PVD (Physical Vapor Deposition) coatings are known for their versatility in color options, offering a wide range of metallic and non-metallic shades. These coatings can achieve colors such as gold, rose gold, silver, black, bronze, blue, purple, and more, depending on the materials and processes used. The exact color is influenced by the type of metal vaporized (target) and the reactive gases employed during the deposition process. Additionally, PVD coatings can be applied to various substrates, including metals and plastics, ensuring uniform color matching. This makes PVD coatings highly customizable and suitable for applications requiring both aesthetic appeal and functional properties like durability and corrosion resistance.
Key Points Explained:
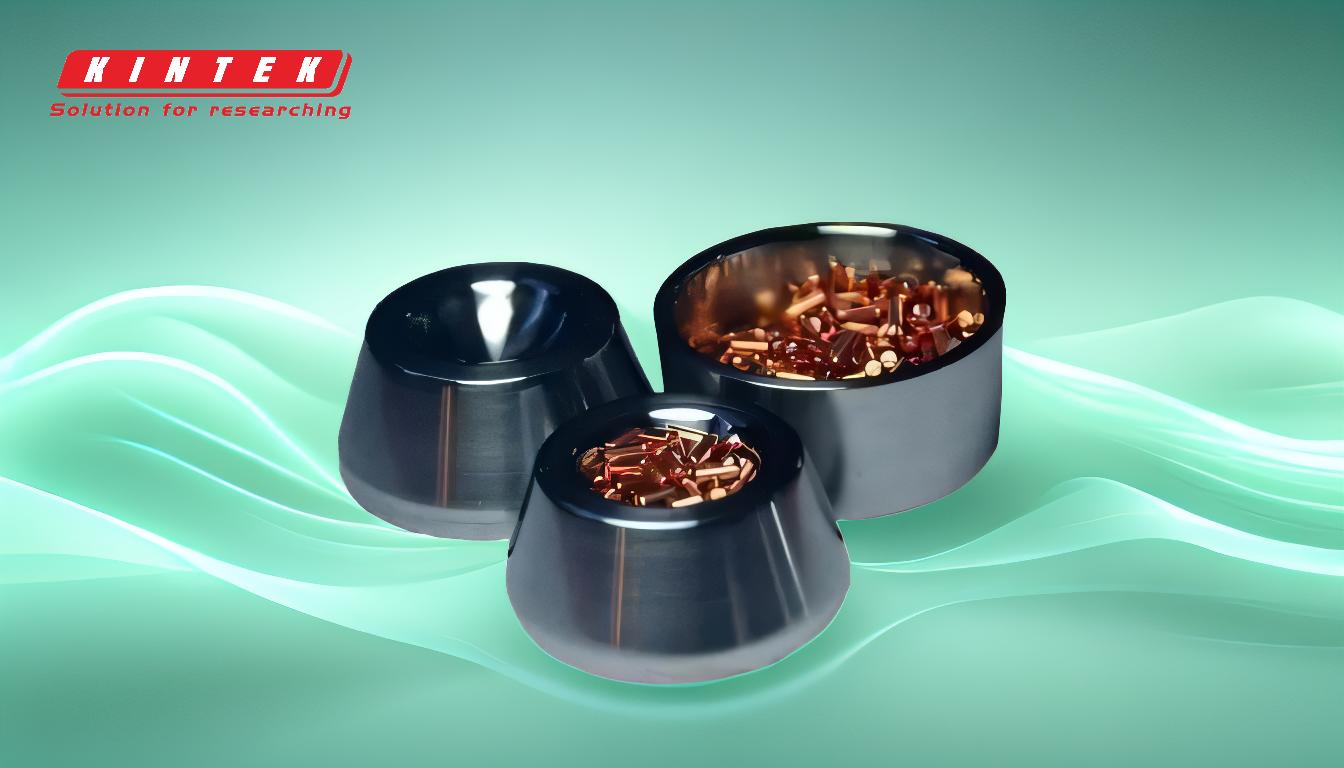
-
Wide Range of Colors Available:
- PVD coatings can achieve a diverse spectrum of colors, including metallic tones like gold, rose gold, silver, and bronze, as well as non-metallic colors such as black, blue, green, and red.
- Examples of specific colors include 24K gold, dark brass, gunmetal, purple, turquoise, and mixed multicolor.
- This versatility allows for customization to meet specific design or functional requirements.
-
Factors Influencing PVD Coating Colors:
- The color of a PVD coating is determined by the type of metal vaporized (target) and the reactive gases used during the deposition process.
- For instance, brass tones, gold tones, and black to grey shades are produced by varying the target material and gas mixture.
- The deposition conditions, such as temperature and pressure, also play a role in achieving the desired color.
-
Substrate Compatibility and Color Uniformity:
- PVD coatings can be applied to a variety of substrates, including metals (e.g., stainless steel, copper, zinc alloy) and plastics.
- The process ensures uniform color across different materials, making it ideal for applications where consistent appearance is critical.
- In some cases, achieving precise color matching may require combining a PVD layer with a colored protective layer.
-
Aesthetic and Functional Benefits:
- PVD coatings not only provide aesthetic appeal but also enhance the functional properties of the substrate.
- These coatings are known for their hardness, corrosion resistance, abrasion resistance, and durability, often eliminating the need for additional protective topcoats.
- The reflective surface of PVD coatings can achieve a metallic luster without the need for polishing.
-
Finishes and Applications:
- PVD coatings are available in various finishes, including polished, satin, and matt, further expanding their aesthetic possibilities.
- They are widely used in industries such as automotive, jewelry, electronics, and architecture, where both appearance and performance are important.
-
Limitations and Considerations:
- PVD coatings have relatively low deposition temperatures and high cleaning requirements.
- The film thickness is typically around 2.5 μm, which is sufficient for most applications.
- However, PVD technologies may exhibit poor coating performance on the back and sides of tools due to low air pressure, which can limit their use in certain scenarios.
In summary, PVD coatings offer a wide range of colors and finishes, making them highly customizable for both aesthetic and functional applications. The color is influenced by the materials and processes used, and the coatings can be applied to various substrates with excellent uniformity. While there are some limitations, PVD coatings remain a popular choice for industries requiring durable, corrosion-resistant, and visually appealing surfaces.
Summary Table:
Aspect | Details |
---|---|
Available Colors | Gold, rose gold, silver, black, bronze, blue, purple, green, red, and more. |
Influencing Factors | Target metal, reactive gases, temperature, and pressure. |
Substrate Compatibility | Metals (stainless steel, copper, zinc alloy) and plastics. |
Functional Benefits | Durability, corrosion resistance, abrasion resistance, and metallic luster. |
Applications | Automotive, jewelry, electronics, architecture. |
Unlock the potential of PVD coatings for your projects—contact us today to learn more!