Nanomaterials, due to their unique properties and small size, present several safety concerns that need to be addressed to ensure safe handling and usage. These concerns arise from their potential to interact with biological systems, environmental persistence, and the lack of comprehensive understanding of their long-term effects. Key safety issues include toxicity, environmental impact, occupational hazards, and challenges in risk assessment and regulation. Understanding these risks is crucial for researchers, manufacturers, and policymakers to develop safe practices and guidelines for the use of nanomaterials.
Key Points Explained:
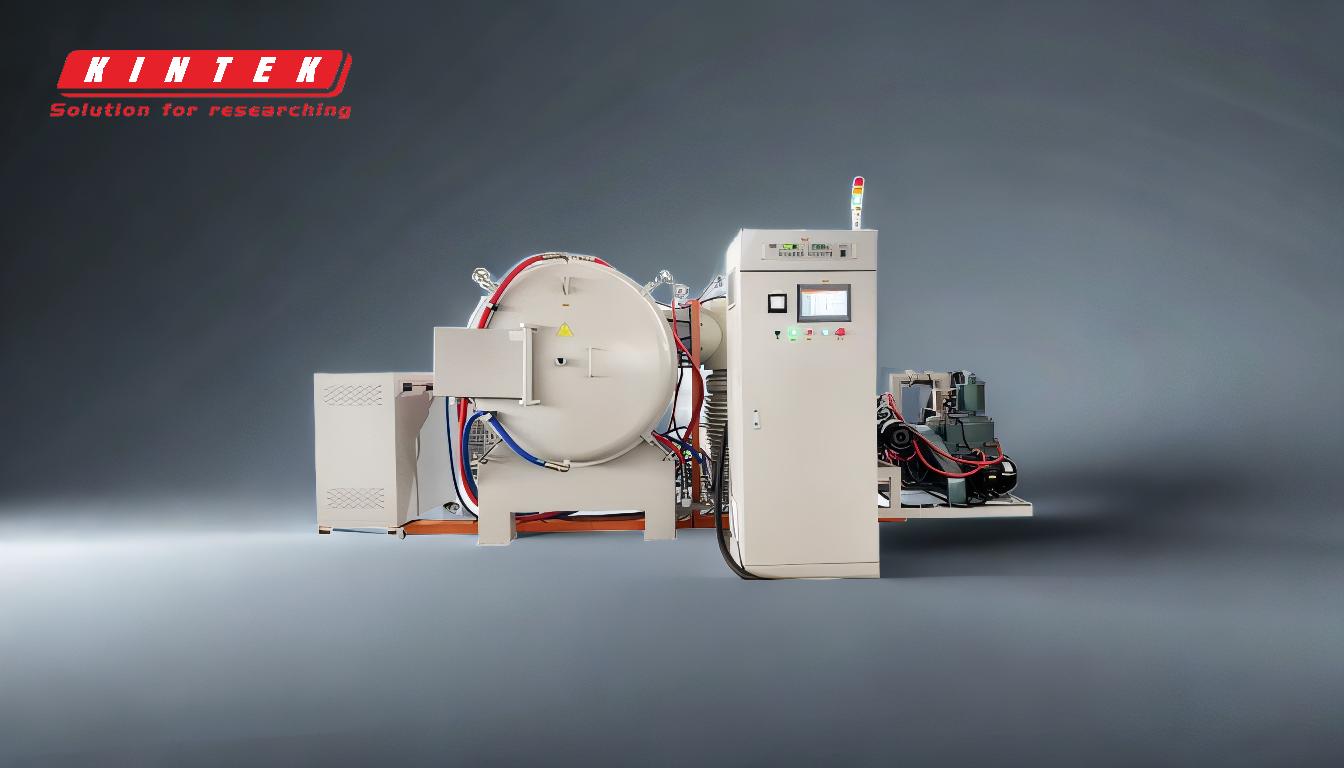
-
Toxicity and Health Risks:
- Size and Reactivity: The small size of nanomaterials allows them to penetrate biological barriers, such as the skin, lungs, and even the blood-brain barrier, potentially leading to unforeseen health risks. Their high surface area-to-volume ratio increases their reactivity, which can result in oxidative stress, inflammation, or cell damage.
- Biodistribution and Accumulation: Nanomaterials can accumulate in organs like the liver, spleen, and kidneys, potentially causing long-term damage. For example, certain nanoparticles have been shown to induce fibrosis or other chronic conditions.
- Lack of Long-Term Studies: There is limited data on the long-term effects of nanomaterial exposure, making it difficult to assess their safety fully.
-
Environmental Impact:
- Persistence and Bioaccumulation: Nanomaterials can persist in the environment and accumulate in ecosystems, potentially affecting wildlife and entering the food chain. For instance, silver nanoparticles used in consumer products have been found in aquatic environments, posing risks to marine life.
- Ecotoxicity: Some nanomaterials, such as titanium dioxide nanoparticles, have been shown to harm aquatic organisms, including fish and algae, by disrupting cellular functions or causing physical damage.
- Recycling and Disposal Challenges: The disposal of nanomaterials is complicated by their small size and potential to contaminate waste streams, raising concerns about their impact on recycling processes and landfill safety.
-
Occupational Hazards:
- Inhalation and Dermal Exposure: Workers involved in the production or handling of nanomaterials are at risk of inhalation or skin contact, which can lead to respiratory issues, skin irritation, or systemic effects. For example, carbon nanotubes have been compared to asbestos in terms of their potential to cause lung damage.
- Lack of Protective Measures: Many workplaces lack adequate safety protocols or protective equipment for handling nanomaterials, increasing the risk of exposure.
- Monitoring and Detection: Current methods for detecting and monitoring nanomaterial exposure in workplaces are often inadequate, making it difficult to assess and mitigate risks effectively.
-
Regulatory and Risk Assessment Challenges:
- Inconsistent Standards: There is a lack of standardized guidelines for the safe use and disposal of nanomaterials, leading to inconsistencies in regulation across industries and countries.
- Data Gaps: The rapid development of nanotechnology has outpaced the generation of safety data, leaving regulators with insufficient information to create comprehensive risk assessments.
- Complexity of Nanomaterials: The diverse properties and behaviors of nanomaterials make it challenging to develop one-size-fits-all safety protocols, requiring tailored approaches for different types of nanomaterials.
-
Public Awareness and Education:
- Lack of Knowledge: Many consumers and workers are unaware of the potential risks associated with nanomaterials, leading to improper handling or disposal.
- Need for Training: Educating researchers, manufacturers, and the public about safe practices is essential to minimize risks and ensure responsible use of nanotechnology.
In conclusion, the safety issues surrounding nanomaterials are multifaceted and require a collaborative effort from scientists, industry leaders, and policymakers to address. By investing in research, developing robust safety protocols, and raising awareness, the potential risks of nanomaterials can be mitigated, allowing society to harness their benefits safely.
Summary Table:
Safety Issue | Key Concerns |
---|---|
Toxicity and Health Risks | - Penetration of biological barriers - Biodistribution and organ accumulation - Lack of long-term studies |
Environmental Impact | - Persistence and bioaccumulation - Ecotoxicity - Recycling and disposal challenges |
Occupational Hazards | - Inhalation and dermal exposure - Lack of protective measures - Monitoring challenges |
Regulatory Challenges | - Inconsistent standards - Data gaps - Complexity of nanomaterials |
Public Awareness | - Lack of knowledge - Need for training and education |
Concerned about nanomaterial safety? Contact our experts today for guidance and solutions!