A press die set is a specialized tool used in manufacturing processes, particularly in metalworking and plastic molding, to shape, cut, or form materials into specific designs or dimensions. It consists of two main components: the punch (upper die) and the die (lower die), which work together under high pressure to manipulate the material. Press die sets are integral to processes like stamping, forging, and extrusion, enabling the mass production of precise and consistent parts. They are commonly used in industries such as automotive, aerospace, and electronics, where high precision and repeatability are critical. The design of a press die set depends on the material being processed, the desired shape, and the production requirements.
Key Points Explained:
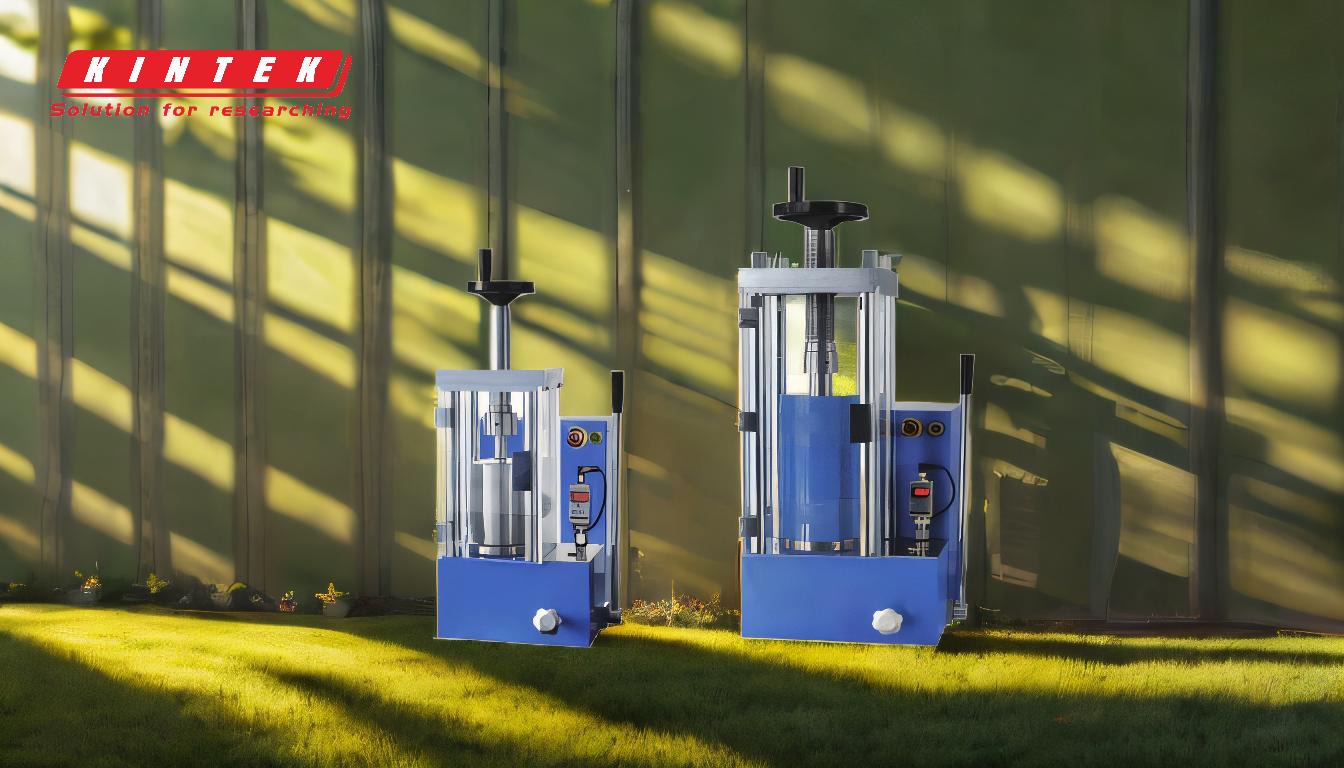
-
Definition and Purpose of a Press Die Set
A press die set is a tool assembly used in manufacturing to shape or cut materials into specific forms. It consists of two primary components: the punch and the die. The punch applies force to the material, while the die provides the desired shape or contour. This setup is essential for processes like stamping, forging, and extrusion, where precision and repeatability are crucial. -
Components of a Press Die Set
- Punch (Upper Die): The punch is the moving part of the die set that applies force to the material. It is designed to match the shape of the final product.
- Die (Lower Die): The die is the stationary part that holds the material in place and provides the cavity or contour into which the material is shaped.
- Guide Pins and Bushings: These components ensure proper alignment between the punch and die, maintaining precision during operation.
- Backing Plates: These provide support to the die and punch, distributing the force evenly and preventing deformation.
-
Types of Press Die Sets
- Simple Die Sets: Used for single operations like cutting or punching.
- Compound Die Sets: Perform multiple operations (e.g., cutting and forming) in a single stroke.
- Progressive Die Sets: Used in high-volume production, where the material moves through multiple stations, each performing a different operation.
- Transfer Die Sets: Similar to progressive dies but used for larger parts, where the material is transferred between stations manually or mechanically.
-
Applications of Press Die Sets
Press die sets are widely used in industries such as:- Automotive: For manufacturing car body parts, engine components, and brackets.
- Aerospace: For producing lightweight and high-strength components.
- Electronics: For creating precise and intricate parts like connectors and housings.
- Consumer Goods: For producing items like kitchen utensils, appliances, and packaging materials.
-
Design Considerations
The design of a press die set depends on several factors:- Material Type: Different materials (e.g., steel, aluminum, plastic) require different die designs to account for properties like hardness and elasticity.
- Part Geometry: The complexity of the part determines the die's design, including the number of operations and the precision required.
- Production Volume: High-volume production often requires more durable and automated die sets, while low-volume production may use simpler designs.
- Tolerance and Precision: The required level of accuracy influences the die's construction and alignment mechanisms.
-
Advantages of Using Press Die Sets
- High Precision: Ensures consistent and accurate production of parts.
- Efficiency: Enables high-speed production, reducing manufacturing time.
- Cost-Effectiveness: Reduces material waste and labor costs, especially in mass production.
- Versatility: Can be adapted for various materials and part designs.
-
Challenges and Maintenance
- Wear and Tear: High-pressure operations can cause wear on the punch and die, requiring regular maintenance or replacement.
- Alignment Issues: Misalignment can lead to defective parts, necessitating precise setup and calibration.
- Material Compatibility: The die set must be compatible with the material being processed to avoid damage or inefficiency.
By understanding the components, types, applications, and design considerations of press die sets, manufacturers can optimize their production processes and achieve high-quality results.
Summary Table:
Aspect | Details |
---|---|
Components | Punch, Die, Guide Pins & Bushings, Backing Plates |
Types | Simple, Compound, Progressive, Transfer Die Sets |
Applications | Automotive, Aerospace, Electronics, Consumer Goods |
Design Considerations | Material Type, Part Geometry, Production Volume, Tolerance & Precision |
Advantages | High Precision, Efficiency, Cost-Effectiveness, Versatility |
Challenges | Wear and Tear, Alignment Issues, Material Compatibility |
Optimize your manufacturing process with precision press die sets—contact our experts today for tailored solutions!