A nitriding furnace is a specialized piece of equipment used to enhance the surface properties of metals, particularly by increasing their hardness and corrosion resistance. This is achieved by heating the metal in a nitrogen-rich environment, typically using ammonia as the nitrogen source. The furnace is designed to maintain precise temperature and atmosphere control, ensuring optimal results for the nitriding process. Nitriding furnaces are widely used in industries such as metallurgy, machinery, and electronics, where improved material performance is critical. The process is essential for applications requiring high wear resistance and durability, such as in automotive components, tools, and industrial machinery.
Key Points Explained:
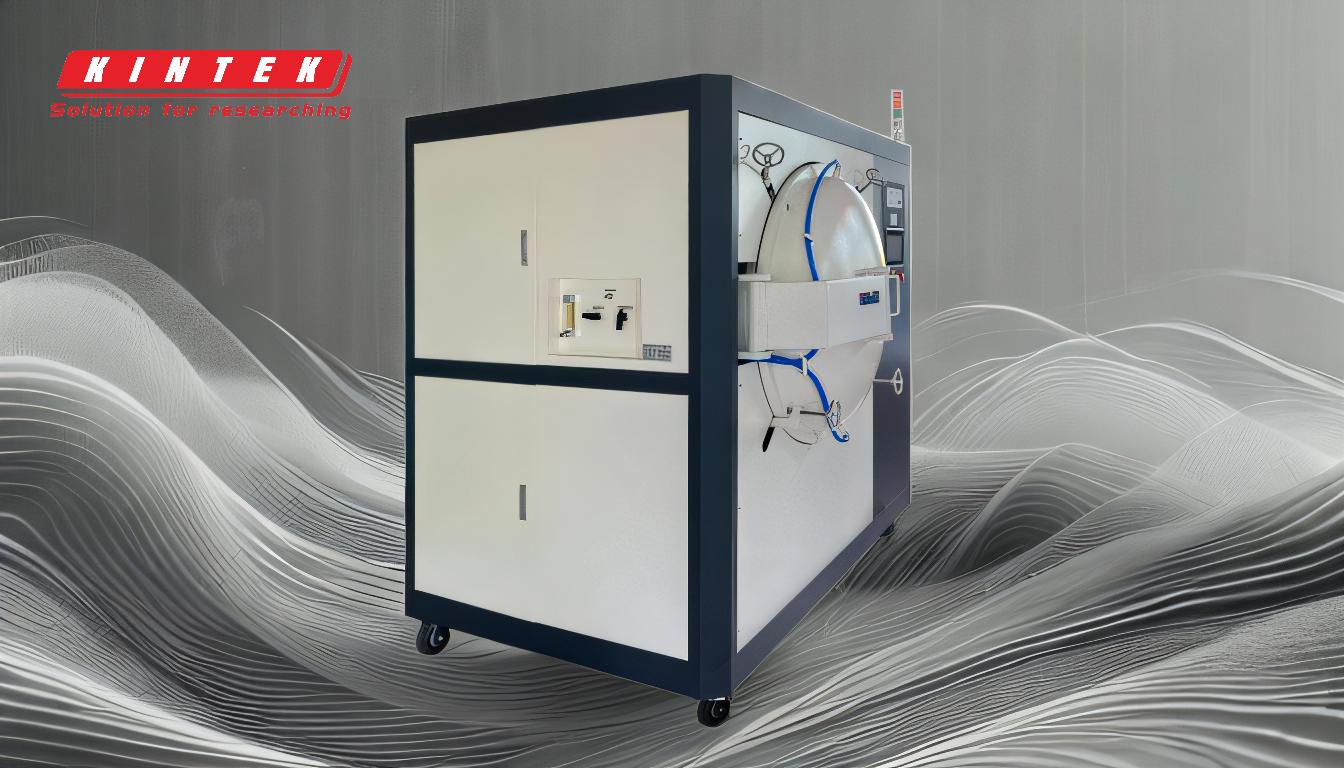
-
Purpose of a Nitriding Furnace:
- A nitriding furnace is primarily used to improve the surface properties of metals, such as hardness and corrosion resistance. This is achieved through a process called nitriding, where the metal is heated in a nitrogen-rich atmosphere, often using ammonia as the nitrogen source.
-
Nitriding Process:
- The nitriding process involves heating the metal to a specific temperature in a controlled nitrogen atmosphere. The nitrogen diffuses into the surface of the metal, forming hard nitrides that enhance the material's properties. This process is typically carried out at temperatures ranging from 500°C to 600°C.
-
Applications of Nitriding Furnaces:
- Nitriding furnaces are used in various industries, including metallurgy, machinery, electronics, and automotive. They are essential for producing components that require high wear resistance, such as gears, crankshafts, and cutting tools. The process is also used in the production of molds and dies, where surface hardness is critical.
-
Types of Nitriding Processes:
- There are several types of nitriding processes, including gas nitriding, plasma nitriding, and salt bath nitriding. Each method has its own advantages and is chosen based on the specific requirements of the application. Gas nitriding, for example, is widely used due to its ability to produce a uniform and controllable nitride layer.
-
Atmosphere Control:
- The atmosphere within the nitriding furnace is carefully controlled to ensure the desired surface reactions occur. In the case of gas nitriding, the atmosphere is typically composed of ammonia, which decomposes to release nitrogen at high temperatures. This nitrogen then diffuses into the metal surface, forming nitrides.
-
Benefits of Nitriding:
- The primary benefits of nitriding include increased surface hardness, improved wear resistance, and enhanced corrosion resistance. These properties make nitrided components more durable and longer-lasting, reducing the need for frequent replacements and maintenance.
-
Comparison with Other Heat Treatment Processes:
- Nitriding is often compared to other heat treatment processes, such as carburizing and case hardening. While carburizing involves adding carbon to the surface of the metal, nitriding adds nitrogen. Nitriding typically results in a harder surface layer compared to carburizing, and it can be performed at lower temperatures, reducing the risk of distortion.
-
Industrial Importance:
- The use of nitriding furnaces is critical in industries where high-performance materials are required. For example, in the automotive industry, nitrided components such as crankshafts and camshafts are essential for ensuring the longevity and reliability of engines. Similarly, in the tooling industry, nitrided cutting tools offer superior performance and longer service life.
-
Future Trends:
- Advances in nitriding technology are focused on improving process efficiency, reducing energy consumption, and enhancing the quality of the nitride layer. Innovations such as plasma nitriding and the use of advanced control systems are expected to drive the future development of nitriding furnaces.
-
Conclusion:
- In summary, a nitriding furnace is a vital piece of equipment in the field of metallurgy and materials science. It plays a crucial role in enhancing the surface properties of metals, making them more durable and resistant to wear and corrosion. The controlled nitrogen atmosphere within the furnace ensures that the nitriding process is carried out effectively, resulting in high-quality components that meet the demanding requirements of various industries. For more information on the types of furnaces used in such processes, you can refer to the nitrogen atmosphere furnace.
Summary Table:
Aspect | Details |
---|---|
Purpose | Enhances metal hardness and corrosion resistance through nitriding. |
Process | Heats metal in a nitrogen-rich atmosphere (500°C–600°C) to form nitrides. |
Applications | Automotive, machinery, electronics, and tooling industries. |
Types of Nitriding | Gas nitriding, plasma nitriding, salt bath nitriding. |
Benefits | Increased hardness, wear resistance, and corrosion resistance. |
Industrial Importance | Critical for high-performance components like gears, crankshafts, and tools. |
Discover how a nitriding furnace can improve your metal components—contact us today!