Inert gases play a crucial role in various industrial processes by providing a non-reactive environment that prevents unwanted chemical reactions, oxidation, or contamination. Their primary function is to maintain the integrity of materials and processes by ensuring that no chemical interactions occur. In processes like sputtering, debinding, Hot Isostatic Pressing (HIP), and vacuum furnaces, inert gases such as argon and nitrogen are used to create a controlled atmosphere. This ensures that materials remain pure, defects are minimized, and processes like cooling or pressure application are carried out effectively. The use of inert gases is essential for achieving consistent, high-quality results in manufacturing and material processing.
Key Points Explained:
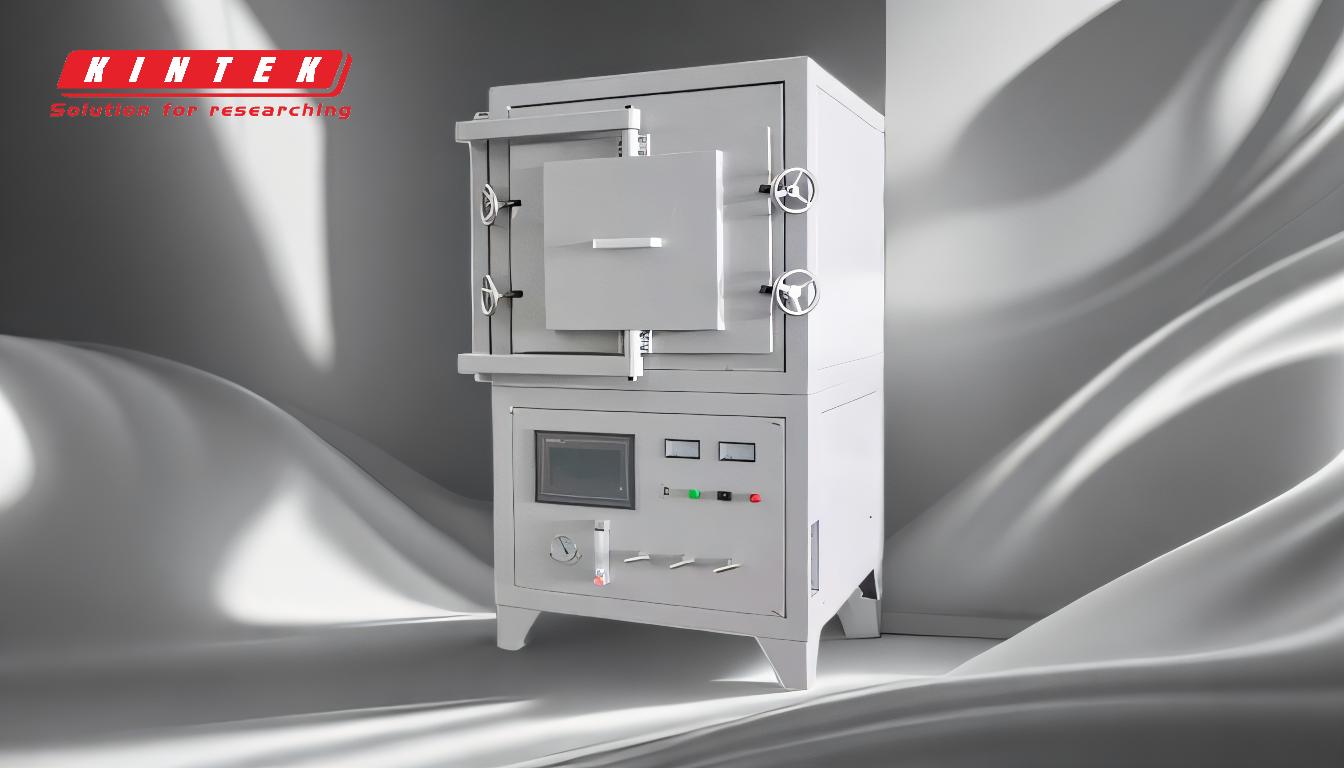
-
Prevention of Chemical Reactions:
- Inert gases, such as argon and nitrogen, are chemically non-reactive. This property is critical in processes like sputtering and HIP, where the goal is to avoid any chemical interaction with the target material or the sample.
- For example, in sputtering, inert gases ensure that the deposition process remains purely physical, preventing contamination or unwanted chemical reactions that could alter the material's properties.
-
Protection Against Oxidation and Contamination:
- In processes like debinding and muffle furnace operations, inert gases act as protective atmospheres. They prevent oxidation or reduction reactions on metal surfaces, especially at high temperatures.
- For instance, nitrogen is used for stainless steels, while argon is preferred for titanium alloys during debinding. This ensures the material's surface remains unchanged, preserving its integrity.
-
Uniform Pressure Application in HIP:
- In Hot Isostatic Pressing (HIP), inert gases like argon are used to apply uniform isostatic pressure in all directions. This uniform pressure is essential for making the material plastic, allowing voids to collapse and bond together.
- The inert gas ensures that no chemical reactions occur during the application of heat and pressure, maintaining the material's properties and improving its density and strength.
-
Cooling in Vacuum Furnaces:
- Inert gases are used in vacuum furnaces to rapidly cool treated metals after processing. The gas is pressurized and circulated through the hot zone to absorb heat, then passed through a heat exchanger to remove the heat.
- This controlled cooling process prevents metallurgical changes and ensures the material reaches the desired temperature without compromising its properties.
-
Fire and Explosion Prevention:
- In the chemical industry, inert gases are used to create non-reactive atmospheres for conducting reactions. They minimize fire hazards and prevent unwanted reactions.
- Additionally, inert gases are used to purge transfer lines and vessels, reducing the risk of explosions or fires by displacing reactive gases like oxygen.
-
Material Purity and Test Accuracy:
- In muffle furnaces and other high-temperature processes, inert gases protect special materials from reacting with air. This ensures that the material remains pure and that test results are accurate.
- For example, inert gases prevent oxidation or other chemical changes that could alter the material's composition or properties during testing.
By understanding these key points, it becomes clear that inert gases are indispensable in maintaining process control, material integrity, and safety across a wide range of industrial applications. Their ability to create a non-reactive environment ensures that processes are carried out efficiently and that the final products meet the required quality standards.
Summary Table:
Key Role of Inert Gases | Applications |
---|---|
Prevention of Chemical Reactions | Sputtering, Hot Isostatic Pressing (HIP) |
Protection Against Oxidation | Debinding, muffle furnace operations |
Uniform Pressure Application | Hot Isostatic Pressing (HIP) |
Cooling in Vacuum Furnaces | Rapid cooling of treated metals |
Fire and Explosion Prevention | Chemical industry reactions, purging transfer lines and vessels |
Material Purity and Test Accuracy | Muffle furnaces, high-temperature processes |
Learn how inert gases can optimize your industrial processes—contact our experts today!