Quenching is a critical process in metallurgy and materials science, where heated materials are rapidly cooled to achieve specific mechanical properties, such as increased hardness or strength. The three primary types of quenching are oil quenching, water quenching, and air quenching, each suited to different materials and desired outcomes. Oil quenching is commonly used for its moderate cooling rate, which minimizes distortion and cracking. Water quenching provides a faster cooling rate, ideal for materials requiring high hardness, but it can increase the risk of cracking. Air quenching, on the other hand, offers the slowest cooling rate, suitable for materials that are prone to distortion or cracking under rapid cooling. The choice of quenching medium depends on the material's properties and the desired mechanical characteristics.
Key Points Explained:
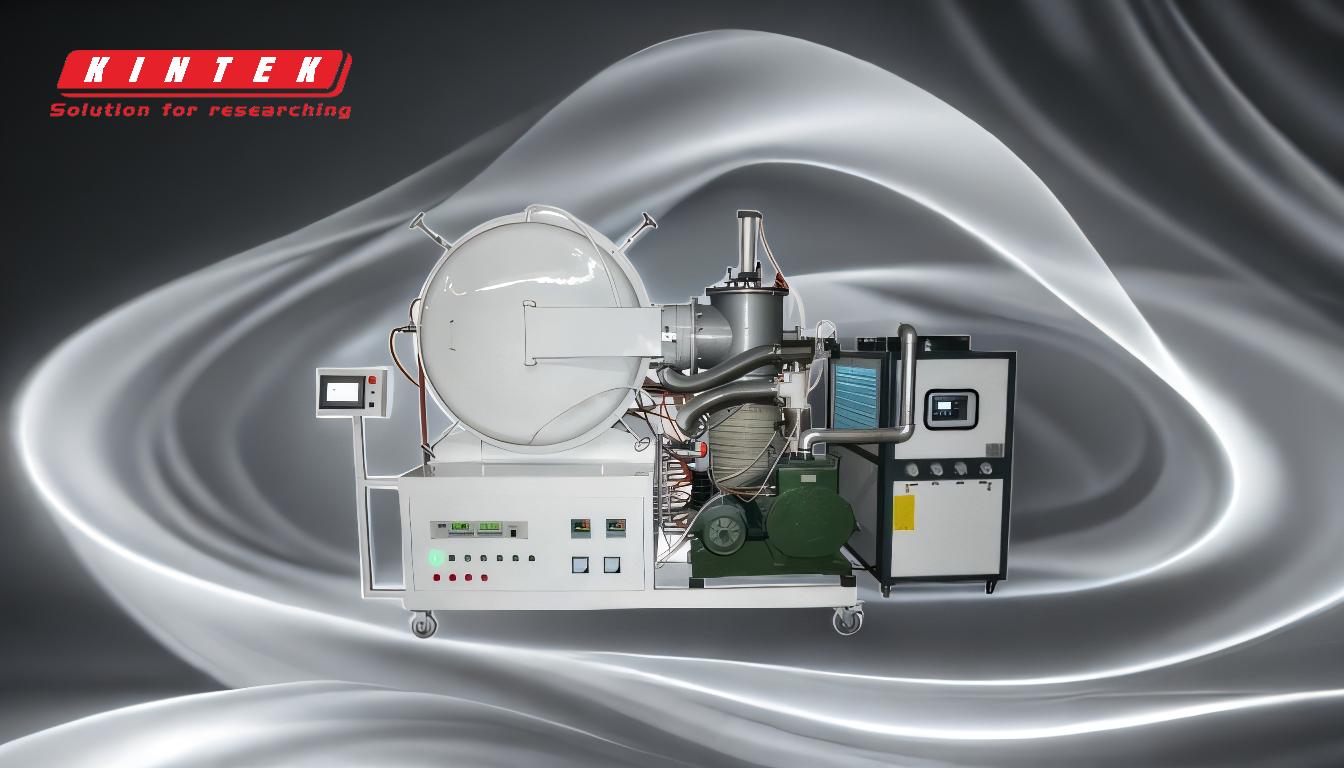
-
Oil Quenching:
- Oil quenching is one of the most widely used quenching methods due to its moderate cooling rate.
- It is particularly suitable for medium and high-carbon steels, as it reduces the risk of cracking and distortion compared to faster cooling methods.
- The oil acts as a heat transfer medium, providing a controlled cooling process that balances hardness and toughness.
- This method is often preferred for complex or intricate parts where minimizing stress is critical.
-
Water Quenching:
- Water quenching provides a much faster cooling rate compared to oil, making it ideal for achieving high hardness in materials.
- It is commonly used for low-carbon steels and certain alloys that require rapid cooling to achieve desired mechanical properties.
- However, the fast cooling rate can lead to increased internal stresses, making parts more susceptible to cracking or distortion.
- Careful control of the quenching process is necessary to avoid these issues, especially for large or thick sections.
-
Air Quenching:
- Air quenching involves cooling the material in still or forced air, offering the slowest cooling rate among the three methods.
- This method is suitable for materials that are highly sensitive to rapid cooling, such as certain tool steels and high-alloy steels.
- Air quenching minimizes the risk of cracking and distortion, making it ideal for parts with complex geometries or thin cross-sections.
- While it may not achieve the same level of hardness as oil or water quenching, it provides a good balance of strength and ductility.
-
Factors Influencing Quenching Choice:
- The choice of quenching medium depends on the material's composition, desired mechanical properties, and part geometry.
- For example, high-carbon steels often require oil quenching to achieve a balance of hardness and toughness, while low-carbon steels may benefit from water quenching for maximum hardness.
- Air quenching is typically reserved for materials that are prone to cracking or distortion under rapid cooling.
- The cooling rate, part size, and complexity of the geometry also play a significant role in determining the most appropriate quenching method.
By understanding the differences between oil, water, and air quenching, manufacturers can select the most suitable method to achieve the desired material properties while minimizing the risk of defects. Each method has its advantages and limitations, and the choice depends on the specific requirements of the material and application.
Summary Table:
Quenching Method | Cooling Rate | Best For | Key Benefits | Limitations |
---|---|---|---|---|
Oil Quenching | Moderate | Medium/high-carbon steels | Minimizes distortion and cracking | Slower cooling rate |
Water Quenching | Fast | Low-carbon steels, certain alloys | Achieves high hardness | Risk of cracking/distortion |
Air Quenching | Slowest | Tool steels, high-alloy steels | Minimizes cracking, ideal for complex parts | Lower hardness levels |
Need help selecting the right quenching method for your materials? Contact our experts today for personalized advice!