Heat treatment furnaces are essential for modifying material properties through controlled heating and cooling processes. The requirements for such furnaces depend on factors like the material being treated, temperature ranges, production volume, and specific treatment processes. Key considerations include furnace design, temperature control, atmosphere regulation, and compatibility with the material and treatment type. Below, we break down the critical requirements and considerations for selecting and operating a heat treatment furnace.
Key Points Explained:
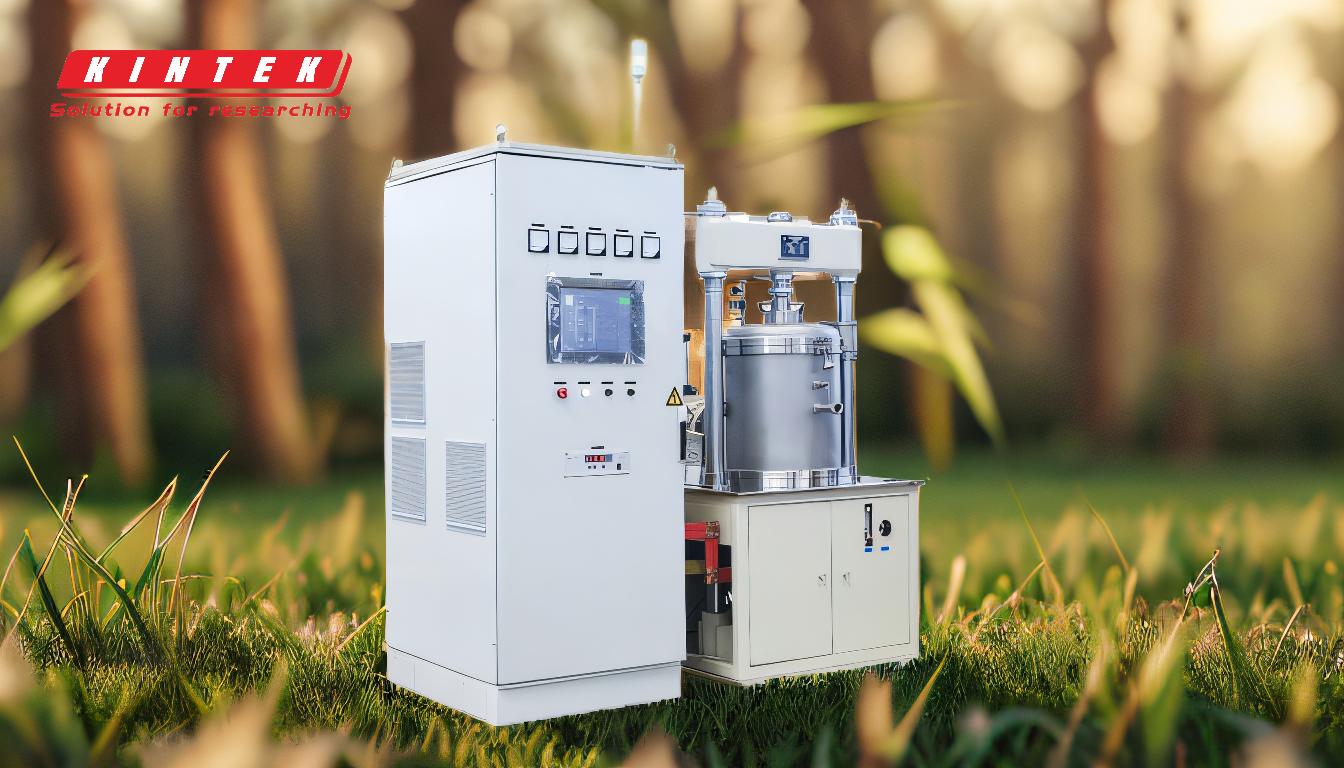
-
Material Compatibility
- The type of material being treated is a primary factor in furnace selection. Different materials (e.g., steel, aluminum, titanium) require specific heat treatment processes such as annealing, hardening, or tempering.
- The furnace must be capable of handling the material's thermal properties, including melting points, thermal conductivity, and expansion rates.
- For example, a furnace designed for steel may not be suitable for aluminum due to differences in temperature requirements and heat distribution.
