A controlled atmosphere temperature treatment system is a specialized equipment used in heat treatment processes to modify the properties of metal parts by heating them in a precisely controlled environment. This system involves regulating the composition and flow of gases (such as CO2, O2, and others) within a sealed furnace to create an optimal atmosphere for heat treatment. The process enhances the microstructure of metals, improving their strength, toughness, wear resistance, and corrosion resistance. Key components of such systems include integral tempering ovens, parts washers, and load transfer cars, which work together to ensure precise temperature control, minimal oxidation, and high-quality, consistent results. These systems are widely used in industries requiring high-performance metal components.
Key Points Explained:
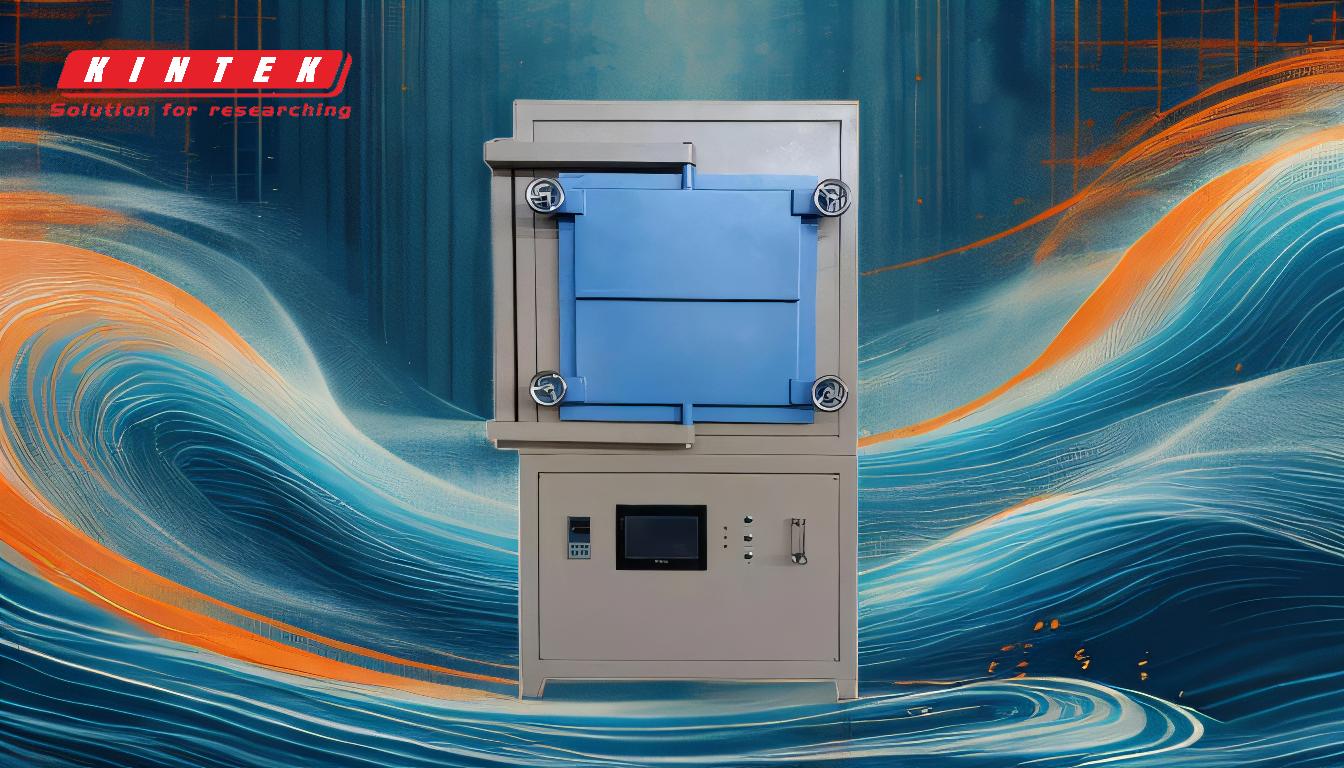
-
Definition and Purpose:
- A controlled atmosphere temperature treatment system is designed to heat metal parts in a precisely regulated environment to alter their physical and mechanical properties.
