A furnace used for smelting is a high-temperature device designed to extract metals from their ores by heating them beyond their melting points. Smelting furnaces are critical in metallurgy and materials science, as they enable the separation of metal from impurities through chemical reactions and heat. These furnaces are used in industries such as mining, manufacturing, and recycling, where they play a vital role in producing pure metals for further processing. Smelting furnaces come in various types, each tailored to specific materials and processes, and they often operate under controlled atmospheres to ensure efficient and safe metal extraction.
Key Points Explained:
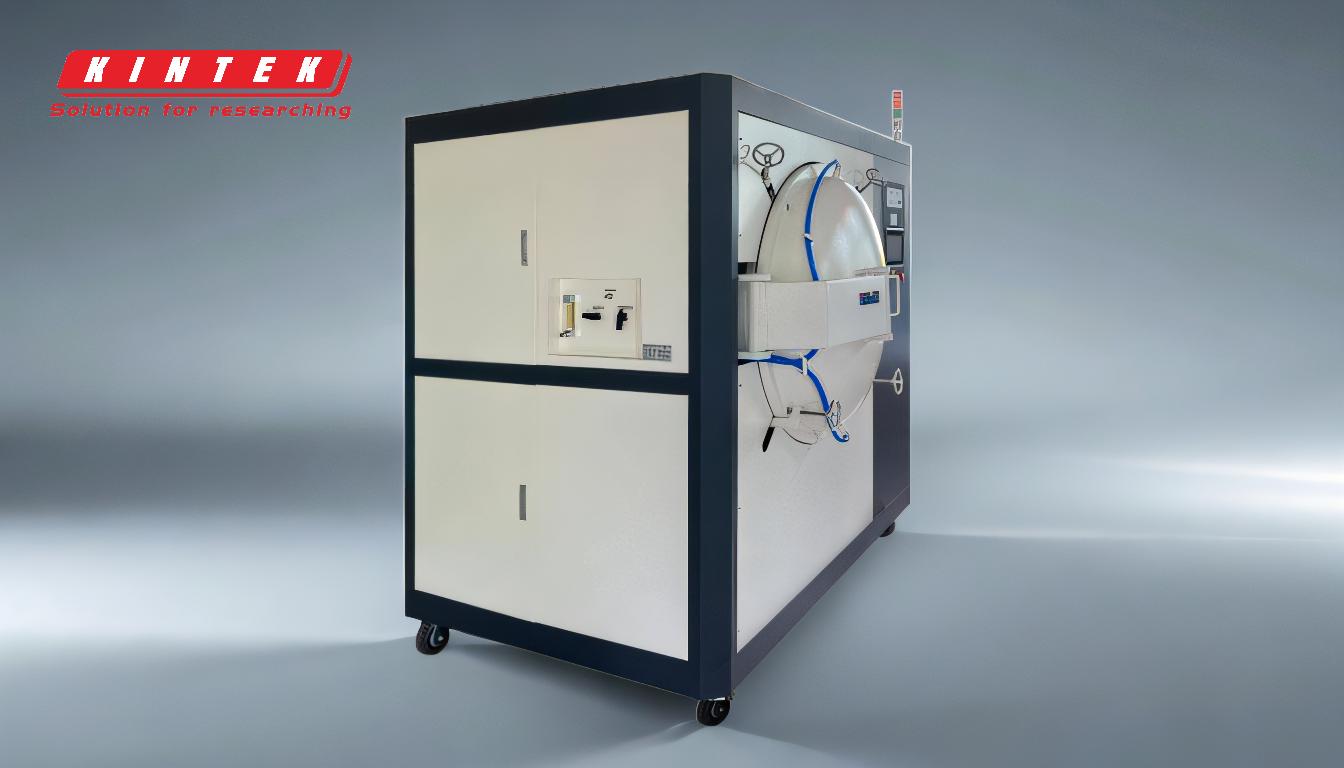
-
Purpose of a Smelting Furnace:
- A smelting furnace is primarily used to extract metals from their ores by applying intense heat. This process involves heating the ore to a temperature high enough to melt the metal, allowing it to separate from impurities and other non-metallic components.
- Smelting is a critical step in metallurgy, enabling the production of pure metals for industrial applications, such as manufacturing, construction, and electronics.
-
Types of Smelting Furnaces:
- Blast Furnace: Commonly used for iron smelting, a blast furnace uses a combination of heat, air, and chemical reactions to reduce iron ore into molten iron. It operates continuously and is essential in steel production.
- Reverberatory Furnace: This furnace is used for smelting non-ferrous metals like copper and tin. It uses indirect heating, where flames heat the metal indirectly through the furnace walls.
- Electric Arc Furnace: Ideal for recycling scrap metal, this furnace uses an electric arc to generate the high temperatures needed to melt metals. It is energy-efficient and widely used in steelmaking.
- Induction Furnace: This type uses electromagnetic induction to heat and melt metals. It is highly efficient and suitable for small-scale smelting operations.
-
Key Components of a Smelting Furnace:
- Heating Chamber: The core of the furnace where the ore is heated to high temperatures. It is designed to withstand extreme heat and chemical reactions.
- Fuel Source: Smelting furnaces use various fuel sources, such as coal, natural gas, or electricity, to generate the necessary heat.
- Refractory Lining: The interior of the furnace is lined with refractory materials that can withstand high temperatures and resist chemical corrosion.
- Airflow System: Many furnaces, like the blast furnace, require a controlled airflow to facilitate combustion and chemical reactions.
-
Applications of Smelting Furnaces:
- Mining and Extraction: Smelting furnaces are essential in mining operations to extract metals like iron, copper, and aluminum from their ores.
- Recycling: Furnaces are used to recycle scrap metal, reducing waste and conserving natural resources.
- Manufacturing: Smelted metals are used to produce a wide range of products, from construction materials to electronic components.
-
Advantages of Smelting Furnaces:
- Efficiency: Modern smelting furnaces are designed to maximize energy efficiency and reduce waste.
- Versatility: They can process a wide range of ores and metals, making them indispensable in various industries.
- Controlled Atmospheres: Many furnaces can operate under specific atmospheric conditions, such as inert or oxidizing environments, to optimize the smelting process.
-
Challenges and Considerations:
- Environmental Impact: Smelting can produce harmful emissions, such as carbon dioxide and sulfur dioxide, which require proper management and mitigation.
- Energy Consumption: High-temperature operations demand significant energy, making energy efficiency a priority in furnace design.
- Safety: Operating a smelting furnace requires strict safety protocols to prevent accidents and ensure worker safety.
In summary, a furnace used for smelting is a versatile and essential tool in metallurgy, enabling the extraction and purification of metals for industrial use. Its design, operation, and applications vary depending on the type of metal being processed and the specific requirements of the industry.
Summary Table:
Aspect | Details |
---|---|
Purpose | Extracts metals from ores by heating beyond melting points. |
Types | Blast, Reverberatory, Electric Arc, Induction furnaces. |
Key Components | Heating chamber, fuel source, refractory lining, airflow system. |
Applications | Mining, recycling, manufacturing. |
Advantages | High efficiency, versatility, controlled atmospheres. |
Challenges | Environmental impact, energy consumption, safety concerns. |
Need a smelting furnace tailored to your needs? Contact our experts today for personalized solutions!