-
Temperature Range and Control
- Heat treatment furnaces must operate within precise temperature ranges to achieve the desired material properties.
- High-temperature furnaces (e.g., up to 1300°C) are needed for processes like sintering or hardening, while lower-temperature furnaces (e.g., 300°C) are used for processes like tempering.
- Temperature uniformity and control are critical to ensure consistent results. Advanced furnaces use thermocouples and digital controllers to maintain precise temperatures.
-
Furnace Atmosphere
- The atmosphere inside the furnace plays a vital role in preventing oxidation, decarburization, or other surface defects during heat treatment.
- Common furnace atmospheres include inert gases (e.g., nitrogen, argon), vacuum environments, or controlled gas mixtures (e.g., hydrogen, carbon dioxide).
- The choice of atmosphere depends on the material and the desired outcome, such as preventing oxidation in stainless steel or enabling carburization in carbon steel.
-
Production Volume and Throughput
- The furnace must align with the production volume and throughput requirements. Batch furnaces are suitable for smaller production runs, while continuous furnaces are ideal for high-volume operations.
- Factors like cycle time, loading capacity, and automation capabilities should be considered to optimize efficiency and productivity.
-
Furnace Design and Type
- The design of the furnace is determined by the type of stock being treated and the specific heat treatment process.
- Common furnace types include:
- Box furnaces: Suitable for batch processing of small to medium-sized parts.
- Pit furnaces: Ideal for treating long or heavy components.
- Continuous furnaces: Designed for high-volume production with consistent heating and cooling cycles.
- The furnace must also accommodate the size and shape of the components being treated.
-
Heating Method
- Heat treatment furnaces use various heating methods, such as electric resistance, gas, or induction heating.
- Electric furnaces offer precise temperature control and are suitable for clean processes, while gas furnaces are more cost-effective for high-temperature applications.
- Induction heating is ideal for localized heat treatment of specific areas on a component.
-
Energy Efficiency and Environmental Impact
- Modern heat treatment furnaces are designed to minimize energy consumption and reduce environmental impact.
- Features like insulation, heat recovery systems, and efficient burners or heating elements help optimize energy use.
- Compliance with environmental regulations, such as emissions standards, is also a critical consideration.
-
Safety and Maintenance
- Safety features, such as temperature sensors, emergency shut-off systems, and proper ventilation, are essential to prevent accidents and ensure operator safety.
- Regular maintenance is required to maintain furnace performance and extend its lifespan. This includes cleaning, inspecting heating elements, and replacing worn-out components.
-
Process Control and Automation
- Advanced furnaces incorporate automation and process control systems to enhance precision and repeatability.
- Features like programmable logic controllers (PLCs), data logging, and real-time monitoring enable operators to track and adjust parameters for optimal results.
- Automation also reduces human error and improves consistency in large-scale production.
-
Cost and Return on Investment (ROI)
- The initial cost of the furnace, along with operating and maintenance expenses, should be evaluated against the expected ROI.
- Factors like energy efficiency, production capacity, and durability influence the long-term cost-effectiveness of the furnace.
- Customized solutions may be required for specialized applications, which can impact the overall cost.
By carefully considering these requirements, manufacturers can select a heat treatment furnace that meets their specific needs, ensuring high-quality results, operational efficiency, and cost-effectiveness.
Summary Table:
Key Consideration | Details |
---|---|
Material Compatibility | Ensure the furnace supports the material's thermal properties and processes. |
Temperature Range | Match the furnace's range to your process needs (e.g., 300°C to 1300°C). |
Furnace Atmosphere | Choose inert gases, vacuum, or controlled mixtures to prevent defects. |
Production Volume | Select batch or continuous furnaces based on throughput requirements. |
Furnace Design | Options include box, pit, and continuous furnaces for specific applications. |
Heating Method | Electric, gas, or induction heating for precise or cost-effective results. |
Energy Efficiency | Optimize energy use with insulation and heat recovery systems. |
Safety and Maintenance | Ensure safety features and regular maintenance for long-term performance. |
Process Automation | Use PLCs and real-time monitoring for precision and consistency. |
Cost and ROI | Evaluate initial costs, energy efficiency, and durability for ROI. |
Ready to find the perfect heat treatment furnace for your needs? Contact our experts today for personalized guidance!