Press molding in ceramics is a technique where clay or granular/powdery ceramic materials are placed into a mold and compressed under pressure, often using a hydraulic press, to form a solid body with a specific geometric shape. This method is commonly used to produce items like bathroom tiles, bricks, and cement, as it allows for efficient shaping at room temperature, reducing the time and energy required compared to traditional kiln firing. The process can involve either isostatic or axial pressure application, depending on the desired outcome and material properties.
Key Points Explained:
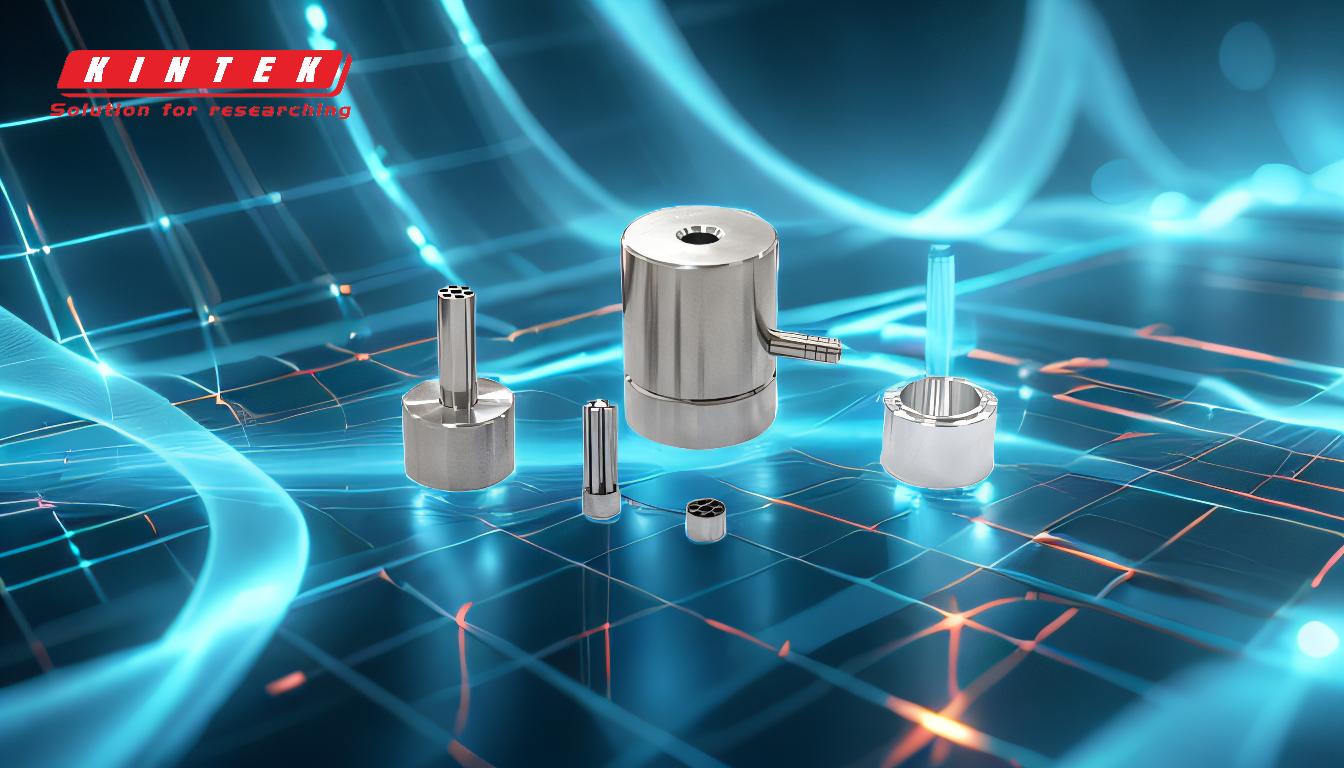
-
Definition of Press Molding in Ceramics:
- Press molding is a forming technique where clay or ceramic powders are placed into a mold and compressed under pressure to create a solid, geometrically defined shape.
- This method is widely used in the production of ceramic products like tiles, bricks, and cement.
-
Role of Hydraulic Presses:
- Hydraulic presses are essential in press molding as they generate the necessary pressure to compress the ceramic materials.
- These presses can apply either isostatic (uniform pressure from all directions) or axial (pressure from one direction) force, depending on the product requirements.
-
Advantages Over Traditional Kiln Firing:
- Press molding is performed at room temperature, eliminating the need for high-temperature kiln firing.
- This reduces production time and energy consumption, making it a more efficient process for certain ceramic products.
-
Applications of Press Molding:
- Commonly used for manufacturing bathroom tiles, bricks, and cement.
- Suitable for producing items that require precise geometric shapes and consistent quality.
-
Process Steps:
- Material Preparation: Granular or powdery ceramic materials are prepared and placed into the mold.
- Compression: The hydraulic press applies pressure to compress the material into the desired shape.
- Demolding: The formed ceramic body is removed from the mold, ready for further processing or use.
-
Types of Pressure Application:
- Isostatic Pressing: Uniform pressure is applied from all directions, ideal for complex shapes and uniform density.
- Axial Pressing: Pressure is applied from one direction, suitable for simpler shapes and high-volume production.
-
Material Considerations:
- The choice of ceramic material (granular or powdery) affects the final product's properties and the required pressure.
- Proper material preparation ensures consistency and quality in the final product.
-
Efficiency and Cost-Effectiveness:
- Press molding is faster and more energy-efficient than traditional kiln firing, making it cost-effective for large-scale production.
- The process allows for high-volume production with consistent quality, reducing waste and improving profitability.
By understanding these key points, a ceramic equipment or consumable purchaser can make informed decisions about adopting press molding techniques for their production needs. This method offers significant advantages in terms of efficiency, precision, and cost-effectiveness, making it a valuable option in the ceramics industry.
Summary Table:
Aspect | Details |
---|---|
Definition | Technique using pressure to shape clay or ceramic powders into solid forms. |
Key Equipment | Hydraulic presses for isostatic or axial pressure application. |
Advantages | Room temperature process, faster, energy-efficient, and cost-effective. |
Applications | Tiles, bricks, cement, and other precise geometric shapes. |
Process Steps | Material preparation → Compression → Demolding. |
Pressure Types | Isostatic (uniform pressure) or axial (one-directional pressure). |
Material Considerations | Granular or powdery ceramics affect properties and pressure requirements. |
Ready to enhance your ceramic production? Contact us today to learn more about press molding solutions!