Injection molding is a versatile manufacturing process used to produce parts by injecting molten material into a mold. Among the various types of injection molding processes, two of the most common are Thermoplastic Injection Molding and Gas-Assisted Injection Molding. Thermoplastic Injection Molding is widely used due to its ability to produce durable and high-quality parts efficiently, while Gas-Assisted Injection Molding is favored for creating complex, hollow, or lightweight parts with improved structural integrity. These processes are essential in industries ranging from automotive to consumer goods, offering unique benefits depending on the application and material requirements.
Key Points Explained:
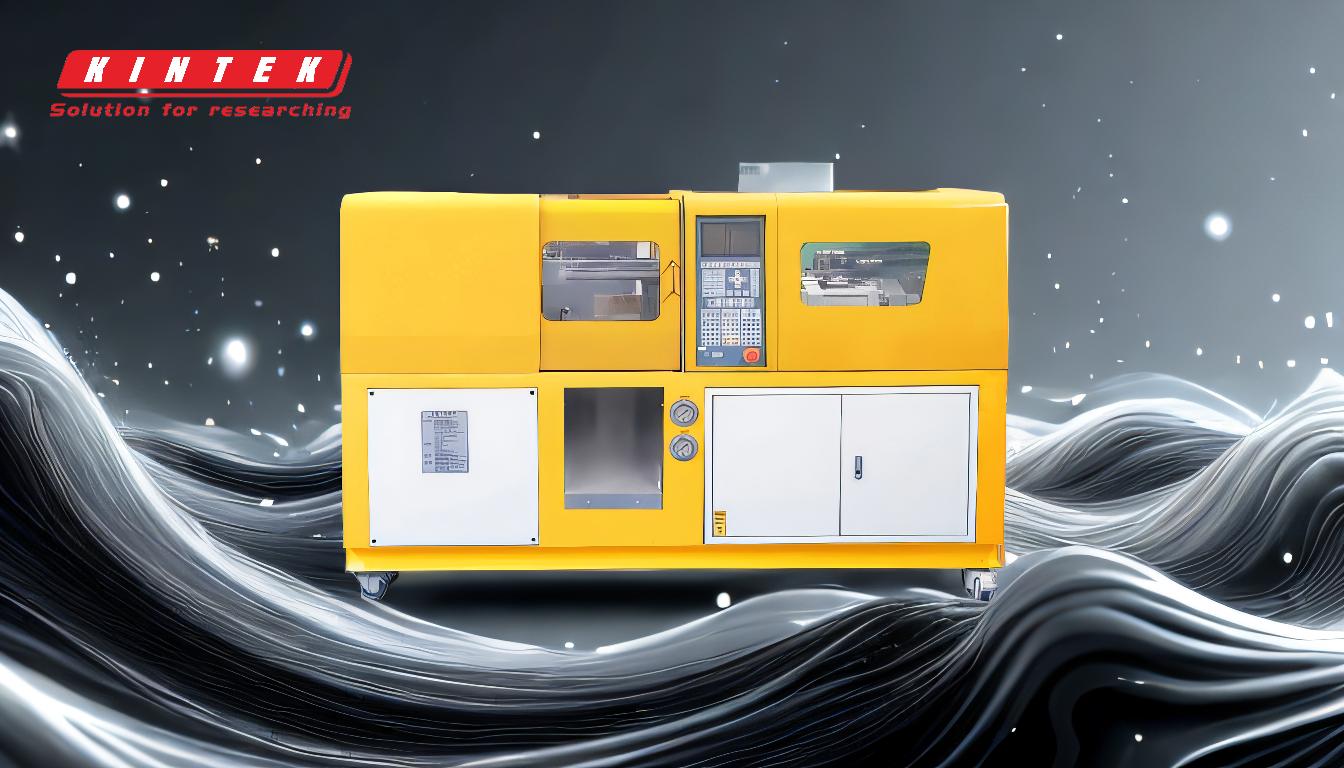
-
Thermoplastic Injection Molding
- Definition: This process involves injecting molten thermoplastic material into a press mold cavity, where it cools and solidifies into the desired shape.
-
Key Features:
- Material Versatility: Thermoplastics, such as polyethylene, polypropylene, and ABS, are commonly used due to their ability to be melted and reshaped multiple times without significant degradation.
- High Efficiency: The process is highly automated, enabling rapid production of large volumes of parts with consistent quality.
- Applications: Widely used in manufacturing consumer goods, automotive components, medical devices, and packaging.
-
Advantages:
- Cost-effective for high-volume production.
- Excellent surface finish and dimensional accuracy.
- Recyclability of thermoplastic materials.
-
Limitations:
- Initial tooling costs can be high.
- Limited to materials that can withstand the melting and cooling process.
-
Gas-Assisted Injection Molding
- Definition: This process involves injecting molten material into a mold, followed by the introduction of pressurized gas (usually nitrogen) to create hollow sections or improve part structure. The use of a nitrogen atmosphere furnace ensures precise control over the gas environment.
-
Key Features:
- Hollow Sections: The gas displaces the molten material in specific areas, creating lightweight, hollow parts.
- Improved Structural Integrity: The gas pressure helps reduce sink marks and warping, resulting in stronger, more uniform parts.
- Applications: Ideal for producing large, complex parts such as automotive panels, furniture, and handles.
-
Advantages:
- Reduces material usage and part weight.
- Enhances part strength and surface finish.
- Minimizes defects like sink marks and warping.
-
Limitations:
- Requires precise control of gas pressure and timing.
- Higher complexity and cost compared to standard injection molding.
-
Comparison of the Two Processes
- Material Usage: Thermoplastic Injection Molding typically uses more material, while Gas-Assisted Injection Molding reduces material consumption by creating hollow sections.
- Part Complexity: Gas-Assisted Injection Molding is better suited for producing complex, lightweight parts with internal voids.
- Cost Considerations: Thermoplastic Injection Molding is generally more cost-effective for simpler, high-volume parts, whereas Gas-Assisted Injection Molding is preferred for specialized applications requiring lightweight and strong components.
-
Choosing the Right Process
- For high-volume production of standard parts, Thermoplastic Injection Molding is often the best choice due to its efficiency and lower operational complexity.
- For complex, lightweight, or structurally demanding parts, Gas-Assisted Injection Molding provides superior results despite its higher cost and complexity.
By understanding these two common types of injection molding processes, manufacturers can select the most appropriate method based on their specific requirements, ensuring optimal performance, cost-efficiency, and product quality.
Summary Table:
Aspect | Thermoplastic Injection Molding | Gas-Assisted Injection Molding |
---|---|---|
Material Usage | Higher material consumption | Reduced material usage (hollow sections) |
Part Complexity | Simpler parts | Complex, lightweight parts |
Cost | Cost-effective for high-volume production | Higher cost, specialized applications |
Applications | Consumer goods, automotive, medical devices | Automotive panels, furniture, handles |
Advantages | High efficiency, recyclability, surface finish | Lightweight, strong, reduced defects |
Limitations | High initial tooling costs | Requires precise gas control |
Need help choosing the right injection molding process? Contact our experts today for tailored solutions!