Carbon nanotubes (CNTs) are one-dimensional nanostructures with remarkable mechanical, electrical, and thermal properties, making them a focal point in nanotechnology research. The techniques for synthesizing and manipulating carbon nanotubes are diverse, each with its own advantages and limitations. These techniques include chemical vapor deposition (CVD), arc discharge, laser ablation, and more. Additionally, post-synthesis processing methods such as functionalization, purification, and alignment are critical for tailoring CNTs for specific applications. Understanding these techniques is essential for researchers and industries aiming to harness the full potential of carbon nanotubes in fields like electronics, energy storage, and materials science.
Key Points Explained:
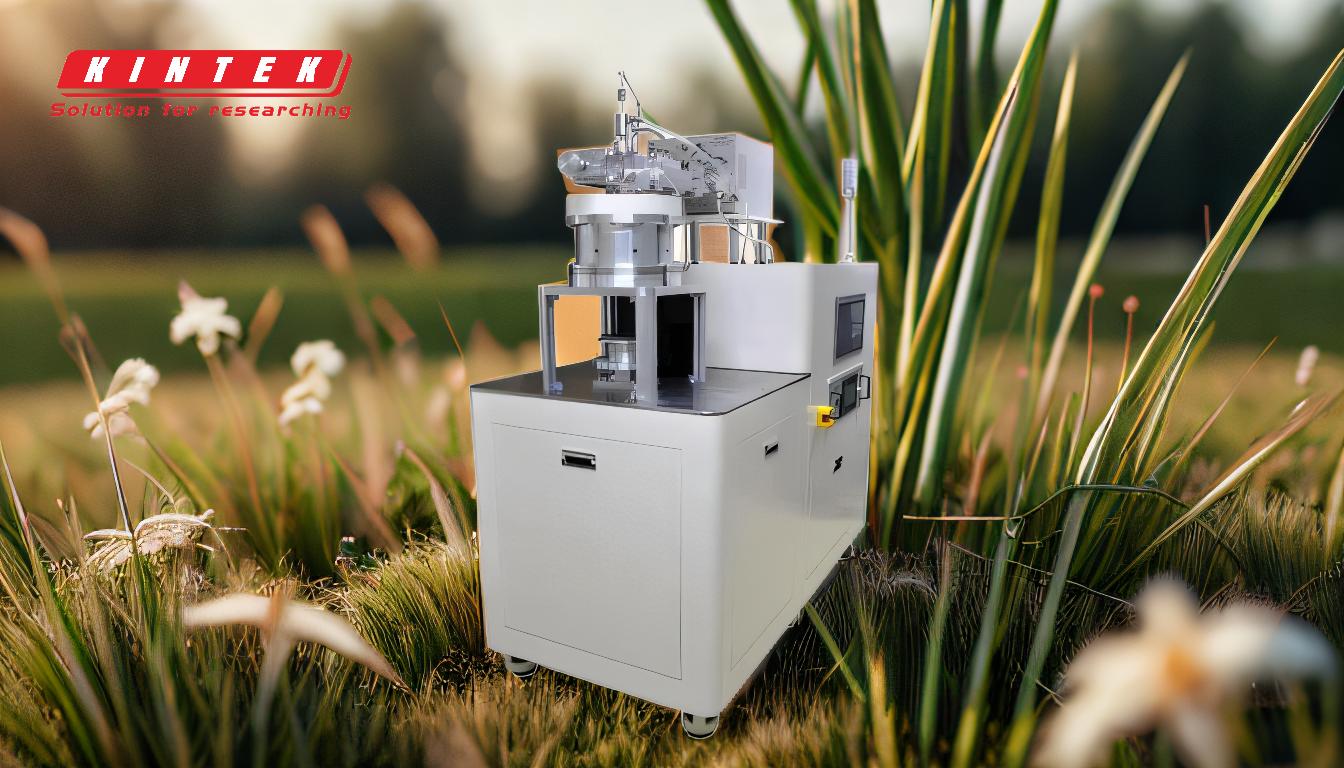
-
Chemical Vapor Deposition (CVD):
- CVD is the most widely used technique for synthesizing carbon nanotubes due to its scalability and ability to produce high-quality CNTs.
