Press machines are essential tools in various industries, and they are primarily classified into two main types based on the method of applying pressure: axial-pressing and isostatic-pressing. Axial-pressing involves applying rigid pressure in a single direction, typically using a mechanical or hydraulic press, and is commonly used for shaping materials like ceramics, metals, and powders. Isostatic-pressing, on the other hand, applies flexible, uniform pressure from all directions using a fluid medium, making it ideal for creating complex shapes and ensuring uniform density in materials. These classifications are crucial for selecting the right press machine for specific applications, as each method offers distinct advantages depending on the material properties and desired outcomes.
Key Points Explained:
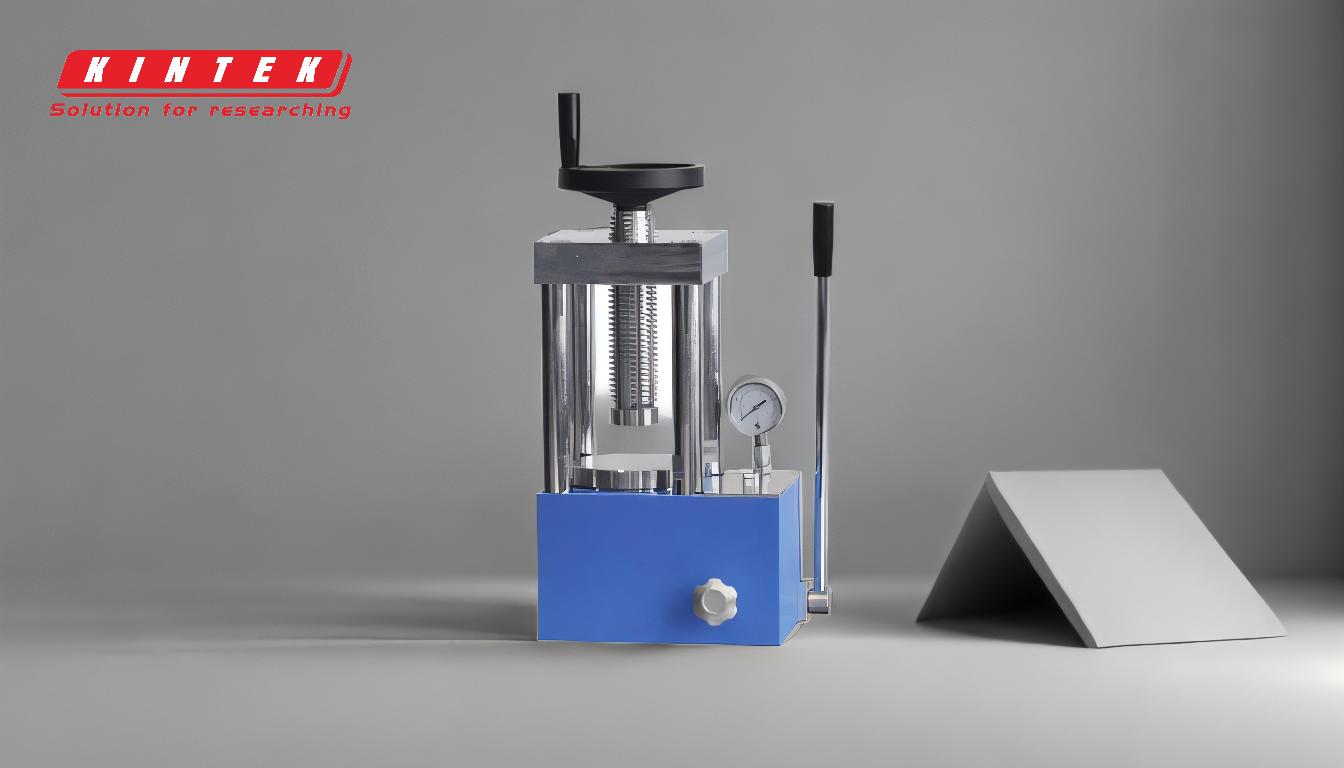
-
Axial-Pressing
- Definition: Axial-pressing, also known as uniaxial pressing, involves applying rigid pressure in a single direction, typically using a mechanical or hydraulic press.
- Mechanism: The pressure is applied through a punch or die, compressing the material into a specific shape or form.
- Applications: This method is widely used in industries such as ceramics, metallurgy, and powder metallurgy for shaping materials like powders, metals, and composites.
-
Advantages:
- High production speed due to straightforward operation.
- Suitable for producing simple shapes with consistent dimensions.
- Cost-effective for large-scale manufacturing.
-
Limitations:
- Limited to simpler geometries due to unidirectional pressure.
- Potential for density variations in the final product.
-
Isostatic-Pressing
- Definition: Isostatic-pressing involves applying flexible, uniform pressure from all directions using a fluid medium, such as oil or water.
- Mechanism: The material is placed in a flexible mold or container, which is then subjected to high pressure from all sides, ensuring uniform compression.
- Applications: This method is ideal for creating complex shapes and ensuring uniform density in materials, making it suitable for advanced ceramics, aerospace components, and medical implants.
-
Advantages:
- Uniform density and microstructure in the final product.
- Capable of producing complex shapes with high precision.
- Reduces the risk of defects like cracks or voids.
-
Limitations:
- Higher equipment and operational costs compared to axial-pressing.
- Slower production rates due to the complexity of the process.
-
Comparison of Axial-Pressing and Isostatic-Pressing
- Pressure Application: Axial-pressing applies pressure in one direction, while isostatic-pressing applies pressure uniformly from all directions.
- Shape Complexity: Axial-pressing is better suited for simpler shapes, whereas isostatic-pressing excels in creating complex geometries.
- Material Density: Isostatic-pressing ensures more uniform material density compared to axial-pressing, which may have density variations.
- Cost and Efficiency: Axial-pressing is more cost-effective and efficient for large-scale production, while isostatic-pressing is preferred for high-precision and high-performance applications.
-
Choosing the Right Press Machine
- Material Properties: Consider the material's compressibility, flowability, and desired final properties.
- Product Requirements: Evaluate the shape complexity, dimensional accuracy, and density uniformity needed for the final product.
- Production Scale: Axial-pressing is more suitable for high-volume production, while isostatic-pressing is better for specialized, low-volume applications.
- Budget Constraints: Factor in the initial investment, operational costs, and maintenance requirements of each method.
By understanding the differences between axial-pressing and isostatic-pressing, manufacturers can make informed decisions about the most appropriate press machine for their specific needs, ensuring optimal results in terms of product quality, efficiency, and cost-effectiveness.
Summary Table:
Aspect | Axial-Pressing | Isostatic-Pressing |
---|---|---|
Pressure Application | Single direction | Uniform pressure from all directions |
Shape Complexity | Simple shapes | Complex geometries |
Material Density | Potential density variations | Uniform density |
Cost & Efficiency | Cost-effective for large-scale production | Higher cost, slower production |
Applications | Ceramics, metals, powders | Aerospace, medical implants, advanced ceramics |
Need help choosing the right press machine? Contact our experts today for personalized advice!