Annealing steel is a heat treatment process used to soften the metal, improve its machinability, and relieve internal stresses. The process involves heating the steel to a specific temperature, holding it at that temperature for a set period, and then cooling it slowly. The choice of equipment and methods for annealing steel depends on the type of steel, the desired properties, and the scale of the operation. Common tools and equipment include furnaces, ovens, and controlled cooling environments. This guide will explore the key considerations and options for annealing steel effectively.
Key Points Explained:
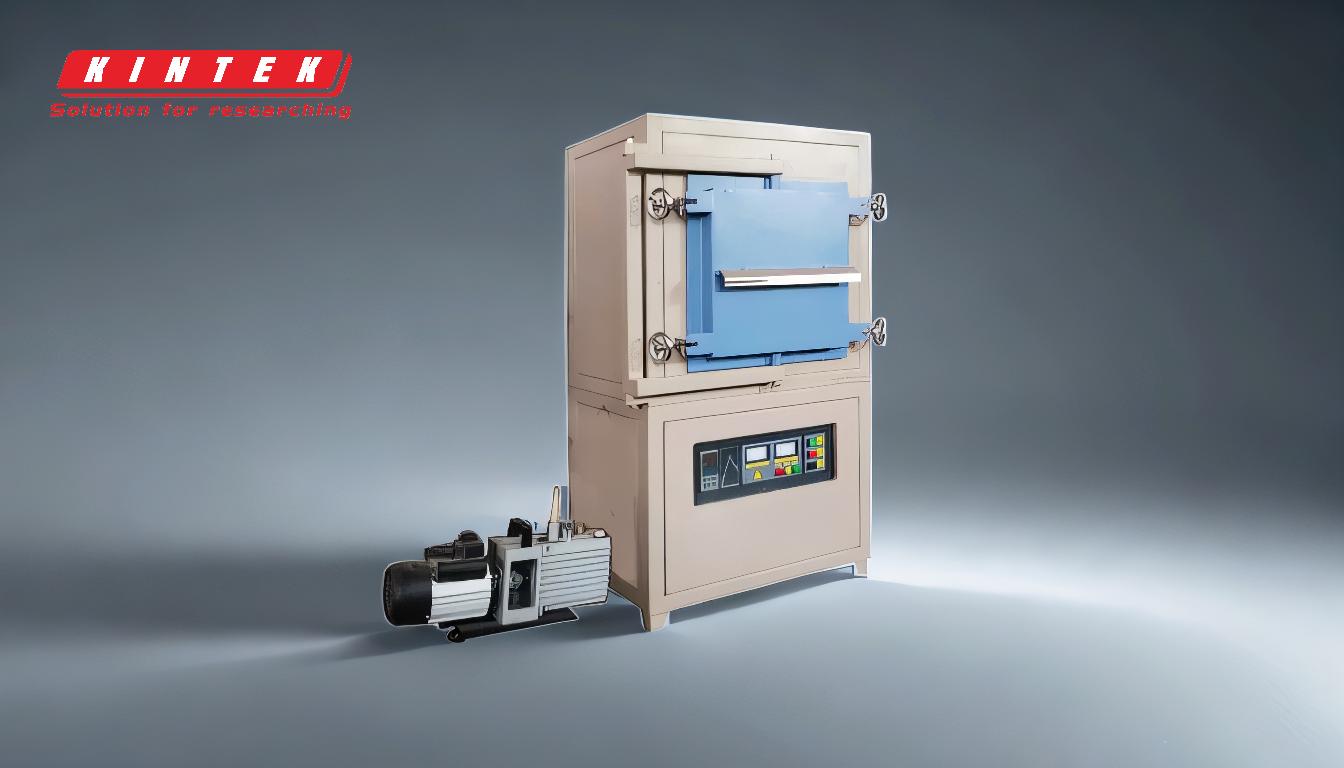
-
Understanding the Annealing Process
- Annealing involves three main stages: heating, soaking, and cooling.
- Heating: The steel is heated to a temperature above its recrystallization point but below its melting point. For most steels, this is typically between 700°C and 900°C.
- Soaking: The steel is held at the target temperature to ensure uniform heat distribution and to allow the microstructure to transform.
- Cooling: The steel is cooled slowly, often in the furnace or in an insulated container, to prevent the formation of hard, brittle structures.
- The goal is to achieve a soft, ductile material with improved workability and reduced internal stresses.
- Annealing involves three main stages: heating, soaking, and cooling.
-
Choosing the Right Equipment
-
Furnaces:
- Electric or gas-fired furnaces are commonly used for annealing steel. They provide precise temperature control and uniform heating.
- For small-scale operations, a muffle furnace is ideal because it isolates the steel from direct contact with flames, reducing the risk of contamination.
-
Ovens:
- Industrial ovens are suitable for larger pieces of steel or batch processing. They offer consistent heat distribution and can handle higher volumes.
-
Induction Heaters:
- Induction heating is used for localized annealing. It heats the steel quickly and efficiently but requires specialized equipment.
-
Salt Baths:
- Salt baths provide rapid and uniform heating, making them suitable for small parts or specific applications. However, they require careful handling due to the corrosive nature of molten salts.
-
Furnaces:
-
Cooling Methods
-
Furnace Cooling:
- The steel is cooled inside the furnace by gradually reducing the temperature. This method is ideal for achieving a soft, stress-free structure.
-
Air Cooling:
- The steel is removed from the furnace and allowed to cool in still air. This method is slower than quenching but faster than furnace cooling.
-
Insulated Containers:
- The steel is placed in an insulated container (e.g., a box filled with vermiculite or sand) to slow down the cooling process.
-
Furnace Cooling:
-
Material Considerations
-
Type of Steel:
- Different steels require different annealing temperatures and cooling rates. For example, low-carbon steels are annealed at lower temperatures than high-carbon steels.
-
Size and Shape:
- Thicker or irregularly shaped pieces may require longer soaking times to ensure uniform heating.
-
Surface Finish:
- To prevent oxidation or scaling, the steel can be annealed in a controlled atmosphere (e.g., inert gas or vacuum) or coated with a protective layer.
-
Type of Steel:
-
Safety and Best Practices
- Always wear appropriate protective gear, such as heat-resistant gloves and goggles, when handling hot steel or operating annealing equipment.
- Ensure proper ventilation when using furnaces or ovens to avoid exposure to harmful fumes.
- Regularly calibrate and maintain equipment to ensure accurate temperature control and consistent results.
- Follow manufacturer guidelines for the specific type of steel and equipment being used.
By carefully selecting the right equipment and following the proper annealing process, you can achieve the desired material properties for your steel. Whether you're working on a small project or an industrial-scale operation, understanding the fundamentals of annealing will help you produce high-quality results.
Summary Table:
Equipment/Method | Key Features | Best Use Cases |
---|---|---|
Electric/Gas Furnaces | Precise temperature control, uniform heating | Small to medium-scale operations |
Muffle Furnaces | Isolates steel from flames, reduces contamination | Small-scale, precision annealing |
Industrial Ovens | Consistent heat distribution, handles large volumes | Large-scale or batch processing |
Induction Heaters | Rapid, localized heating | Small parts or specific applications |
Salt Baths | Rapid and uniform heating | Small parts, requires careful handling |
Furnace Cooling | Gradual cooling for soft, stress-free structure | General-purpose annealing |
Air Cooling | Slower than quenching, faster than furnace cooling | Moderate cooling needs |
Insulated Containers | Slows cooling process, ideal for specific applications | Custom cooling requirements |
Ready to optimize your annealing process? Contact our experts today for tailored solutions!