A Chemical Vapor Deposition (CVD) system is a sophisticated technology used to deposit thin films of materials onto a substrate through chemical reactions in the vapor phase. This process is widely utilized across various industries, including electronics, optics, and materials science, to produce coatings, semiconductors, composites, and more. CVD systems enable the creation of materials with specific properties, such as corrosion resistance, wear resistance, and enhanced thermal or optical characteristics. The process involves reacting volatile compounds with other gases at high temperatures to form a non-volatile solid film on a heated substrate. CVD is versatile, offering methods like Plasma-Enhanced CVD (PECVD) that allow for lower deposition temperatures and energy-efficient processes.
Key Points Explained:
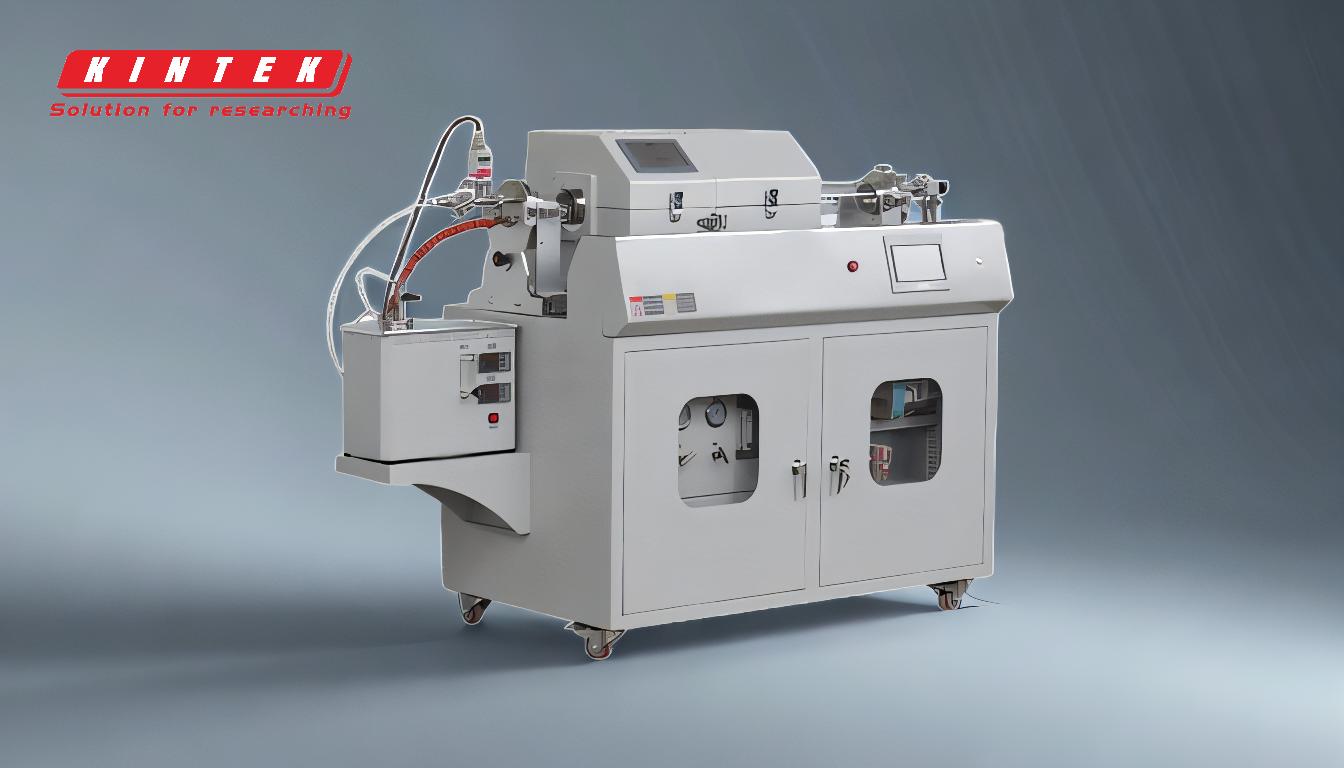
-
Definition of CVD:
- Chemical Vapor Deposition (CVD) is a process where gases react thermochemically at high temperatures to form a solid film on a substrate. This method is particularly useful for creating thin films with precise properties, such as durability, friction reduction, and thermal improvement.
-
Applications of CVD:
- Electronics Industry: CVD is crucial in the manufacture of semiconductors and chips, enabling the production of high-performance electronic components.
- Optical Coatings: CVD is used to apply coatings on glass and plastic to enhance optical properties, such as anti-reflective or heat-protective layers.
- Wear and Corrosion Resistance: Materials treated with CVD exhibit improved resistance to wear and corrosion, making them ideal for industrial tools and machinery.
- Synthetic Diamond Layers: CVD is employed to deposit synthetic diamond layers on tools, enhancing their hardness and durability.
- Nanotechnology: CVD is instrumental in producing nanomaterials, such as nanomachines, filaments, and whiskers, which are essential for advanced technological applications.
-
CVD Process Details:
- The process involves introducing volatile compounds into a reaction chamber, where they chemically react with other gases at elevated temperatures. The resulting non-volatile solid deposits onto a heated substrate, forming a thin film.
- Plasma-Enhanced CVD (PECVD): This variant uses plasma to initiate chemical reactions at lower temperatures, offering advantages such as reduced energy consumption and minimal environmental impact.
-
Advantages of CVD:
- Versatility: CVD can deposit a wide range of materials, including metals, ceramics, and composites, with precise control over film properties.
- High-Quality Films: The process produces uniform, high-purity films with excellent adhesion to the substrate.
- Scalability: CVD is suitable for both small-scale laboratory research and large-scale industrial production.
-
Components of a CVD System:
- Reaction Chamber: The core component where chemical reactions occur and the thin film is deposited.
- Gas Delivery System: Controls the flow of reactive gases into the chamber.
- Heating System: Maintains the high temperatures required for the chemical reactions.
- Vacuum System: Ensures a controlled environment by removing unwanted gases and impurities.
- Control System: Manages process parameters such as temperature, pressure, and gas flow for precise film deposition.
-
Future Trends in CVD:
- Low-Temperature CVD: Ongoing research aims to develop CVD processes that operate at lower temperatures, reducing energy consumption and expanding the range of compatible substrates.
- Green CVD: Efforts are being made to minimize the environmental impact of CVD by using non-toxic precursors and reducing waste.
- Integration with Additive Manufacturing: Combining CVD with 3D printing technologies to create complex, multi-material structures with tailored properties.
In summary, CVD systems are essential tools in modern materials science and technology, enabling the production of advanced materials with tailored properties for a wide range of applications. Their versatility, precision, and scalability make them indispensable in industries ranging from electronics to nanotechnology.
Summary Table:
Key Aspect | Details |
---|---|
Definition | Process where gases react at high temperatures to form solid films on substrates. |
Applications | Electronics, optical coatings, wear/corrosion resistance, synthetic diamonds, nanotechnology. |
Advantages | Versatility, high-quality films, scalability, and precise control. |
Components | Reaction chamber, gas delivery system, heating system, vacuum system, control system. |
Future Trends | Low-temperature CVD, green CVD, integration with additive manufacturing. |
Ready to explore how a CVD system can transform your applications? Contact us today to learn more!