Graphite furnaces are primarily used for high-temperature processes that require an inert atmosphere to prevent oxidation or other unwanted chemical reactions. The gases commonly used in graphite furnaces include Argon, Nitrogen, Helium, or non-flammable forming gas. These gases are chosen for their inert properties, which ensure that the materials being processed are not chemically altered during heating. The selection of gas depends on the specific application, temperature requirements, and material compatibility. Below, we explore the key points related to the gases used in graphite furnaces and their significance.
Key Points Explained:
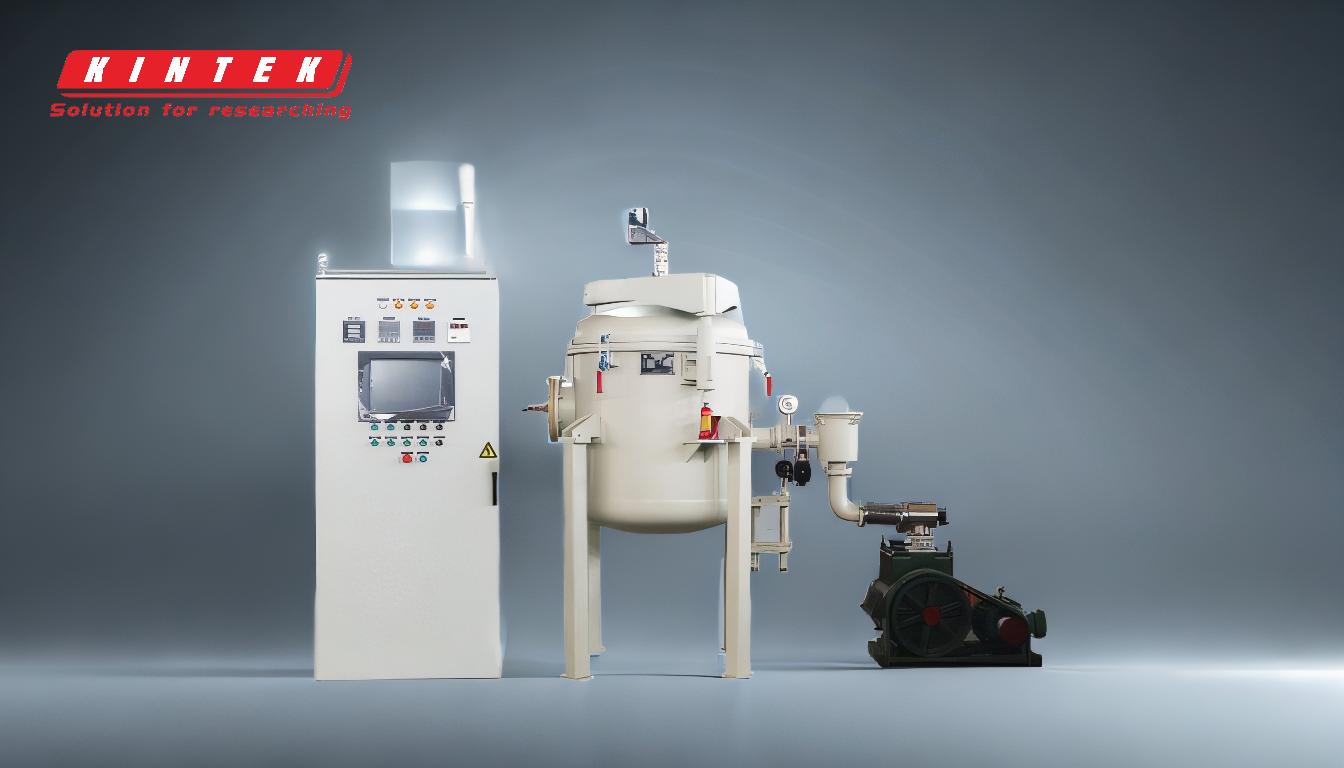
-
Purpose of Inert Gases in Graphite Furnaces
- Inert gases are used to create a controlled atmosphere that prevents oxidation, contamination, or unwanted chemical reactions during high-temperature processes.
- Graphite furnaces are often employed for heat treatments, melting, sintering, and other applications where maintaining material integrity is critical.
