Heat treatment furnaces are categorized based on their temperature ranges, applications, and heat sources. These furnaces are essential for processes like annealing, hardening, tempering, and carburizing, each requiring specific temperature ranges and environmental conditions. The choice of furnace depends on the material being treated, the desired outcome, and operational efficiency. Heat treatment furnaces can be classified into low-temperature (0–700°C), general-purpose (700–1050°C), and high-temperature (1000–1400°C) furnaces. Additionally, they are categorized by heat sources, such as solid, liquid, or gaseous fuels, and specific designs like rotary drum or roller hearth kilns.
Key Points Explained:
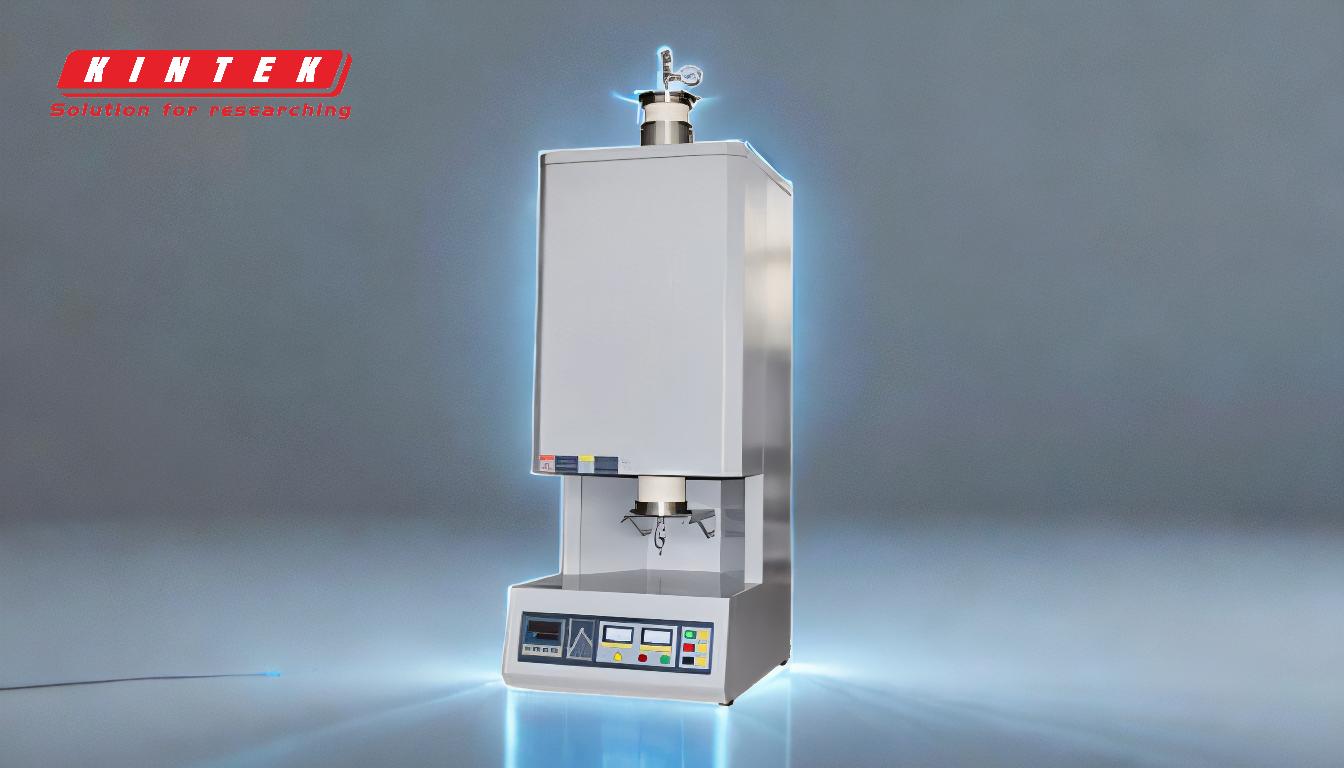
-
Classification by Temperature Range:
-
Low-Temperature Furnaces (0–700°C):
- Used for tempering and sub-critical annealing of steel.
