The deposition rate is a critical parameter in thin film deposition processes, as it directly influences the quality, properties, and performance of the deposited material. It indicates how quickly a material is deposited onto a substrate and is affected by various factors such as gas flow, pressure, temperature, and the choice of target material. Understanding the deposition rate helps in optimizing the process to achieve desired film properties, such as chemical composition, microstructure, and optical characteristics. This is particularly important in industries like semiconductors, where precise control over film properties is essential for high-performance applications.
Key Points Explained:
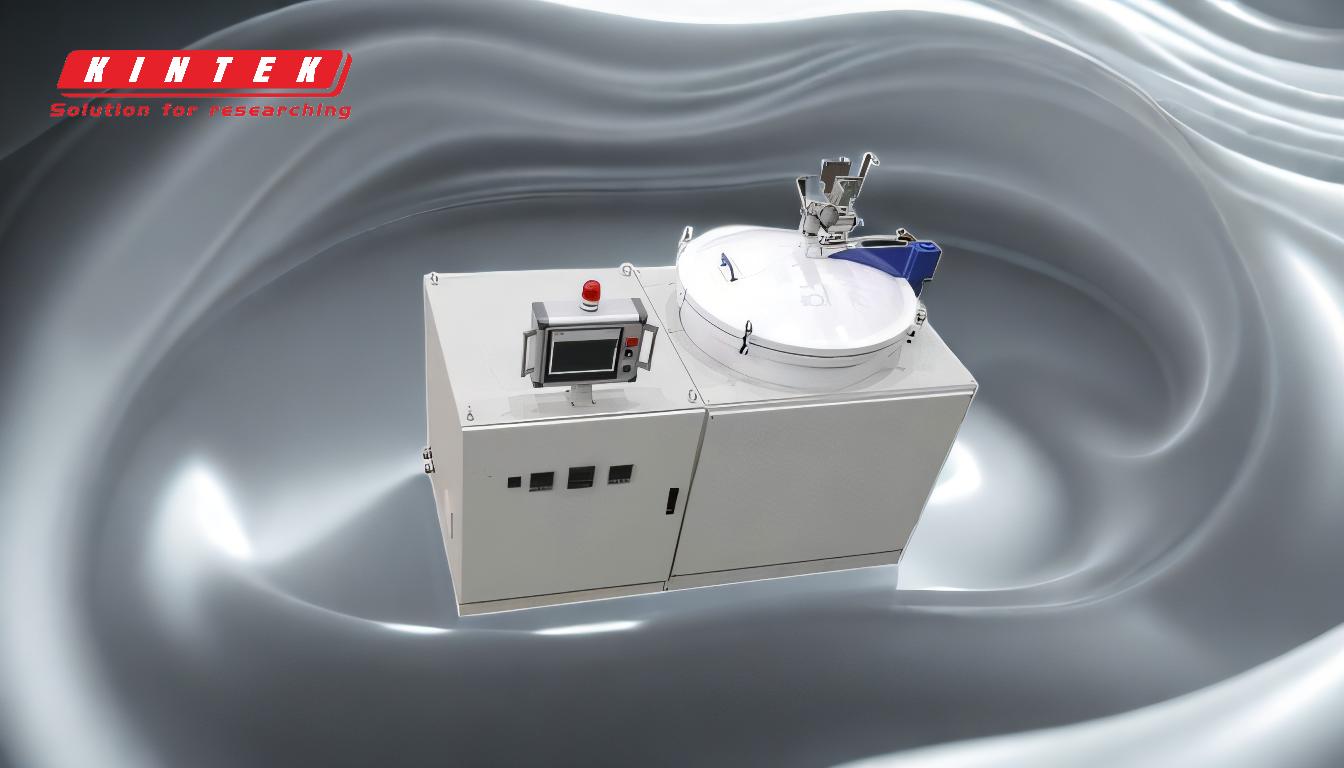
-
Definition of Deposition Rate:
- The deposition rate refers to the speed at which a material is deposited onto a substrate during a thin film deposition process. It is typically measured in units of thickness per unit time (e.g., nanometers per second).
- This rate is a key indicator of the efficiency and effectiveness of the deposition process, as it directly impacts the uniformity, thickness, and quality of the thin film.
-
Factors Influencing Deposition Rate:
- Gas Flow: For example, in the deposition of SiNx films, increasing the flow of SiH4 (silane) increases the deposition rate, while increasing NH3 (ammonia) flow decreases it. This is because the chemical reactions governing the deposition process are influenced by the availability of reactants.
- Pressure: Higher pressure generally increases the deposition rate by increasing the number of reactive species available for deposition. However, this can also lead to changes in film properties, such as density and stress.
- Temperature: Substrate temperature plays a significant role in determining the deposition rate. Higher temperatures can enhance the mobility of atoms on the substrate surface, leading to better film quality but potentially reducing the deposition rate due to increased desorption of deposited species.
- Target Material: The choice of target material affects the deposition rate by influencing the sputtering yield and the energy distribution of the sputtered particles. Different materials have different sputtering efficiencies, which can be adjusted by modifying the sputtering system and anode configuration.
-
Impact on Film Properties:
- Chemical Composition: The deposition rate can influence the stoichiometry of the deposited film. For example, in SiNx films, the ratio of Si to N can vary depending on the deposition conditions, affecting the film's chemical and physical properties.
- Microstructure: A higher deposition rate can lead to a more amorphous or less crystalline structure, while a lower rate may favor the formation of a more ordered crystalline structure.
- Optical Properties: The deposition rate is closely related to the optical properties of the film, such as the refractive index and extinction coefficient. For instance, in SiNx films, the refractive index tends to increase with the deposition rate when influenced by gas flow, but it may decrease with temperature and pressure.
-
Importance in Semiconductor Industry:
- In the semiconductor industry, precise control over the deposition rate is crucial for producing high-quality, high-performance thin films. These films are used in various applications, including transistors, capacitors, and interconnects, where uniformity, thickness, and material properties are critical.
- The ability to adjust the deposition rate allows for the optimization of film properties to meet specific performance requirements, such as electrical conductivity, thermal stability, and mechanical strength.
-
Practical Implications for Equipment and Consumable Purchasers:
- Equipment Selection: When selecting deposition equipment, purchasers should consider systems that offer precise control over deposition parameters, such as gas flow, pressure, and temperature, to achieve the desired deposition rate and film properties.
- Consumables: The choice of target materials and gases should be based on their impact on the deposition rate and the resulting film properties. For example, selecting a target material with a high sputtering yield can increase the deposition rate, while choosing gases that optimize the chemical reactions can improve film quality.
- Process Optimization: Understanding the relationship between deposition rate and film properties allows purchasers to optimize the deposition process for specific applications, ensuring that the final product meets the required specifications.
In summary, the deposition rate is a fundamental parameter in thin film deposition processes, influencing the quality, properties, and performance of the deposited material. By understanding and controlling the factors that affect the deposition rate, manufacturers can optimize their processes to produce high-quality thin films for a wide range of applications, particularly in the semiconductor industry.
Summary Table:
Aspect | Details |
---|---|
Definition | Speed of material deposition onto a substrate (e.g., nm/s). |
Key Influencing Factors | Gas flow, pressure, temperature, and target material. |
Impact on Film Properties | Chemical composition, microstructure, and optical properties. |
Industry Importance | Critical in semiconductors for high-performance applications. |
Practical Implications | Equipment and consumable selection, process optimization. |
Want to optimize your thin film deposition process? Contact our experts today for tailored solutions!