Corrosion prevention in metals is crucial for maintaining their structural integrity and longevity. Two primary methods are commonly used: protective coatings and cathodic protection. Protective coatings act as a barrier between the metal and its environment, preventing exposure to corrosive elements. Cathodic protection, on the other hand, involves altering the electrochemical properties of the metal to make it less susceptible to corrosion. These methods are widely applied in industries such as construction, automotive, and marine engineering to ensure the durability of metal structures and components.
Key Points Explained:
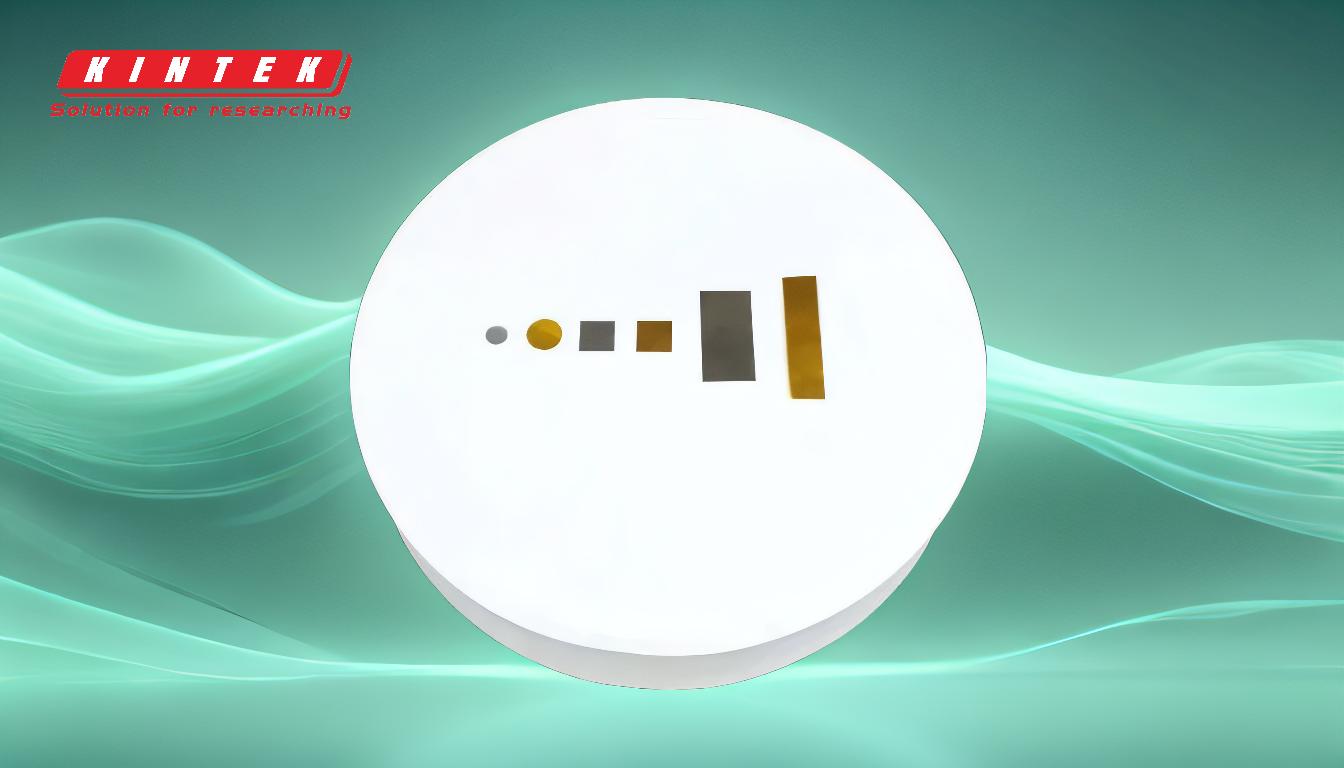
-
Protective Coatings:
- Definition: Protective coatings are materials applied to the surface of a metal to create a barrier that prevents direct contact with corrosive elements such as moisture, oxygen, and chemicals.
-
Types of Coatings:
- Paints and Varnishes: These are the most common types of coatings, providing a cost-effective and versatile solution for corrosion prevention.
- Powder Coatings: Applied electrostatically and cured under heat, these coatings offer a durable and uniform protective layer.
- Galvanization: This involves coating the metal with a layer of zinc, which acts as a sacrificial anode, corroding in place of the underlying metal.
- Anodizing: Primarily used for aluminum, this electrochemical process creates a thick oxide layer that enhances corrosion resistance.
-
Advantages:
- Easy to apply and maintain.
- Can be customized for specific environmental conditions.
- Provides both aesthetic and functional benefits.
-
Limitations:
- Coatings may degrade over time and require reapplication.
- Improper application can lead to uneven protection.
-
Cathodic Protection:
- Definition: Cathodic protection is a technique that makes the metal surface the cathode of an electrochemical cell, thereby reducing or eliminating corrosion.
-
Types of Cathodic Protection:
- Sacrificial Anode Method: Involves attaching a more reactive metal (e.g., magnesium or zinc) to the protected metal. The sacrificial anode corrodes instead of the protected metal.
- Impressed Current Method: Uses an external power source to supply a continuous electrical current to the metal, counteracting the corrosion process.
-
Applications:
- Widely used in pipelines, ship hulls, and underground storage tanks.
- Effective in environments where coatings alone may not suffice, such as highly corrosive soils or seawater.
-
Advantages:
- Provides long-term protection, especially in harsh environments.
- Can be combined with protective coatings for enhanced effectiveness.
-
Limitations:
- Requires careful monitoring and maintenance.
- Initial setup costs can be high, particularly for impressed current systems.
-
Comparison of the Two Methods:
- Protective Coatings are more suitable for applications where aesthetics and ease of application are important, while Cathodic Protection is preferred for long-term protection in highly corrosive environments.
- Both methods can be used in combination to achieve optimal results, as coatings provide immediate protection, and cathodic protection ensures sustained resistance to corrosion.
-
Considerations for Equipment and Consumable Purchasers:
- Cost: Protective coatings are generally more cost-effective upfront, but cathodic protection may offer better long-term value in corrosive environments.
- Durability: Cathodic protection is more durable in extreme conditions, whereas coatings may require periodic maintenance.
- Application Complexity: Coatings are easier to apply, but cathodic protection systems require specialized knowledge and equipment.
- Environmental Factors: The choice of method should consider the specific environmental conditions the metal will be exposed to, such as humidity, salinity, or chemical exposure.
By understanding these methods and their respective advantages and limitations, purchasers can make informed decisions to ensure the longevity and performance of metal equipment and structures.
Summary Table:
Method | Types | Advantages | Limitations |
---|---|---|---|
Protective Coatings | Paints, varnishes, powder coatings, galvanization, anodizing | Easy to apply, customizable, aesthetic and functional benefits | May degrade over time, improper application can lead to uneven protection |
Cathodic Protection | Sacrificial anode method, impressed current method | Long-term protection, effective in harsh environments | Requires monitoring, high initial setup costs |
Need help selecting the right corrosion prevention method for your needs? Contact our experts today for personalized advice!