- In this method, a carbon-containing gas (e.g., methane or ethylene) is decomposed at high temperatures (600–1200°C) in the presence of a metal catalyst (e.g., iron, cobalt, or nickel).
- The catalyst particles act as nucleation sites for CNT growth, enabling the formation of single-walled (SWCNTs) or multi-walled carbon nanotubes (MWCNTs).
- CVD allows precise control over CNT diameter, length, and alignment, making it suitable for industrial applications.
-
Arc Discharge:
- Arc discharge is one of the earliest methods for CNT synthesis and involves creating an electric arc between two graphite electrodes in an inert gas atmosphere.
- The high temperatures generated (up to 4000°C) vaporize the carbon, which then condenses to form CNTs.
- This method is known for producing high-quality CNTs, but it is less scalable and less controllable compared to CVD.
- It is often used for producing MWCNTs and requires post-synthesis purification to remove impurities like amorphous carbon and metal particles.
-
Laser Ablation:
- In laser ablation, a high-powered laser is used to vaporize a graphite target containing a metal catalyst in a high-temperature furnace.
- The vaporized carbon condenses into CNTs as it cools.
- This technique is capable of producing high-purity SWCNTs but is energy-intensive and less scalable than CVD.
- It is primarily used in research settings where high-quality CNTs are required.
-
Post-Synthesis Processing:
- Purification: As-synthesized CNTs often contain impurities such as metal catalysts and amorphous carbon. Purification techniques include oxidation, acid treatment, and filtration to isolate high-purity CNTs.
- Functionalization: Chemical functionalization involves attaching functional groups (e.g., carboxyl or hydroxyl groups) to the CNT surface to improve solubility, dispersion, and compatibility with other materials.
- Alignment: For applications like field-emission displays or nanocomposites, CNTs need to be aligned. Techniques such as mechanical stretching, magnetic field alignment, and template-assisted growth are used to achieve this.
-
Emerging Techniques:
- Plasma-Enhanced CVD (PECVD): This variation of CVD uses plasma to lower the synthesis temperature, enabling CNT growth on temperature-sensitive substrates.
- Electrochemical Synthesis: A relatively new method where CNTs are grown electrochemically from carbon-containing electrolytes, offering potential for low-temperature and scalable production.
- Green Synthesis: Researchers are exploring environmentally friendly methods using renewable carbon sources and low-energy processes to synthesize CNTs.
-
Applications and Challenges:
- CNTs are used in a wide range of applications, including transistors, sensors, batteries, supercapacitors, and composite materials.
- Despite their potential, challenges remain in achieving large-scale, cost-effective production, controlling CNT properties consistently, and addressing potential environmental and health risks.
By understanding these techniques, researchers and industries can select the most appropriate method for their specific needs, paving the way for innovative applications of carbon nanotubes in various fields.
Summary Table:
Technique | Description | Advantages | Limitations |
---|---|---|---|
Chemical Vapor Deposition (CVD) | Decomposes carbon-containing gas at high temps with a metal catalyst. | Scalable, high-quality CNTs, precise control. | Requires high temperatures, costly equipment. |
Arc Discharge | Electric arc between graphite electrodes in inert gas. | High-quality CNTs, simple setup. | Less scalable, requires purification. |
Laser Ablation | High-powered laser vaporizes graphite target. | High-purity SWCNTs, suitable for research. | Energy-intensive, less scalable. |
Post-Synthesis Processing | Includes purification, functionalization, and alignment. | Tailors CNTs for specific applications. | Additional steps increase complexity. |
Emerging Techniques | Includes PECVD, electrochemical synthesis, and green synthesis. | Lower temps, scalable, eco-friendly options. | Still under development, limited scalability. |
Unlock the potential of carbon nanotubes for your research or industry—contact our experts today!