Chemical vapor deposition (CVD) is a versatile and widely used technique for depositing high-quality thin films and coatings. The process involves the reaction of gaseous precursors on a substrate surface, leading to the formation of a solid material. CVD is particularly valued for its ability to produce films with high purity, fine-grained structures, and excellent uniformity, making it suitable for applications in semiconductors, optoelectronics, and other advanced industries. The equipment required for CVD is specialized and must be carefully selected to ensure optimal performance and results.
Key Points Explained:
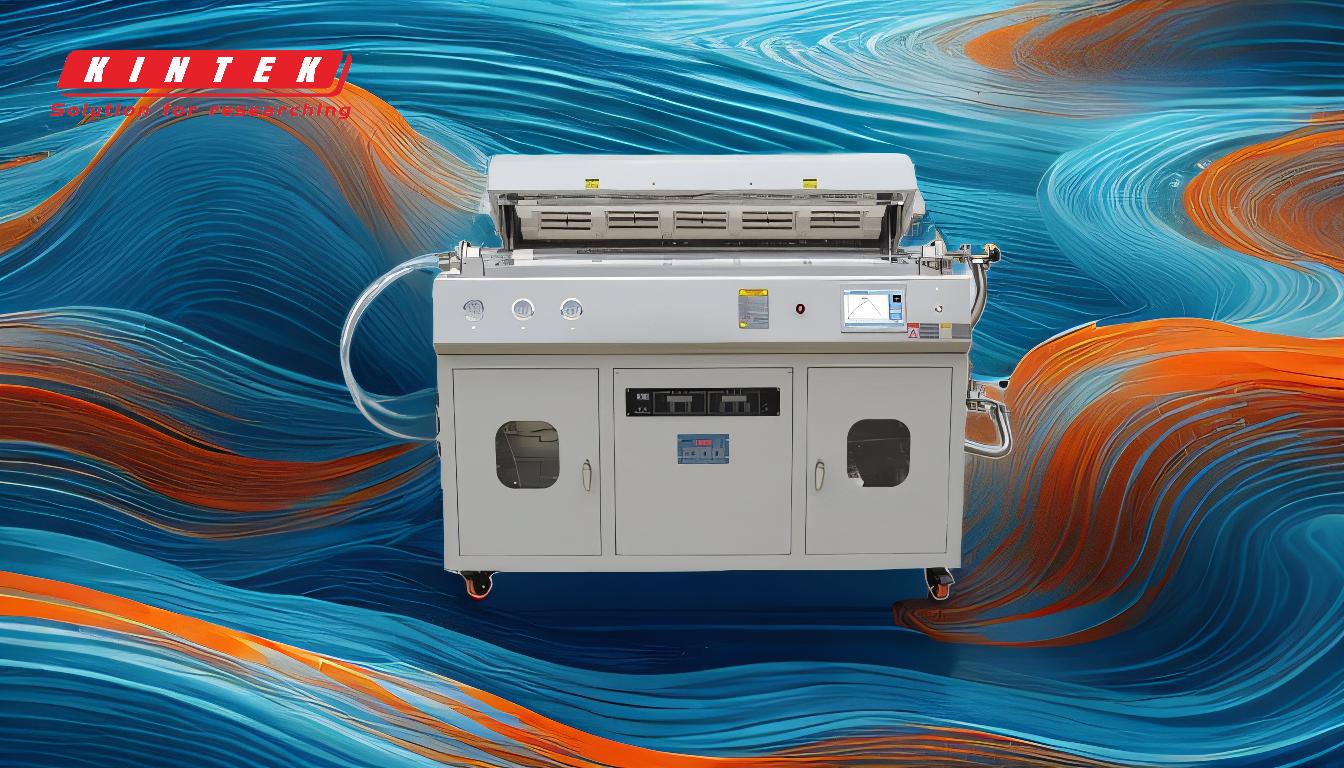
-
CVD Reactor Chamber:
- The reactor chamber is the core component of a CVD system. It provides a controlled environment where the chemical reactions take place. The chamber must withstand high temperatures (typically 850-1100°C) and corrosive gases. Materials like quartz, stainless steel, or ceramics are commonly used for construction.
