An annealing furnace is a specialized piece of equipment used to heat materials, typically metals, above their recrystallization temperature to alter their physical properties. This process makes the material more ductile, reduces internal stresses, and improves its workability. The furnace achieves this by heating the material to a specific temperature, holding it there for a set period, and then cooling it in a controlled manner. A vacuum annealing furnace operates under a vacuum environment, which prevents oxidation and contamination, making it ideal for high-precision applications like stainless steel components, bearings, and cutting tools.
Key Points Explained:
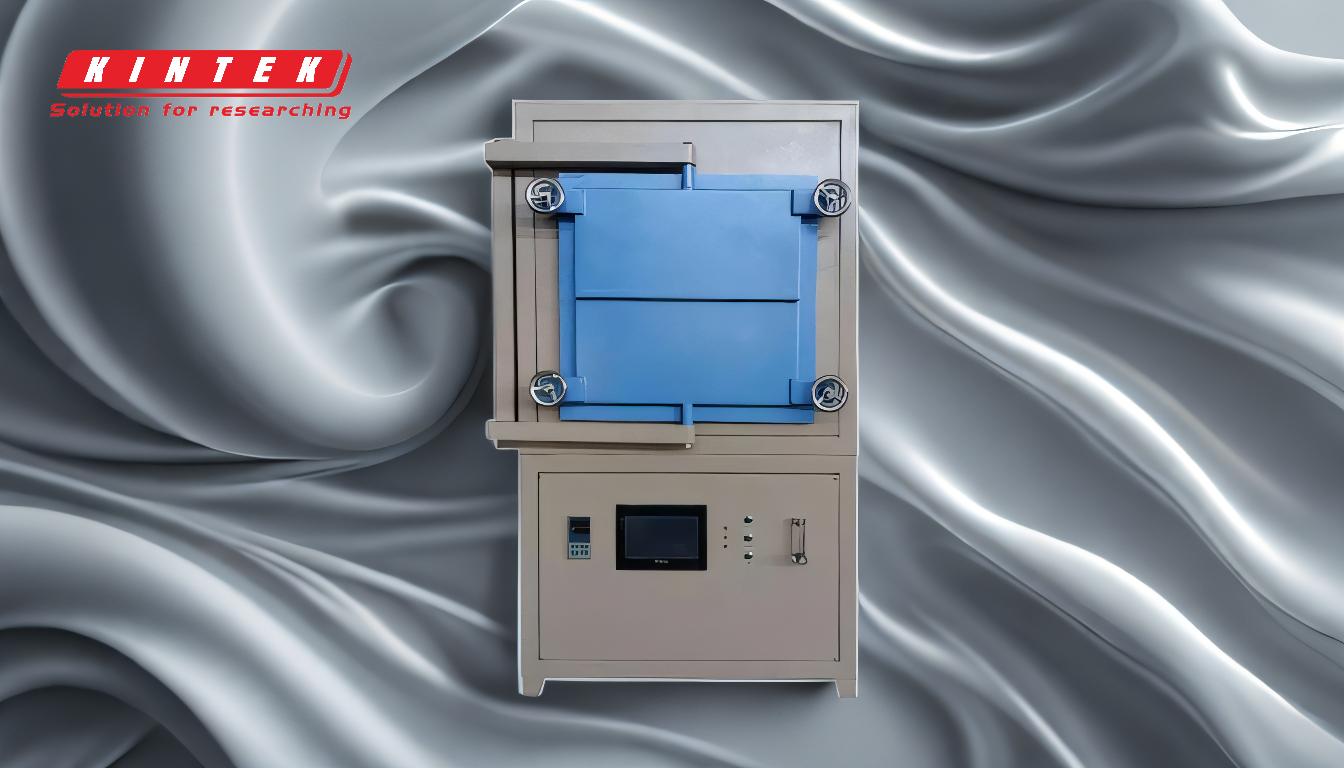
-
Purpose of an Annealing Furnace:
- An annealing furnace is designed to heat materials, particularly metals, above their recrystallization temperature. This process softens the material, making it more ductile and easier to work with. It also relieves internal stresses and improves the material's overall mechanical properties, such as strength and hardness.
-
How an Annealing Furnace Works:
- The furnace heats the material to a temperature above its recrystallization point, holds it at that temperature for a specific duration, and then cools it down in a controlled manner. This controlled cooling is crucial to achieve the desired material properties.
-
Applications of Annealing Furnaces:
- Annealing furnaces are widely used in industries that require metalworking, such as automotive, aerospace, and manufacturing. They are essential for processes like welding, melting, and quenching, where altering the material's properties is necessary.
-
Advantages of a Vacuum Annealing Furnace:
- A vacuum annealing furnace operates in a vacuum environment, which prevents oxidation and contamination. This is particularly important for high-precision applications where material purity is critical. The vacuum environment ensures that the material remains uncontaminated, resulting in higher quality and more reliable components.
-
Specific Uses of Vacuum Annealing Furnaces:
- These furnaces are commonly used for stainless steel deep-drawing parts, such as plumbing equipment, to prevent oxidation. They are also used in the production of stainless steel bearings, cutting tools, self-tapping screws, and stainless steel dowels. The ability to operate in a protective atmosphere makes them suitable for high-precision metal components.
-
Cooling Mechanism in Vacuum Furnaces:
- After the heating process, inert gas is used to cool the metal quickly. The gas is pressurized and circulated to absorb heat, which is then removed through a heat exchanger. This rapid cooling helps in achieving the desired material properties efficiently.
-
Material Handling in Annealing Furnaces:
- The material is typically placed in a basket, which is then moved into the furnace using a crane. The basket is hoisted into the furnace for heating, and after the process is complete, it is removed and cooled. This method ensures that the material is handled safely and efficiently.
In summary, an annealing furnace, especially a vacuum annealing furnace, plays a crucial role in altering the physical properties of materials to make them more suitable for various industrial applications. The vacuum environment ensures high-quality results by preventing contamination and oxidation, making it indispensable for high-precision manufacturing processes.
Summary Table:
Aspect | Details |
---|---|
Purpose | Heats metals above recrystallization temperature to improve ductility. |
How It Works | Heats, holds, and cools materials in a controlled manner. |
Applications | Used in automotive, aerospace, and manufacturing industries. |
Vacuum Furnace Benefits | Prevents oxidation and contamination, ideal for high-precision components. |
Cooling Mechanism | Uses inert gas for rapid, controlled cooling. |
Material Handling | Materials are placed in baskets and moved using cranes for efficiency. |
Learn how an annealing furnace can optimize your processes—contact our experts today!