Plasma coating, specifically plasma sputter coating, is a sophisticated technique used to apply thin, precise, and uniform coatings onto various surfaces. This method leverages plasma ions to vaporize the coating material, which then deposits onto the target surface. The process is highly effective for applications requiring meticulous control over coating thickness and uniformity, such as in the semiconductor industry, optics, and advanced materials research. The use of plasma ensures that the coating adheres strongly to the substrate, enhancing durability and performance.
Key Points Explained:
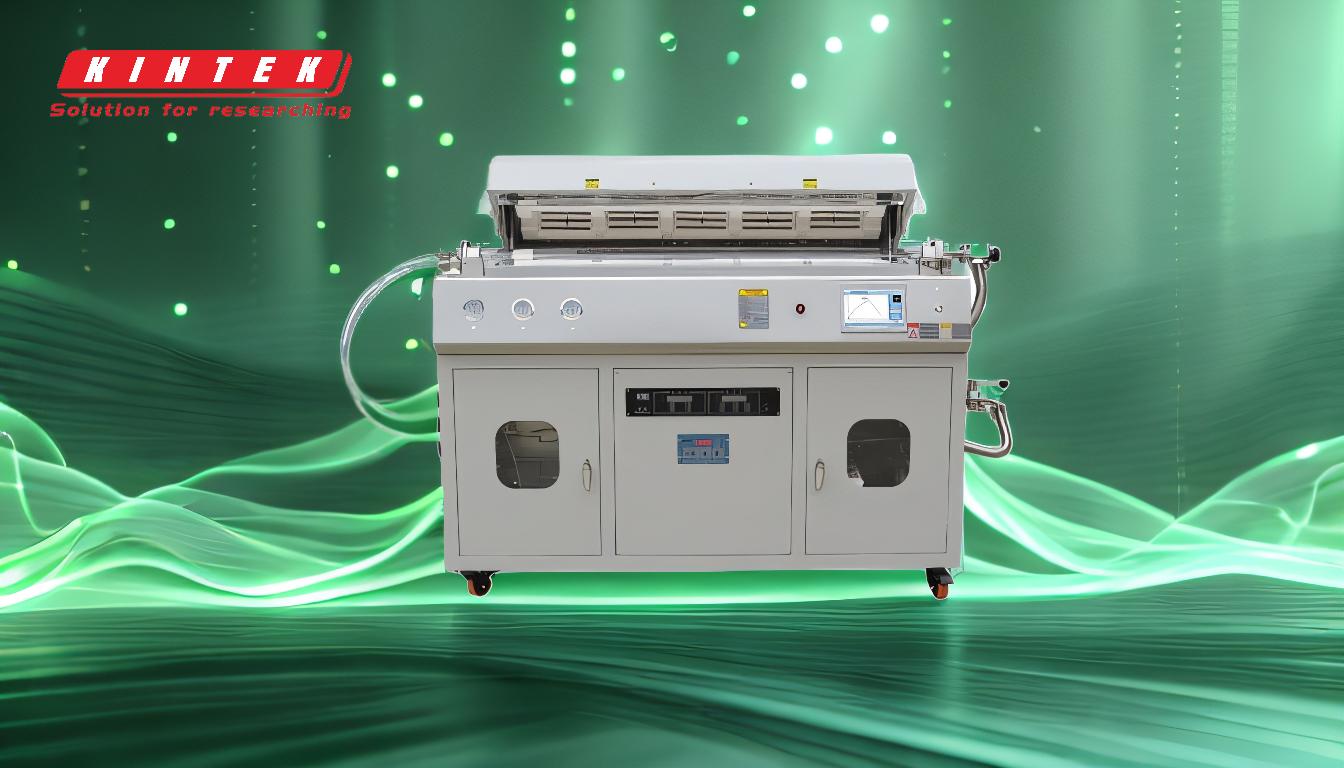
-
Definition of Plasma Sputter Coating:
- Plasma sputter coating is a process where plasma ions are used to vaporize a target material, which then deposits as a thin film onto a substrate. This technique is known for its ability to produce highly uniform and precise coatings.
-
How Plasma Sputter Coating Works:
- Plasma Generation: A plasma is created by ionizing a gas, typically argon, within a vacuum chamber. This plasma consists of positively charged ions and free electrons.
- Sputtering Process: The positively charged ions are accelerated towards a target material (the coating material). When these ions collide with the target, they dislodge atoms from the target's surface.
- Deposition: The dislodged atoms travel through the vacuum and deposit onto the substrate, forming a thin, uniform coating.
-
Advantages of Plasma Sputter Coating:
- Precision and Uniformity: The process allows for extremely precise control over the thickness and uniformity of the coating, making it ideal for applications where exact specifications are crucial.
- Strong Adhesion: The use of plasma ensures that the coating adheres strongly to the substrate, enhancing the durability and performance of the coated material.
- Versatility: Plasma sputter coating can be used with a wide range of materials, including metals, ceramics, and polymers, making it suitable for various industries.
-
Applications of Plasma Sputter Coating:
- Semiconductor Industry: Used for depositing thin films of materials like silicon dioxide and aluminum on semiconductor wafers.
- Optics: Applied in the production of anti-reflective coatings, mirrors, and other optical components.
- Advanced Materials Research: Utilized in the development of new materials with specific properties, such as enhanced conductivity or corrosion resistance.
-
Comparison with Other Coating Techniques:
- Physical Vapor Deposition (PVD): Similar to plasma sputter coating, PVD also involves the vaporization of a target material. However, PVD typically uses thermal evaporation or electron beams rather than plasma ions.
- Chemical Vapor Deposition (CVD): CVD involves chemical reactions to deposit a coating, whereas plasma sputter coating relies on physical processes. CVD can produce thicker coatings but may not offer the same level of precision.
-
Challenges and Considerations:
- Cost: The equipment and process can be expensive, making it less suitable for low-budget applications.
- Complexity: The process requires a high level of expertise and control, particularly in maintaining the vacuum and plasma conditions.
- Material Limitations: While versatile, not all materials are suitable for sputtering, and some may require special conditions or pre-treatment.
In summary, plasma sputter coating is a highly effective method for applying precise and uniform coatings, with strong adhesion and versatility across various industries. Despite its challenges, the benefits it offers in terms of precision and performance make it a valuable technique in advanced material applications.
Summary Table:
Aspect | Details |
---|---|
Definition | Plasma ions vaporize a target material, depositing it as a thin film. |
Process | Plasma generation, sputtering, and deposition in a vacuum chamber. |
Advantages | Precision, uniformity, strong adhesion, and material versatility. |
Applications | Semiconductors, optics, advanced materials research. |
Comparison with PVD/CVD | Offers higher precision than CVD, differs from PVD in ion-based sputtering. |
Challenges | High cost, complexity, and material limitations. |
Learn how plasma sputter coating can elevate your projects—contact our experts today!