- Operate with dry furnaces featuring forced air circulation or liquid baths (oil, lead, or salt).
- Ideal for processes requiring precise control at lower temperatures.
-
General-Purpose Furnaces (700–1050°C):
- Suitable for hardening, normalizing, and carburizing of carbon and low-alloy steels.
- Versatile and widely used in industrial settings.
-
High-Temperature Furnaces (1000–1400°C):
- Designed for heat treatment of high-speed steels and other high-temperature cycles.
- Essential for applications requiring extreme heat resistance.
-
Low-Temperature Furnaces (0–700°C):
-
Classification by Heat Source:
-
Solid Fuels (e.g., coal, pulverized coal, coke):
- Economical and widely available.
- Suitable for large-scale industrial operations.
-
Liquid Fuels (e.g., gasoline, kerosene):
- Provide consistent and controllable heat.
- Used in applications requiring precise temperature regulation.
-
Gaseous Fuels (e.g., coal gas, producer gas):
- Cleaner and more efficient than solid fuels.
- Preferred for environmentally sensitive operations.
-
Solid Fuels (e.g., coal, pulverized coal, coke):
-
Classification by Design and Application:
-
Drying Ovens:
- Used for drying and curing materials at controlled temperatures.
- Common in laboratories and small-scale industrial applications.
-
Muffle Furnaces:
- Provide a controlled, oxygen-free environment for heat treatment.
- Ideal for processes requiring high precision and contamination-free conditions.
-
Laboratory Incubators:
- Designed for low-temperature applications like biological testing.
- Ensure uniform temperature distribution for sensitive materials.
-
Rotary Drum Furnaces:
- Used for sintering and heat treatment of bulk materials.
- Feature continuous operation for high-volume production.
-
Roller Hearth Kilns:
- Provide uniform heating for flat or sheet materials.
- Commonly used in ceramic and metal industries.
-
Pusher Slab Kilns:
- Designed for high-throughput heat treatment of large components.
- Suitable for heavy industrial applications.
-
Lift Bottom Kilns:
- Offer flexibility for batch processing.
- Ideal for small-scale or specialized heat treatment.
-
Drying Ovens:
-
Industrial Furnace Types:
-
Gas Furnaces:
- Use natural gas or propane for efficient and clean heat generation.
- Widely used in industries requiring consistent and high-temperature heat.
-
Electric Furnaces:
- Provide precise temperature control and are environmentally friendly.
- Suitable for applications requiring minimal contamination.
-
Oil Furnaces:
- Utilize oil as a fuel source for high-temperature processes.
- Common in industries with access to affordable oil resources.
-
Gas Furnaces:
By understanding these classifications, purchasers can select the most appropriate furnace for their specific heat treatment needs, ensuring optimal performance and cost-efficiency.
Summary Table:
Classification | Key Details |
---|---|
Temperature Range | - Low-Temperature (0–700°C): Tempering, annealing |
- General-Purpose (700–1050°C): Hardening, normalizing, carburizing | |
- High-Temperature (1000–1400°C): High-speed steel treatment | |
Heat Source | - Solid Fuels: Economical, large-scale |
- Liquid Fuels: Precise temperature control | |
- Gaseous Fuels: Clean, efficient | |
Design & Application | - Muffle Furnaces: Oxygen-free, high precision |
- Rotary Drum Furnaces: Bulk material sintering | |
- Roller Hearth Kilns: Uniform heating for flat materials | |
Industrial Types | - Gas Furnaces: Efficient, clean heat |
- Electric Furnaces: Precise, environmentally friendly | |
- Oil Furnaces: High-temperature processes |
Need help choosing the right heat treatment furnace? Contact our experts today for personalized guidance!