Vacuum furnaces are specialized equipment used across a wide range of industries for processes that require high-temperature treatments in a controlled, oxygen-free environment. They are essential for applications such as annealing, brazing, sintering, and heat treatment, where the absence of air prevents oxidation and contamination. Industries like aerospace, automotive, medical, and electronics rely on vacuum furnaces for producing high-strength, durable, and precise components. These furnaces are also critical in advanced manufacturing techniques like additive manufacturing and 3D printing, where controlled heat treatment is necessary for achieving desired material properties.
Key Points Explained:
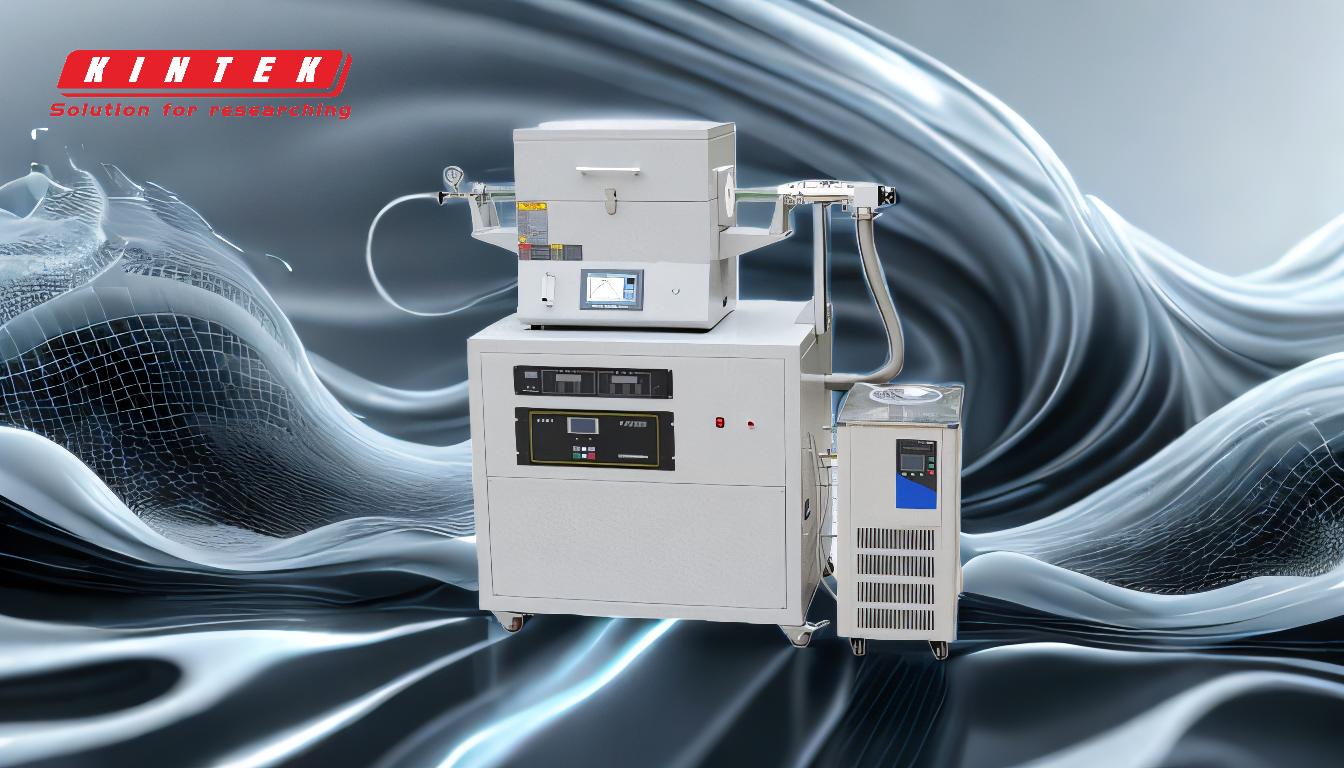
-
Protection from Oxidation and Contamination:
- Vacuum furnaces operate in an oxygen-free environment, which prevents oxidation and contamination of materials during high-temperature processes. This is crucial for maintaining the integrity and performance of metals and alloys.
- Applications: Annealing, brazing, sintering, and heat treatment of steel and metal parts.
-
Versatility Across Industries:
- Aerospace: Used for enhancing the strength and durability of components like turbine blades and engine parts.
- Automotive: Improves wear resistance and durability of transmission and engine components.
- Medical: Produces high-strength surgical instruments and medical implants.
- Electronics: Essential for processes like thin film deposition and crystal growth.
-
Advanced Manufacturing Techniques:
- Additive Manufacturing: Vacuum furnaces are used for proactive heat treatment in 3D printing and additive manufacturing, ensuring the desired material properties are achieved.
- Powdered Metal Parts: Used in metal injection molding and powdered metal parts manufacturing for creating complex geometries with high precision.
-
Specialized Processes:
- Vacuum Carburizing: A low-pressure carburizing process used to harden the surface of steel components without oxidation.
- Debinding: Removal of binders from molded parts before sintering.
- Purification and Sintering: Used in ceramics, silicon carbide, and hard alloy materials for high-temperature sintering and purification.
-
High-Temperature Material Processing:
- Vacuum furnaces are capable of processing materials at temperatures below 1,200 °C, making them suitable for a wide range of high-temperature applications.
- Industries: Electronics, energy, artificial gems, and advanced ceramics.
-
Vacuum Induction Furnaces:
- Used in vacuum metallurgy for melting alloys and special steels required in aerospace, missiles, rockets, and atomic energy equipment.
- Materials Produced: High-temperature alloys, stainless steel, heat-resistant steel, ultra-high-strength steel, tool steel, bearing steel, magnetic materials, elastic alloys, and expansion alloys.
-
Applications in Cutting-Edge Technologies:
- Body and Vehicle Armor: Used for ultra-high temperature sintering to produce durable armor materials.
- Advanced Ceramics: High-temperature firing of ceramics for industrial and technological applications.
Vacuum furnaces are indispensable in modern manufacturing and material processing, offering unparalleled control and consistency in high-temperature treatments. Their ability to operate in a contamination-free environment makes them ideal for producing high-performance components across a diverse range of industries. For more detailed information, you can explore the topic further at vacuum furnace.
Summary Table:
Application | Key Uses |
---|---|
Annealing | Prevents oxidation, enhances material strength |
Brazing | Joins metals without contamination |
Sintering | Produces high-strength components in additive manufacturing |
Heat Treatment | Improves durability and wear resistance of automotive and aerospace parts |
Vacuum Carburizing | Hardens steel surfaces without oxidation |
Debinding | Removes binders from molded parts before sintering |
Purification & Sintering | Used in ceramics, silicon carbide, and hard alloy materials |
Learn how vacuum furnaces can revolutionize your manufacturing process—contact us today!