Hot isostatic pressing (HIP) is a manufacturing process that uses high temperature and pressure to improve the properties of materials, particularly metals and ceramics. By applying uniform pressure from all directions using inert gas, HIP enhances material density, eliminates porosity, and improves mechanical properties such as strength, ductility, and fatigue resistance. It is widely used in industries like aerospace, automotive, and medical devices to produce high-performance components. HIP is also effective for bonding materials, relieving thermal stresses, and optimizing additive manufacturing parts by addressing issues like porosity and poor layer adhesion.
Key Points Explained:
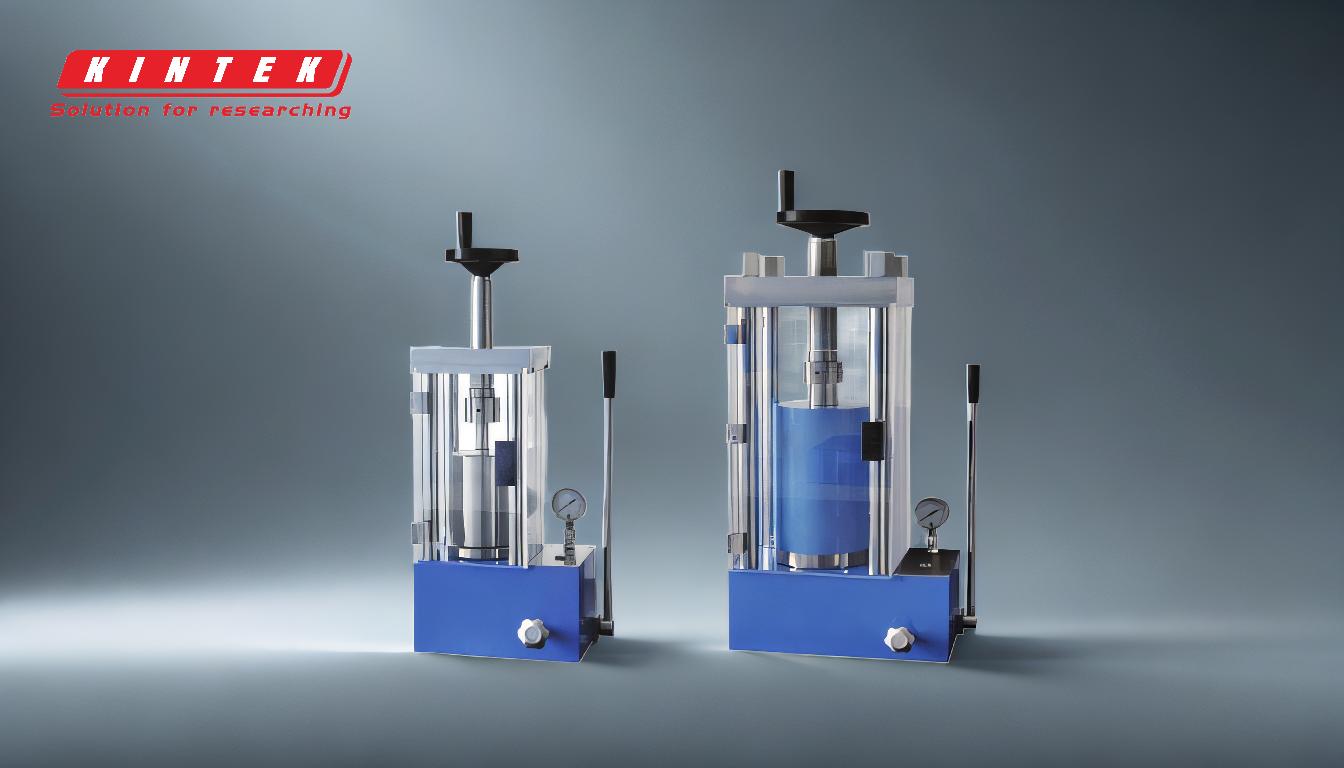
-
Process Overview:
- Hot isostatic pressing involves placing materials (powder or solid) in a high-pressure chamber filled with inert gas, typically argon.
- The chamber is heated to high temperatures (e.g., 1000°C) and pressurized (e.g., 100MPa) to achieve uniform densification and bonding.
- The process is controlled to ensure precise temperature, pressure, and timing, followed by a cool-down phase for safe removal of parts.
-
Key Benefits:
- Improved Density: HIP produces materials with nearly 100% theoretical density, eliminating voids and porosity.
- Enhanced Mechanical Properties: It improves ductility, fatigue resistance, wear resistance, and corrosion resistance.
- Stress Relief: HIP relieves internal stresses in cast, sintered, and additively manufactured parts, ensuring structural integrity.
- Consolidation of Manufacturing Steps: HIP combines heat treatment, quenching, and aging processes, reducing production time and costs.
-
Applications:
- Additive Manufacturing: HIP addresses porosity and layer adhesion issues in 3D-printed parts, creating a uniform microstructure.
- Material Bonding: It enables the cladding or bonding of dissimilar materials, either in powder or solid form.
- High-Performance Industries: HIP is used in aerospace, automotive, and medical industries to produce components with superior mechanical properties.
-
Comparison with Other Methods:
- Wet-Bag Isostatic Pressing: Unlike HIP, wet-bag pressing uses liquid as the pressurizing medium and is typically performed at lower temperatures. It is suitable for simpler shapes and lower-density products.
- Warm Isostatic Press: This process operates at lower temperatures than HIP and uses a heated liquid medium. It is ideal for materials that require moderate temperature and pressure for densification.
-
Material Property Enhancement:
- HIP significantly increases fatigue life (by 10 to 100 times) and improves wear and corrosion resistance.
- It ensures uniform material properties throughout the component, making it ideal for critical applications.
-
Process Control:
- The temperature, pressure, and duration of the HIP process are carefully monitored to achieve optimal results.
- Advanced systems, like those in a warm isostatic press, use precise temperature control and booster sources to maintain consistent conditions.
By leveraging the principles of uniform pressure and high temperature, HIP transforms materials into high-performance components, making it a cornerstone of modern manufacturing.
Summary Table:
Aspect | Details |
---|---|
Process Overview | Uses high temperature and pressure with inert gas for uniform densification. |
Key Benefits | Improves density, mechanical properties, stress relief, and production efficiency. |
Applications | Additive manufacturing, material bonding, aerospace, automotive, and medical industries. |
Comparison with Others | Wet-bag pressing uses liquid; warm isostatic press operates at lower temperatures. |
Material Enhancement | Increases fatigue life, wear resistance, and corrosion resistance. |
Process Control | Precise temperature, pressure, and timing for optimal results. |
Learn how HIP can revolutionize your manufacturing process—contact our experts today!