-
Common Gases Used
-
Argon:
- Argon is a popular choice due to its high inertness and availability.
- It is heavier than air, providing better coverage and protection in the furnace chamber.
- Suitable for high-temperature applications, such as melting alloys or sintering.
-
Nitrogen:
- Nitrogen is cost-effective and widely used in applications where extreme inertness is not required.
- It is lighter than Argon, making it suitable for processes that do not involve highly reactive materials.
- However, nitrogen may react with certain materials at high temperatures, so compatibility must be ensured.
-
Helium:
- Helium is highly inert and has excellent thermal conductivity, making it ideal for processes requiring rapid heat transfer.
- It is lighter than Argon and Nitrogen, which can affect its distribution in the furnace chamber.
- Often used in specialized applications, such as foaming or reaction kinetics studies.
-
Non-flammable Forming Gas:
- This is typically a mixture of inert gases (e.g., Argon and Nitrogen) with a small percentage of hydrogen.
- Used in applications where a reducing atmosphere is needed to prevent oxidation.
- The hydrogen content must be carefully controlled to avoid flammability risks.
-
Argon:
-
Factors Influencing Gas Selection
-
Application Requirements:
- The type of material being processed and the desired outcome (e.g., melting, sintering, or foaming) influence the choice of gas.
-
Temperature Range:
- Some gases, like Argon, are better suited for extremely high temperatures, while others, like Nitrogen, may have limitations.
-
Cost and Availability:
- Nitrogen is often preferred for cost-sensitive applications, while Argon and Helium are used when performance is prioritized.
-
Safety Considerations:
- Non-flammable forming gas must be handled carefully to avoid flammability risks, especially in high-temperature environments.
-
Application Requirements:
-
Applications of Graphite Furnaces
-
Melting and Alloying:
- Graphite furnaces are used to melt metals and create alloys in an inert atmosphere to prevent contamination.
-
Pressure Sintering:
- Sintering processes benefit from inert gases to ensure uniform material properties and prevent oxidation.
-
Foaming and Reaction Kinetics:
- Inert gases are essential for studying high-temperature reactions and creating foamed materials.
-
Heating Solid Electrolytes:
- Solid electrolytes used in batteries and fuel cells are often processed in graphite furnaces under inert conditions.
-
Melting and Alloying:
-
Advantages of Using Inert Gases
-
Material Integrity:
- Prevents oxidation, decarburization, and other chemical reactions that could degrade the material.
-
Process Control:
- Provides a stable environment for precise temperature and pressure control.
-
Versatility:
- Suitable for a wide range of materials and processes, from metals to ceramics.
-
Material Integrity:
-
Considerations for Equipment Purchasers
-
Gas Compatibility:
- Ensure the furnace design supports the chosen gas and can handle its flow rate and pressure requirements.
-
Safety Features:
- Look for furnaces with built-in safety mechanisms, such as gas leak detectors and automatic shut-off systems.
-
Operational Costs:
- Factor in the cost of gas consumption and availability when selecting a furnace.
-
Maintenance Requirements:
- Consider the ease of maintenance and the availability of replacement parts for the gas delivery system.
-
Gas Compatibility:
In conclusion, the choice of gas in a graphite furnace depends on the specific application, material requirements, and operational considerations. Argon, Nitrogen, Helium, and non-flammable forming gas are the most commonly used options, each offering unique advantages. Equipment purchasers should carefully evaluate these factors to select the most suitable gas and furnace configuration for their needs.
Summary Table:
Gas | Properties | Applications |
---|---|---|
Argon | High inertness, heavier than air, excellent for high-temperature processes | Melting alloys, sintering, high-temperature treatments |
Nitrogen | Cost-effective, lighter than Argon, suitable for less reactive materials | General heat treatment, cost-sensitive applications |
Helium | Highly inert, excellent thermal conductivity, lighter than Argon and Nitrogen | Foaming, reaction kinetics studies, rapid heat transfer processes |
Non-flammable Forming Gas | Mixture of inert gases with hydrogen, reduces oxidation risks | Applications requiring a reducing atmosphere, controlled hydrogen environments |
Need help selecting the right gas for your graphite furnace? Contact our experts today for personalized advice!