- The primary purpose is to improve the microstructure of metals, enhancing properties such as strength, toughness, wear resistance, and corrosion resistance.
-
Key Components:
- Controlled Atmosphere Furnace: The core component where the heat treatment occurs. It maintains a specific gas composition (e.g., elevated CO2, reduced O2) to prevent oxidation and decarburization.
- Integral Tempering Oven: Used to temper the metal after heating, ensuring the desired hardness and toughness.
- Parts Washer: Cleans parts before and after treatment to remove contaminants and ensure consistent results.
- Load Transfer Cars: Facilitate the movement of parts between different stages of the heat treatment process, ensuring efficiency and automation.
-
Process Overview:
- Heating: Metal parts are heated in a controlled atmosphere furnace to a specific temperature.
- Cooling: Rapid cooling (quenching) is applied to achieve the desired microstructure and mechanical properties.
- Tempering: Additional heating and cooling steps may be used to fine-tune the hardness and toughness of the metal.
-
Benefits of Controlled Atmosphere:
- Improved Product Quality: Precise control of the atmosphere minimizes oxidation and decarburization, leading to higher-quality parts.
- Enhanced Mechanical Properties: The process improves strength, toughness, and resistance to wear and corrosion.
- Increased Production Efficiency: Automation and mechanization reduce labor intensity and improve productivity.
- Material Savings: Reduced burning and decarburization during heating save materials and improve part quality.
-
Applications:
- Automotive Industry: Used for heat-treating engine components, gears, and other high-stress parts.
- Aerospace Industry: Enhances the performance of critical components like turbine blades and structural parts.
- Tool Manufacturing: Improves the durability and performance of cutting tools and dies.
- General Manufacturing: Used for a wide range of metal parts requiring enhanced mechanical properties.
-
Key Features of Controlled Atmosphere Furnaces:
- High Sealing Requirements: Ensures no external air enters the furnace, maintaining the controlled atmosphere.
- Uniform Atmosphere: Achieved through precise gas flow control, ensuring consistent treatment across all parts.
- Anti-Carburizing Bricks: Used to prevent carburization of the furnace lining, extending its lifespan.
- Safety Features: Includes fire curtains and explosion-proof devices to ensure safe operation.
- Automation: High degree of mechanization and automation reduces human error and increases efficiency.
-
Advantages Over Traditional Heat Treatment:
- Minimal Oxidation and Decarburization: Controlled atmosphere prevents surface degradation, leading to better part quality.
- Precision Control: Allows for strict control of carbon content and other parameters, ensuring consistent results.
- Versatility: Can be used for a wide range of metals and alloys, including complex-shaped parts.
- Cost-Effectiveness: Reduces material waste and improves production efficiency, lowering overall costs.
In summary, a controlled atmosphere temperature treatment system is a sophisticated and highly effective solution for enhancing the properties of metal parts. By carefully controlling the heating environment, these systems deliver superior quality, consistency, and efficiency, making them indispensable in industries requiring high-performance metal components.
Summary Table:
Aspect | Details |
---|---|
Purpose | Enhances metal microstructure for improved strength, toughness, and resistance. |
Key Components | Controlled atmosphere furnace, integral tempering oven, parts washer, load transfer cars. |
Process Steps | Heating, cooling (quenching), and tempering. |
Benefits | Improved product quality, enhanced mechanical properties, increased efficiency. |
Applications | Automotive, aerospace, tool manufacturing, general manufacturing. |
Key Features | High sealing, uniform atmosphere, anti-carburizing bricks, safety features, automation. |
Advantages | Minimal oxidation, precision control, versatility, cost-effectiveness. |
Discover how a controlled atmosphere temperature treatment system can revolutionize your metal processing—contact us today!