- The chamber design varies depending on the type of CVD process (e.g., atmospheric pressure CVD, low-pressure CVD, or plasma-enhanced CVD). It must ensure uniform gas flow and temperature distribution to achieve consistent film deposition.
-
Gas Delivery System:
- The gas delivery system is responsible for supplying the precursor gases and carrier gases to the reactor chamber. It includes mass flow controllers, gas cylinders, and tubing.
- Precursor gases are chosen based on the desired film material (e.g., methane for carbon-based films or silane for silicon-based films). Carrier gases, such as argon or nitrogen, help transport the precursors and control the reaction environment.
-
Heating System:
- CVD processes require high temperatures to activate the chemical reactions. The heating system can include resistive heaters, induction heaters, or infrared lamps.
- The substrate must be heated uniformly to ensure even film growth. In some cases, the chamber itself is heated, while in others, the substrate is directly heated.
-
Vacuum System:
- Many CVD processes operate under reduced pressure to enhance gas diffusion and reaction kinetics. A vacuum pump is used to achieve and maintain the desired pressure within the reactor chamber.
- The vacuum system must be compatible with the process gases and capable of handling potential byproducts.
-
Plasma or Laser-Assisted Equipment (Optional):
- For processes like Plasma Enhanced Chemical Vapour Deposition (PECVD), a plasma source is required to ionize the precursor gases, allowing deposition at lower temperatures.
- Laser-assisted CVD uses focused laser beams to locally heat the substrate, enabling precise control over film growth.
-
Exhaust and Byproduct Management:
- The exhaust system removes reaction byproducts and unreacted gases from the chamber. It often includes scrubbers or filters to neutralize hazardous chemicals.
- Proper byproduct management is critical for safety and environmental compliance.
-
Substrate Holder and Manipulation System:
- The substrate holder must securely hold the substrate while allowing for uniform exposure to the precursor gases. It may include rotation or translation mechanisms to improve film uniformity.
- The holder material should be compatible with the process conditions and the substrate material.
-
Monitoring and Control Systems:
- Sensors and control systems are used to monitor parameters such as temperature, pressure, gas flow rates, and film thickness. These systems ensure process repeatability and quality control.
- Advanced CVD systems may include in-situ diagnostics, such as optical emission spectroscopy or quartz crystal microbalance, for real-time monitoring.
-
Cooling System:
- After deposition, the substrate and chamber must be cooled to prevent thermal stress or damage. A cooling system, such as water cooling or forced air, is often integrated into the CVD setup.
-
Safety Equipment:
- CVD processes involve hazardous gases and high temperatures, so safety equipment is essential. This includes gas detectors, emergency shut-off systems, and proper ventilation.
- Operators must follow strict safety protocols to minimize risks.
By carefully selecting and integrating these components, a CVD system can be tailored to meet specific application requirements, ensuring high-quality film deposition with excellent control over material properties.
Summary Table:
Component | Function | Key Features |
---|---|---|
CVD Reactor Chamber | Provides a controlled environment for chemical reactions | Withstands high temperatures (850-1100°C), made of quartz, stainless steel, or ceramics |
Gas Delivery System | Supplies precursor and carrier gases | Includes mass flow controllers, gas cylinders, and tubing |
Heating System | Activates chemical reactions with high temperatures | Uses resistive heaters, induction heaters, or infrared lamps |
Vacuum System | Enhances gas diffusion and reaction kinetics | Includes vacuum pumps compatible with process gases |
Plasma/Laser-Assisted Equipment | Enables lower-temperature deposition or precise control | Optional for PECVD or laser-assisted CVD |
Exhaust and Byproduct Management | Removes reaction byproducts and unreacted gases | Includes scrubbers or filters for safety and compliance |
Substrate Holder | Holds and manipulates the substrate for uniform exposure | May include rotation or translation mechanisms |
Monitoring and Control Systems | Ensures process repeatability and quality control | Includes sensors for temperature, pressure, gas flow rates, and film thickness |
Cooling System | Prevents thermal stress after deposition | Uses water cooling or forced air |
Safety Equipment | Ensures safe operation with hazardous gases and high temperatures | Includes gas detectors, emergency shut-off systems, and ventilation |
Need a customized CVD system for your application? Contact our experts today to get started!