Heat treating metal involves high temperatures and potentially hazardous materials, making safety a critical consideration. Key safety measures include proper furnace setup, monitoring, and handling of materials. The operating environment must be free of hazards, and specific procedures like nitrogen cooling and proper cooling times must be followed. Safety equipment and tools are essential to prevent accidents. Adhering to these guidelines ensures a safer workplace and minimizes risks associated with heat treatment processes.
Key Points Explained:
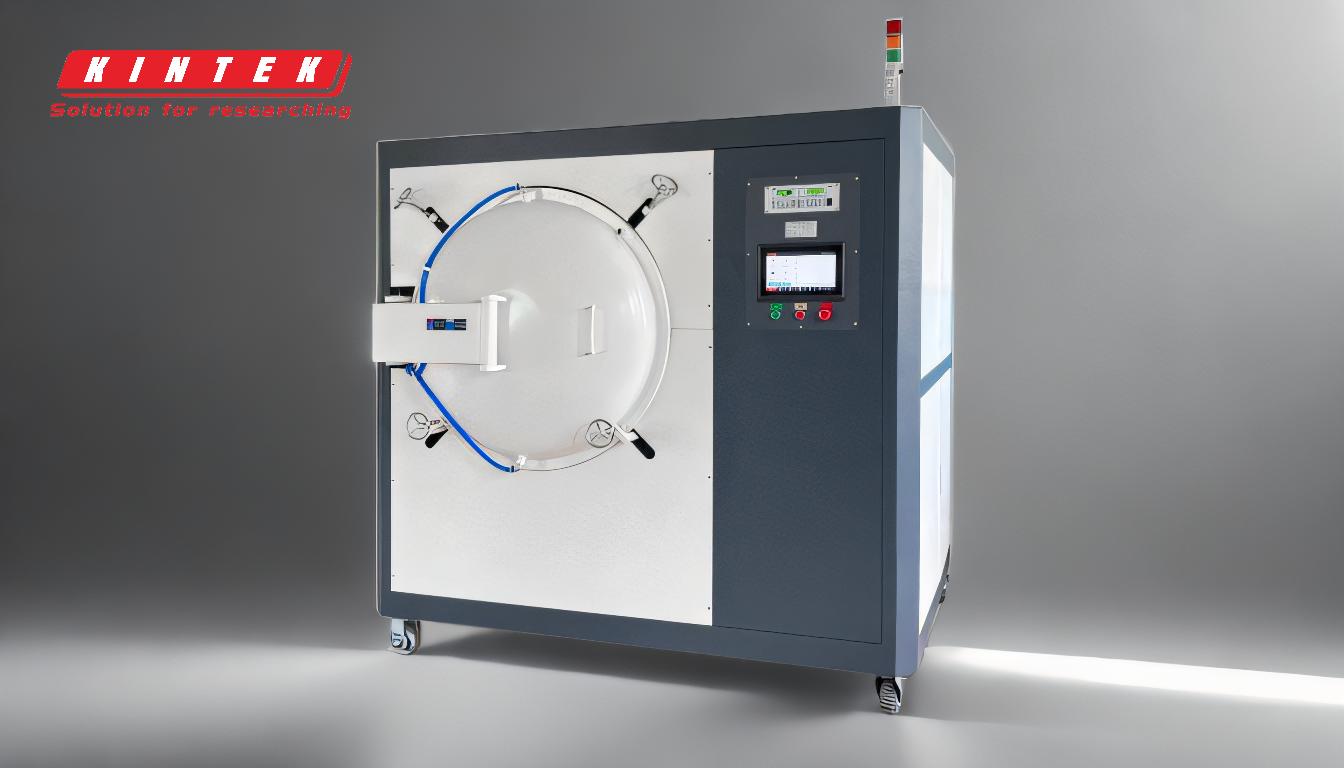
-
Furnace Setup and Stability
- Stable Surface: Ensure the furnace is placed on a stable, level surface to prevent tipping or movement during operation.
- Proper Grounding: The furnace must be properly grounded to avoid electrical hazards.
- Electrical Components: Use appropriate electrical components that can handle the furnace's power requirements to prevent overheating and electrical fires.
-
Operating Environment
- Hazard-Free Area: The area around the furnace should be free of flammable or hazardous materials to reduce the risk of fire or explosions.
- Ventilation: Adequate ventilation is necessary to disperse any fumes or gases that may be released during the heat treatment process.
-
Temperature Monitoring and Control
- Avoid Exceeding Limits: Do not exceed the recommended temperature limits for the furnace and the materials being treated to prevent damage and potential hazards.
- Continuous Monitoring: Regularly monitor the furnace during operation to ensure it is functioning correctly and to detect any anomalies early.
-
Handling Materials and Components
- Careful Handling: Handle samples and furnace components with care to avoid burns or other injuries. Use appropriate tools and protective equipment.
- Transporting and Pouring Melt: Use proper tools to transport and pour molten metal, and always wear safety equipment to protect against splashes and spills.
-
Cooling Procedures
- Nitrogen Cooling: Fill the oil cooling chamber with nitrogen during cooling to enhance safety and cooling efficiency.
- Complete Cooling: Ensure the workpiece is fully cooled and drained of oil before vacuuming the chamber to prevent residual heat from causing accidents.
- Air-Cooling Time: For high alloy die steel materials, strictly adhere to cooling times and allow sufficient air-cooling time to avoid thermal stress and cracking.
-
Post-Operation Safety
- Residual Oil Mist Check: Check for residual oil mist before releasing air into the chamber to prevent fire hazards.
- Furnace Maintenance: After use, power off the furnace and close the door to maintain its condition and prevent accidental activation.
-
Workpiece Placement
- Avoid Overloading: Do not overload the furnace to ensure even heat distribution and prevent mechanical failures.
- Even Placement: Place workpieces evenly in the material basket to avoid uneven heating and potential damage to the furnace or materials.
By following these safety considerations, the risks associated with heat treating metal can be significantly reduced, ensuring a safer and more efficient working environment.
Summary Table:
Safety Measure | Key Actions |
---|---|
Furnace Setup and Stability | Stable surface, proper grounding, appropriate electrical components |
Operating Environment | Hazard-free area, adequate ventilation |
Temperature Monitoring | Avoid exceeding limits, continuous monitoring |
Handling Materials | Use protective equipment, proper tools for molten metal |
Cooling Procedures | Nitrogen cooling, complete cooling, air-cooling time for high alloy materials |
Post-Operation Safety | Check for residual oil mist, power off and maintain furnace |
Workpiece Placement | Avoid overloading, even placement in material basket |
Ensure your heat treatment process is safe and efficient—contact our experts today for personalized advice!