Braze welding bond strength depends on several critical factors, including the compatibility of the base metals and filler material, surface preparation, joint design, and the thermal conditions during the welding process. The strength of the bond is influenced by the metallurgical interaction between the filler material and the base metals, which must form a strong, durable joint. Surface cleanliness and proper wetting of the filler material are essential for achieving a strong bond. Additionally, the joint design must allow for adequate filler material distribution, and the thermal conditions must ensure proper melting and solidification of the filler material without causing thermal stress or distortion in the base metals.
Key Points Explained:
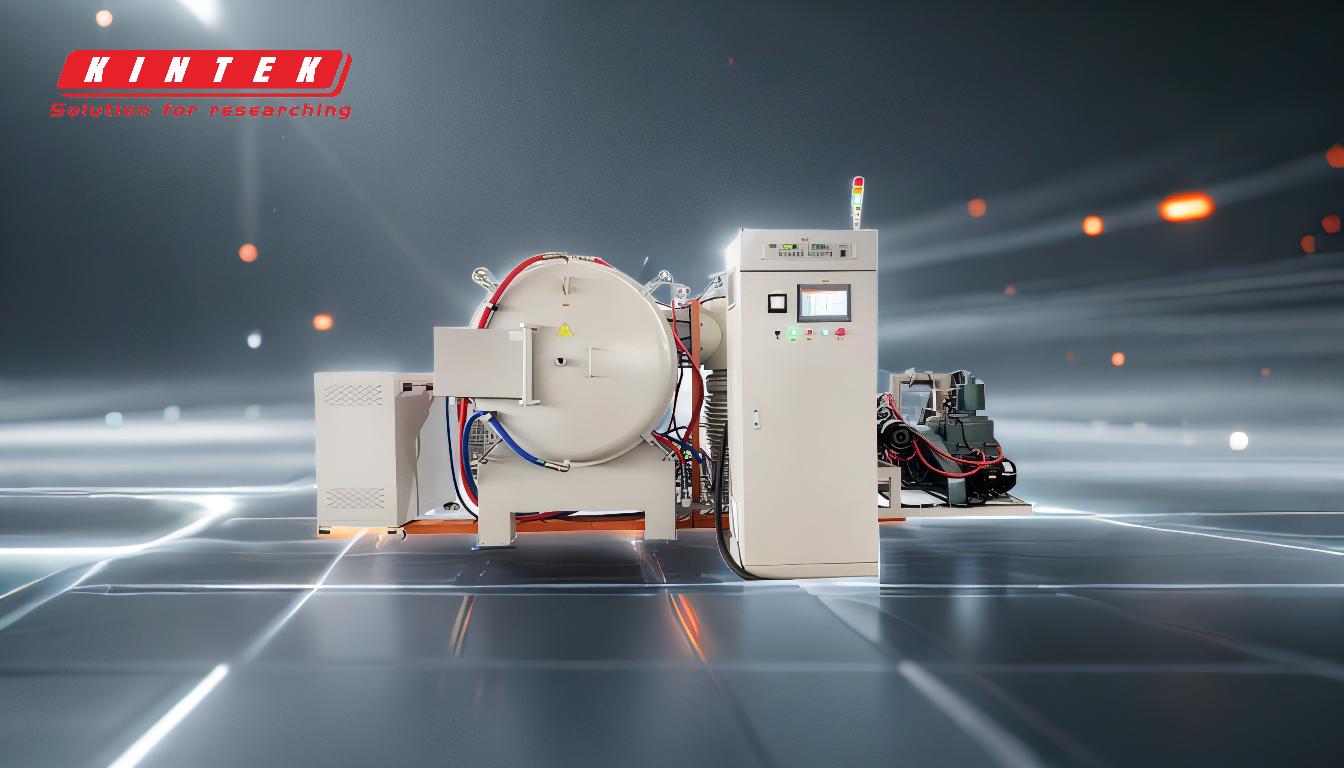
-
Compatibility of Base Metals and Filler Material:
- The bond strength in braze welding heavily relies on the metallurgical compatibility between the base metals and the filler material. The filler material must have a lower melting point than the base metals to ensure it melts and flows into the joint without melting the base metals.
- The filler material should form a strong metallurgical bond with the base metals, often through processes like diffusion or alloying. For example, using a copper-based filler for steel or a silver-based filler for stainless steel ensures good compatibility and bond strength.
-
Surface Preparation:
- Surface cleanliness is crucial for achieving a strong bond. Contaminants such as oil, grease, oxides, or dirt can prevent proper wetting of the filler material, leading to weak or incomplete bonds.
- Surface preparation techniques like cleaning, degreasing, and abrasive blasting are often used to ensure the surfaces are free from contaminants. In some cases, chemical fluxes are applied to remove oxides and promote wetting.
-
Joint Design:
- The design of the joint plays a significant role in determining bond strength. The joint must provide sufficient surface area for the filler material to adhere to and distribute evenly.
- Common joint designs for braze welding include lap joints, butt joints, and T-joints. The joint clearance (gap between the base metals) is critical; too wide or too narrow a gap can lead to poor filler material distribution and weak bonds.
-
Thermal Conditions:
- Proper control of the heating and cooling process is essential for achieving a strong bond. The filler material must be heated to its melting point and allowed to flow into the joint, but excessive heat can damage the base metals or cause distortion.
- The cooling rate must also be controlled to prevent thermal stress or cracking in the joint. Uniform heating and cooling are often achieved using controlled heating methods like induction heating or furnace brazing.
-
Wetting and Capillary Action:
- Wetting refers to the ability of the molten filler material to spread and adhere to the base metals. Good wetting is essential for forming a strong bond.
- Capillary action helps draw the molten filler material into the joint, ensuring complete filling and strong adhesion. The joint design and surface preparation must facilitate capillary action for optimal bond strength.
-
Use of Fluxes and Atmospheres:
- Fluxes are often used in braze welding to remove oxides and improve wetting. They also protect the joint from oxidation during the heating process.
- In some cases, controlled atmospheres (e.g., inert gases or vacuum) are used to prevent oxidation and contamination, further enhancing bond strength.
By carefully considering these factors, a strong and durable bond can be achieved in braze welding, ensuring the integrity and performance of the welded joint.
Summary Table:
Factor | Key Considerations |
---|---|
Compatibility | Metallurgical interaction between base metals and filler material. |
Surface Preparation | Cleanliness, degreasing, and use of fluxes to ensure proper wetting. |
Joint Design | Adequate surface area and clearance for filler material distribution. |
Thermal Conditions | Controlled heating and cooling to prevent distortion or thermal stress. |
Wetting & Capillary Action | Molten filler material must spread and fill the joint effectively. |
Fluxes & Atmospheres | Use of fluxes or controlled atmospheres to prevent oxidation and enhance bond strength. |
Need expert advice on achieving optimal bond strength in braze welding? Contact us today for tailored solutions!