When atoms are deposited on surfaces at higher temperatures, several key phenomena occur that significantly influence the characteristics of the resulting film. Higher temperatures enhance surface reactions, leading to denser films with improved composition. However, the process temperature must be carefully controlled, as it can also lead to unintended consequences such as the degradation of sensitive components or the extraction of unwanted materials, which can compromise the quality of the final product. Understanding these effects is crucial for optimizing deposition processes in various applications.
Key Points Explained:
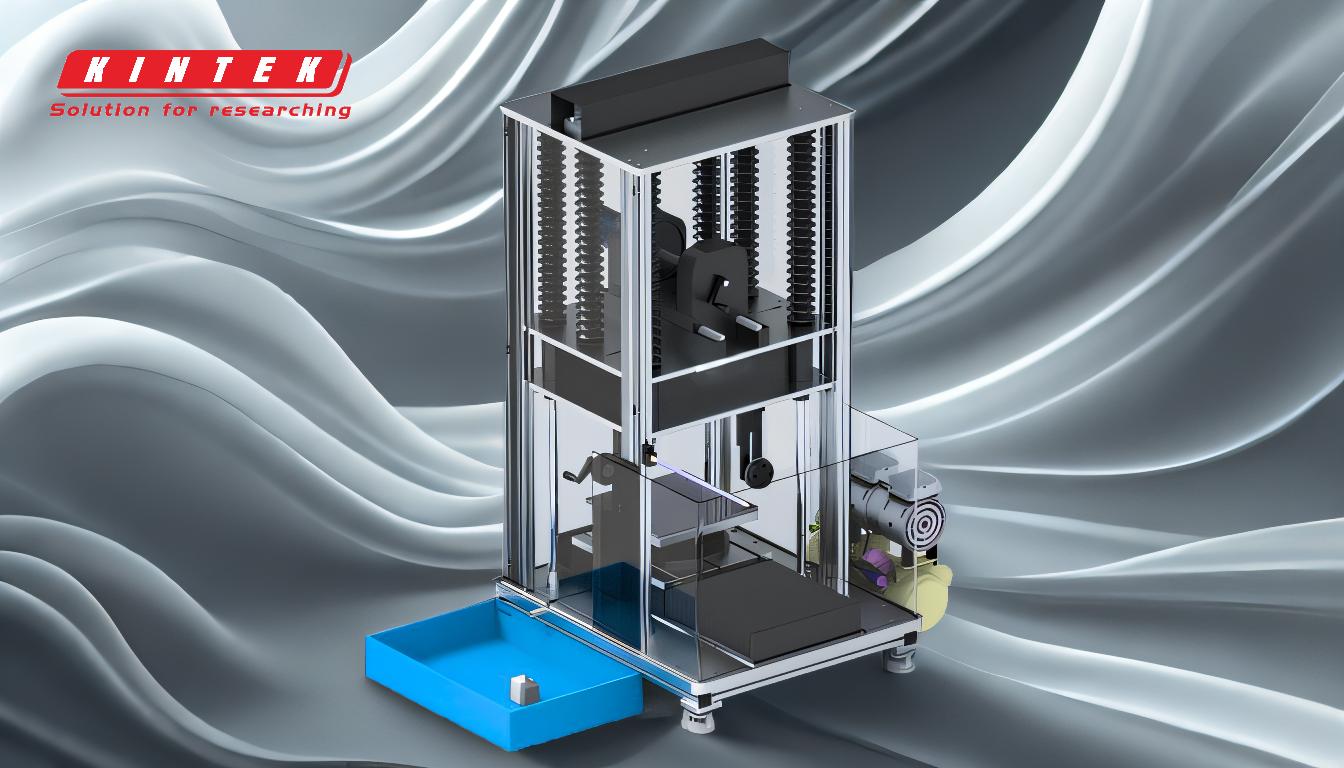
-
Effect of Temperature on Film Density and Composition:
- Higher substrate temperatures during deposition enhance surface reactions, leading to a denser deposited film. This is because increased thermal energy allows atoms to diffuse more effectively across the surface, filling in gaps and creating a more uniform and compact structure.
- The improved composition of the film at higher temperatures is due to better atomic mobility, which facilitates the formation of more stable and ordered structures.
-
Impact on Film Quality:
- While higher temperatures can improve the density and composition of the film, they can also pose risks to the quality of the final product. For instance, in processes involving sensitive materials like terpenoids or cannabinoids, elevated temperatures can lead to degradation or denaturation, resulting in a lower quality product.
- The extraction of unwanted materials, such as waxes or resins, increases at higher temperatures, which can further degrade the quality of the film or the final product.
-
Application-Specific Temperature Limits:
- The choice of deposition temperature is often constrained by the specific requirements of the application. For example, in the production of CBD/THC products, higher temperatures can decrease the concentration of desirable compounds like terpenoids, leading to a less effective or less desirable product.
- In other applications, such as semiconductor manufacturing, higher temperatures might be necessary to achieve the desired film properties, but they must be carefully balanced to avoid damaging the substrate or other components.
-
Trade-offs in Process Optimization:
- Optimizing the deposition process involves balancing the benefits of higher temperatures, such as improved film density and composition, against the potential drawbacks, such as the risk of degrading sensitive materials or extracting unwanted components.
- Process engineers must consider the specific requirements of the application and the properties of the materials involved to determine the optimal deposition temperature.
-
Practical Considerations for Equipment and Consumables:
- When selecting equipment for high-temperature deposition processes, it is important to choose materials and components that can withstand the elevated temperatures without degrading or introducing contaminants.
- Consumables used in the deposition process, such as substrates or target materials, must also be compatible with the chosen temperature range to ensure consistent and high-quality results.
By understanding these key points, equipment and consumable purchasers can make informed decisions about the materials and processes they use, ensuring that they achieve the desired film properties while minimizing the risks associated with higher deposition temperatures.
Summary Table:
Key Factor | Effect at Higher Temperatures |
---|---|
Film Density | Increased due to enhanced surface reactions and better atomic mobility. |
Film Composition | Improved as atoms form more stable and ordered structures. |
Film Quality | May degrade for sensitive materials (e.g., terpenoids, cannabinoids) due to thermal degradation. |
Unwanted Material Extraction | Increases, potentially compromising film or product quality. |
Application-Specific Limits | Temperature must align with material and process requirements to avoid damage. |
Process Optimization | Balance benefits of higher temperatures with risks of degradation or contamination. |
Equipment and Consumables | Must withstand high temperatures without degrading or introducing contaminants. |
Need help optimizing your deposition process? Contact our experts today for tailored solutions!