Arc furnaces are critical equipment in metallurgical processes, primarily used for melting metals and alloys. They are categorized based on their design, power source, and application. The most common types include three-phase alternating current (AC) arc furnaces and direct current (DC) arc furnaces. These furnaces vary in size, ranging from small units for specialized applications to large industrial-scale furnaces capable of handling hundreds of tons of material. The choice of furnace depends on factors such as energy efficiency, operational requirements, and the specific metallurgical process.
Key Points Explained:
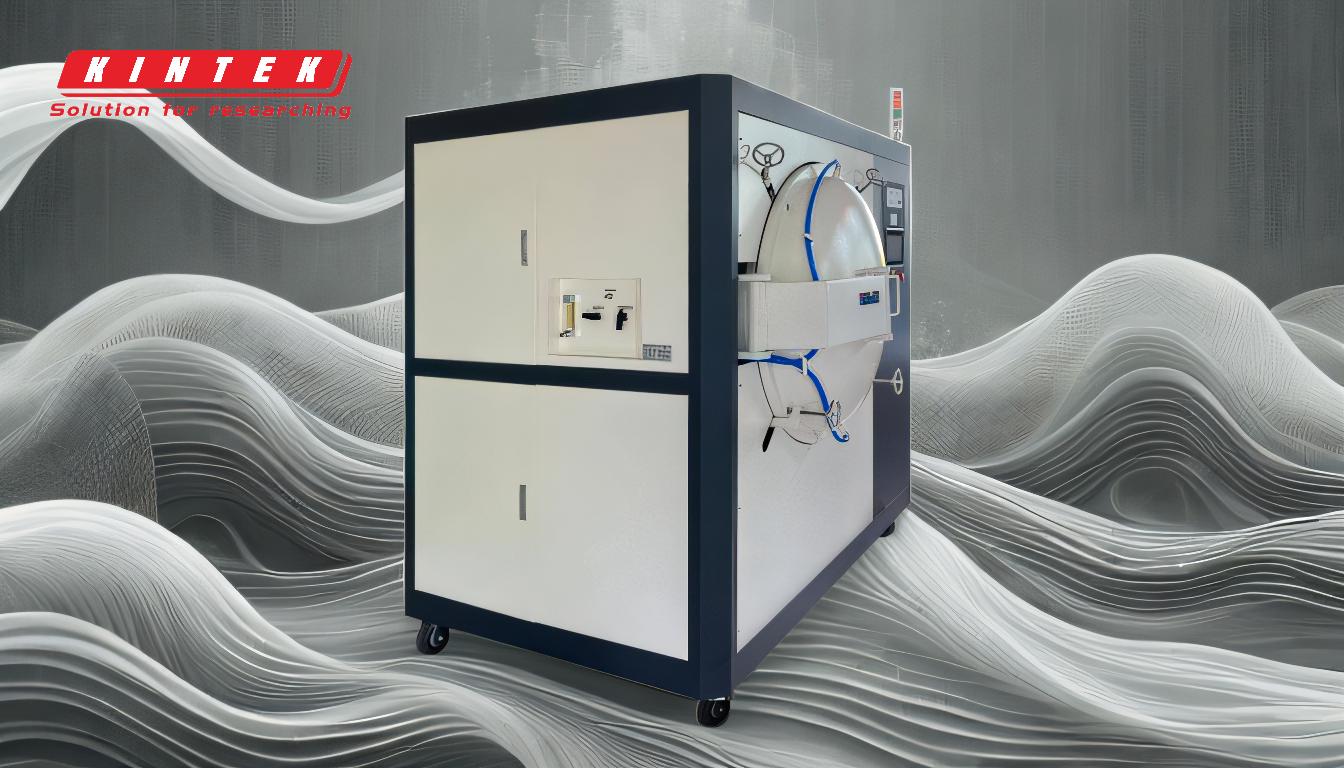
-
Three-Phase Alternating Current (AC) Arc Furnaces:
- These are the most widely used type of arc furnaces in the industry.
- They typically feature three vertically positioned graphite electrodes, which strike arcs directly into the metal bath.
- The three-phase AC design ensures uniform heating and efficient melting of metals.
- They are suitable for large-scale operations, with capacities ranging from a few tons to over 400 tons.
- AC arc furnaces are preferred for their reliability and ability to handle a wide range of materials.
-
Direct Current (DC) Arc Furnaces:
- DC arc furnaces use a single graphite electrode and are powered by direct current.
- They have gained popularity in recent years due to their energy efficiency and reduced electrode consumption.
- The single-electrode design simplifies the furnace structure and reduces maintenance requirements.
- DC arc furnaces are particularly effective for processes requiring precise temperature control and lower electrical noise.
- They are often used in smaller-scale operations or specialized applications.
-
Size and Capacity:
- Arc furnaces are available in a wide range of sizes, from small units for laboratory or pilot-scale applications to large industrial furnaces.
- The capacity of an arc furnace is a critical factor in determining its suitability for specific processes.
- Larger furnaces are typically used in steelmaking and other high-volume metallurgical operations.
-
Applications:
- Arc furnaces are primarily used for melting metals and alloys, including steel, iron, and non-ferrous metals.
- They are also employed in recycling processes, where scrap metal is melted and refined.
- The versatility of arc furnaces makes them suitable for various industries, including automotive, construction, and aerospace.
-
Energy Efficiency and Environmental Considerations:
- Modern arc furnaces are designed to optimize energy consumption and reduce environmental impact.
- DC arc furnaces, in particular, are known for their lower energy requirements and reduced emissions.
- The choice of furnace type can significantly influence the overall sustainability of the metallurgical process.
By understanding the different types of arc furnaces and their applications, purchasers can make informed decisions based on their specific operational needs and sustainability goals.
Summary Table:
Type | Key Features | Applications |
---|---|---|
AC Arc Furnaces | - Three graphite electrodes - Uniform heating - High capacity (up to 400 tons) |
- Large-scale steelmaking - Melting metals and alloys - High-volume operations |
DC Arc Furnaces | - Single graphite electrode - Energy-efficient - Precise temperature control |
- Smaller-scale operations - Specialized applications - Reduced emissions |
Size & Capacity | - Ranges from small lab units to large industrial furnaces | - Tailored to specific process needs |
Energy Efficiency | - DC furnaces reduce energy consumption and emissions | - Sustainable metallurgical processes |
Ready to find the perfect arc furnace for your operations? Contact us today to learn more!