The Atomic Layer Deposition (ALD) process is a highly precise and controlled method for depositing thin films at the atomic level. It involves a sequence of steps that ensure uniform and conformal film growth. The process begins with the introduction of a precursor gas that forms a monolayer on the substrate surface. Excess precursor is then purged, followed by the introduction of a reactant gas that reacts with the monolayer. The by-products of this reaction are subsequently removed, and the cycle repeats until the desired film thickness is achieved. ALD is known for its ability to produce extremely thin, uniform, and conformal films, making it ideal for applications requiring high precision and control.
Key Points Explained:
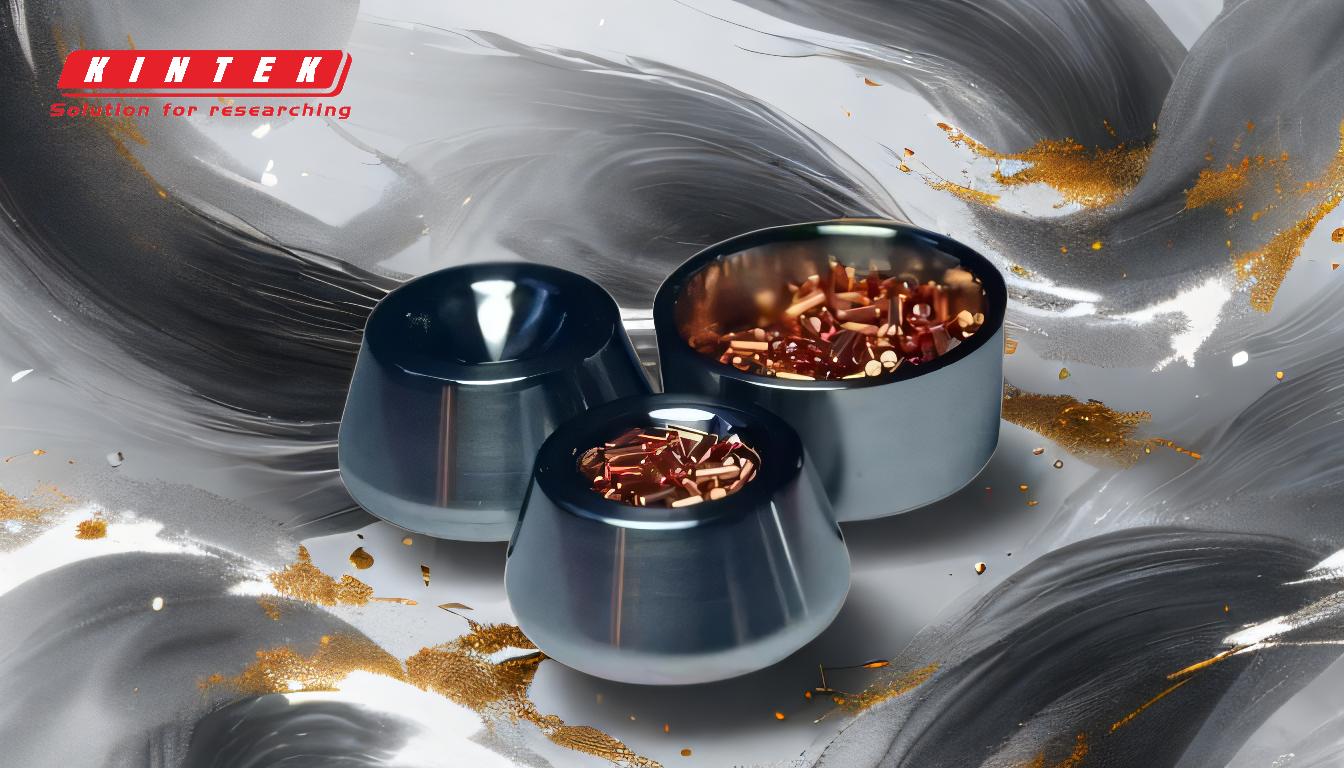
-
Introduction of the First Precursor:
- The ALD process begins with the introduction of the first precursor gas into the reaction chamber.
- This precursor chemically binds to the substrate surface, forming a monolayer. The binding is self-limiting, meaning that once the surface is fully covered, no further precursor will bind, ensuring a uniform layer.
- This step is crucial for achieving atomic-level precision in film deposition.
-
Purging Excess Precursor:
- After the first precursor has formed a monolayer, the chamber is evacuated and purged to remove any excess precursor molecules.
- This step ensures that only the chemically bound monolayer remains on the substrate surface, preventing any unwanted reactions or contamination in subsequent steps.
- Purging is typically done using an inert gas like nitrogen or argon.
-
Introduction of the Reactant:
- The next step involves introducing a reactant gas into the chamber. This reactant reacts with the monolayer formed by the first precursor.
- The reaction between the reactant and the monolayer results in the formation of a new layer of material on the substrate surface.
- Similar to the first step, this reaction is self-limiting, ensuring that only one atomic layer is formed at a time.
-
Purging Reaction By-products:
- After the reaction between the reactant and the monolayer, the chamber is again evacuated and purged to remove any volatile by-products of the reaction.
- This step is essential to prevent contamination and ensure the purity of the deposited film.
- The purging process also prepares the chamber for the next cycle of precursor and reactant introduction.
-
Repetition of the Cycle:
- The entire sequence of precursor introduction, purging, reactant introduction, and purging is repeated multiple times.
- Each cycle results in the deposition of a single atomic layer, and the process continues until the desired film thickness is achieved.
- The number of cycles can range from a few to several hundred, depending on the required film thickness.
-
Controlled Temperature and Environment:
- ALD is performed in a controlled environment with precise temperature regulation. The temperature is typically maintained within a specific range to ensure optimal precursor adsorption and reaction kinetics.
- The controlled environment also helps in achieving uniform film deposition and high-quality film properties.
-
Conformality and Uniformity:
- One of the key advantages of ALD is its ability to produce highly conformal films, even on complex three-dimensional structures with high aspect ratios.
- The self-limiting nature of the reactions ensures that the film thickness is uniform across the entire substrate surface, including features like trenches and vias.
-
Applications of ALD:
- ALD is widely used in the semiconductor industry for depositing thin films on wafers, including high-k dielectrics, metal gates, and barrier layers.
- It is also used in the production of microelectromechanical systems (MEMS), optical coatings, and protective coatings for various materials.
- The precision and control offered by ALD make it suitable for applications requiring nanoscale film deposition.
In summary, the ALD process is a highly controlled and precise method for depositing thin films at the atomic level. It involves a sequence of steps that ensure uniform and conformal film growth, making it ideal for applications requiring high precision and control. The process is characterized by its self-limiting reactions, controlled environment, and ability to produce films with excellent conformality and uniformity.
Summary Table:
Step | Description |
---|---|
1. Introduction of Precursor | Precursor gas forms a self-limiting monolayer on the substrate surface. |
2. Purging Excess Precursor | Excess precursor is removed using inert gas to prevent contamination. |
3. Introduction of Reactant | Reactant gas reacts with the monolayer to form a new atomic layer. |
4. Purging By-products | Volatile by-products are purged to maintain film purity. |
5. Repetition of Cycle | Steps 1-4 are repeated to achieve the desired film thickness. |
6. Controlled Environment | Precise temperature and environment ensure uniform and high-quality film growth. |
7. Conformality & Uniformity | ALD produces highly conformal films on complex 3D structures. |
8. Applications | Used in semiconductors, MEMS, optical coatings, and protective layers. |
Discover how ALD can revolutionize your thin film processes—contact our experts today!