Ceramic tubes are versatile components widely used in industries and applications that demand materials capable of withstanding extreme conditions such as high temperatures, electrical currents, erosion, and impact. They are essential in furnace and kiln operations, temperature measurement, electrical insulation, and as protective or structural components in high-temperature environments. Their applications span across laboratory equipment, industrial processes, and specialized machinery, making them indispensable in fields like metallurgy, glass manufacturing, electronics, and healthcare. Ceramic tubes, particularly those made from alumina, are valued for their durability, thermal resistance, and electrical insulation properties.
Key Points Explained:
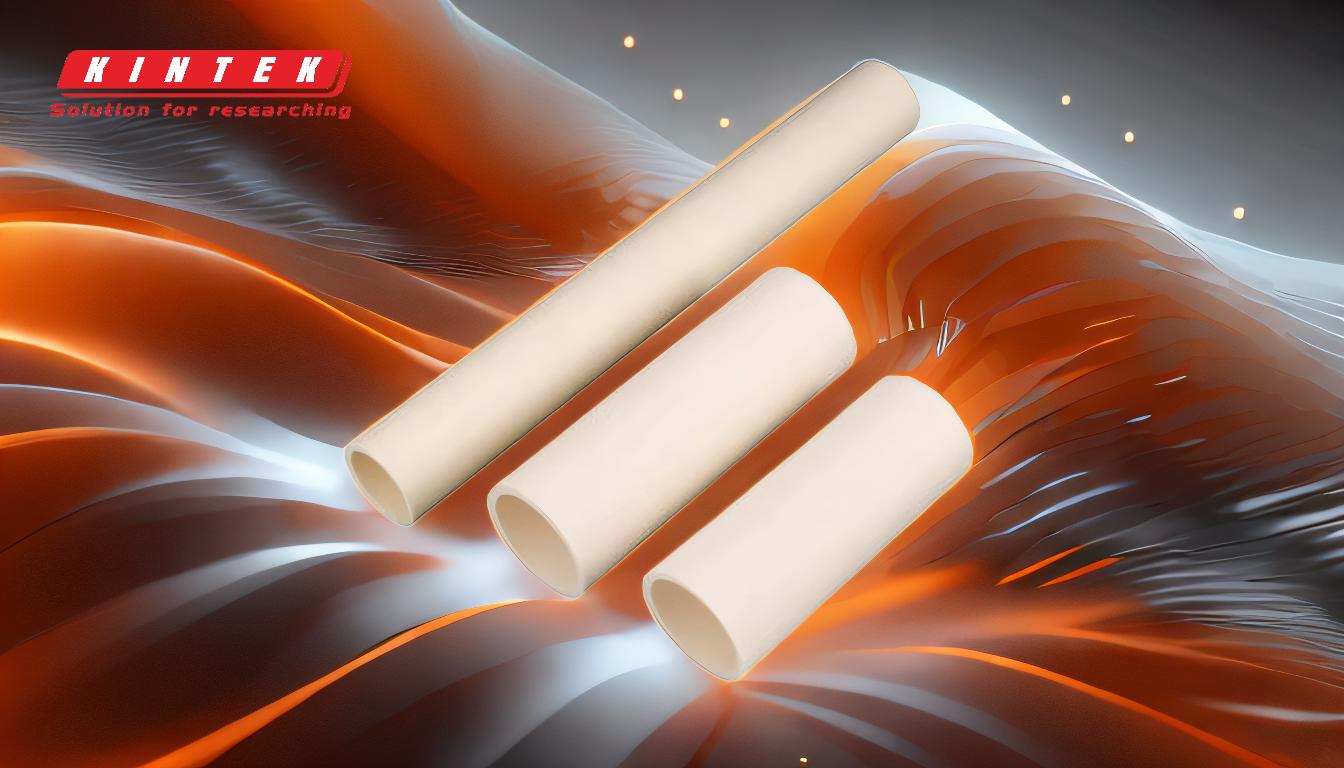
-
High-Temperature Applications:
- Ceramic tubes are extensively used in furnaces and kilns due to their ability to withstand extreme heat.
- They serve as furnace tubes in laboratory and industrial settings, providing structural support and insulation in high-temperature environments.
- Example: Alumina tubes are used in vacuum tube electric furnaces, muffle furnaces, and tin bath tubes for the float glass industry.
-
Electrical Insulation and Lead-Outs:
- Ceramic tubes are ideal for insulating electrical components and providing lead-outs for electrical cables in high-temperature systems.
- They are used in applications like thermocouples, igniter tubes, and high-power resistors, where electrical insulation is critical.
- Example: Ceramic tubes are used as protective tubes for thermocouples and as insulators in vacuum devices.
-
Temperature Measurement and Control:
- Ceramic tubes are employed in temperature measurement systems, such as thermocouple protection tubes, ensuring accurate readings in harsh environments.
- They are also used in thermostats and other temperature control devices.
- Example: Alumina tubes are used as protection tubes for solar glass and in thermocouple components.
-
Structural and Support Roles:
- Porous ceramic tubes are used to support wound heating elements in larger furnaces and kilns, ensuring even heat distribution and structural integrity.
- They are also used in turbine casting supports and wafer processing components.
- Example: Porous ceramic tubes support heating elements in industrial furnaces and kilns.
-
Specialized Industrial Applications:
- Ceramic tubes are used in niche industries, such as the aluminum trichloride industry, where they serve as chlorine tubes.
- They are also used in surgical devices, knife sharpeners, and other precision instruments.
- Example: Alumina tubes are used in surgical devices and as components in the aluminum trichloride industry.
-
Burner and Gas/Oil-Fired Kiln Applications:
- Ceramic tubes are used as burner holes in gas and oil-fired kilns, providing durability and resistance to high temperatures and corrosive environments.
- Example: Ceramic tubes are used in gas and oil-fired kilns for burner applications.
-
Vacuum and Atmosphere Furnaces:
- Ceramic tubes are used in vacuum and atmosphere furnaces, where their ability to withstand high temperatures and maintain structural integrity is critical.
- Example: Alumina tubes are used in vacuum atmosphere furnaces for high-temperature processes.
-
Durability and Resistance:
- Ceramic tubes are chosen for their resistance to erosion, impact, and chemical corrosion, making them suitable for demanding industrial environments.
- Example: Ceramic tubes are used in harsh environments like degassers and pump systems.
By understanding these key points, purchasers of equipment and consumables can make informed decisions about the appropriate use of ceramic tubes in their specific applications. Their versatility and resilience make them a valuable component in a wide range of industries.
Summary Table:
Application | Key Use | Example |
---|---|---|
High-Temperature Applications | Withstand extreme heat in furnaces and kilns | Alumina tubes in vacuum tube electric furnaces |
Electrical Insulation | Insulate electrical components and provide lead-outs | Protective tubes for thermocouples |
Temperature Measurement | Ensure accurate readings in harsh environments | Alumina tubes in thermocouple protection tubes |
Structural Support | Support heating elements and ensure structural integrity | Porous ceramic tubes in industrial furnaces |
Specialized Industrial Uses | Serve as chlorine tubes in niche industries | Alumina tubes in the aluminum trichloride industry |
Burner and Kiln Applications | Provide durability in gas and oil-fired kilns | Ceramic tubes in burner applications |
Vacuum and Atmosphere Furnaces | Maintain structural integrity in high-temperature processes | Alumina tubes in vacuum atmosphere furnaces |
Durability and Resistance | Resist erosion, impact, and chemical corrosion | Ceramic tubes in degassers and pump systems |
Looking for high-quality ceramic tubes for your industrial needs? Contact us today to find the perfect solution!