A rotary furnace is a specialized heating device used in various industries for processes such as powder roasting, ceramic sintering, high-temperature experiments, and material treatment. It consists of a long, cylindrical steel body lined with refractory materials to withstand high temperatures. The furnace is inclined at a 3% to 6% angle and rotates slowly, driven by an electric motor through gears or driven rollers. This rotation ensures uniform heating and mixing of materials inside the furnace. Rotary furnaces are versatile and find applications in ceramics, metallurgy, electronics, and more, making them essential for high-temperature industrial and research processes.
Key Points Explained:
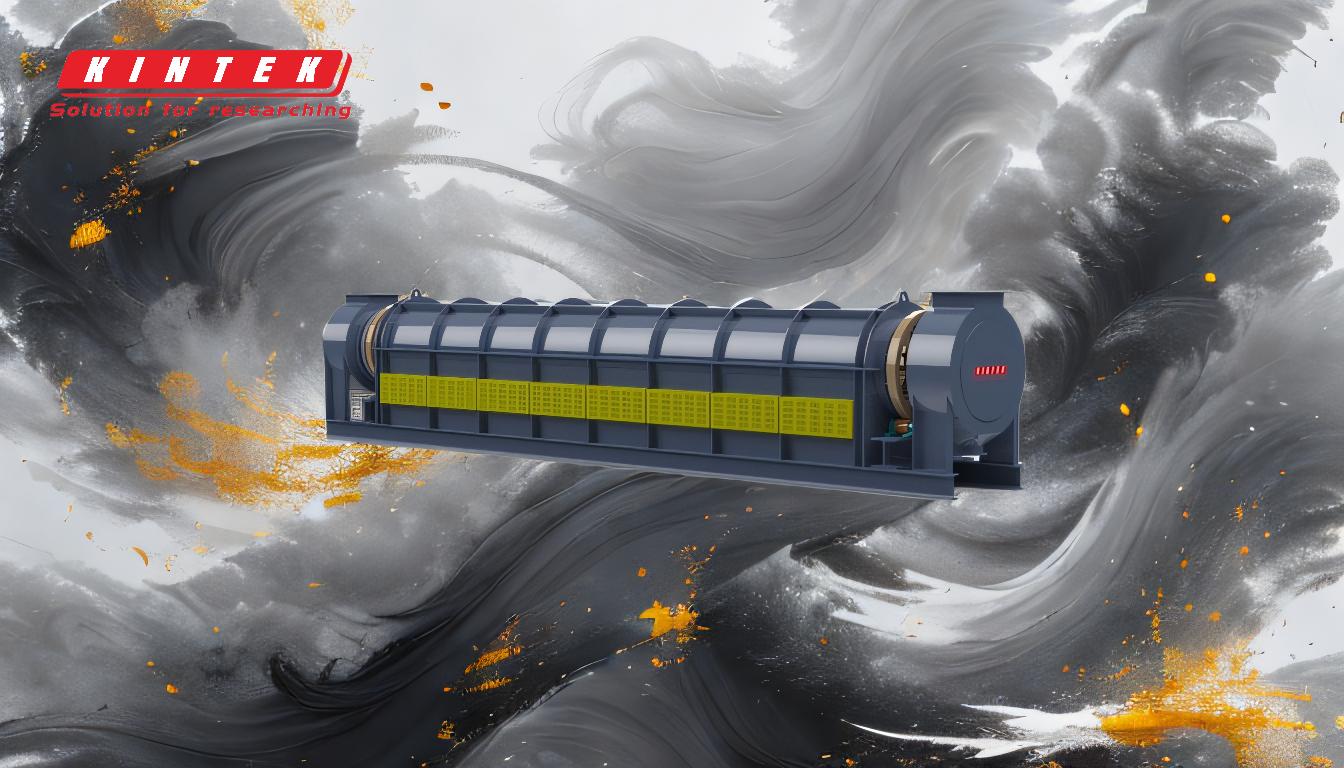
-
Structure of a Rotary Furnace:
- The furnace body is a long steel cylinder lined with refractory materials to insulate against high temperatures and prevent corrosion. The refractory lining can withstand temperatures up to 1000°C and is made from materials like bricks, cement, or moldable compounds.
- The furnace is supported on several pairs of supporting wheels and is inclined at an angle of 3% to 6%. This inclination allows materials to move from one end of the furnace to the other during rotation.
-
Rotation Mechanism:
- The furnace rotates slowly around its axis, driven by an electric motor through gears or driven rollers. This rotation ensures uniform heating and mixing of materials.
- The speed of rotation can be adjusted using a variable speed drive, and in some cases, a remote controller is used to set the furnace to rotate forward or backward.
-
Applications:
- Rotary furnaces are widely used in industries such as ceramics, metallurgy, electronics, glass, chemical industry, and machinery. They are also utilized in research institutes and universities for high-temperature experiments and material treatment.
- Specific applications include powder roasting, ceramic sintering, high-temperature atmosphere sintering, flue gas treatment, annealing, and sintering.
-
Advantages of Rotary Furnaces:
- The rotating furnace design ensures even heat distribution and thorough mixing of materials, which is crucial for processes like sintering and roasting.
- The inclination and rotation allow for continuous processing, making it efficient for industrial-scale operations.
- The refractory lining provides excellent insulation and protection, enabling the furnace to operate at extremely high temperatures.
-
Components:
- The main components of a rotary furnace include the furnace body, the refractory lining, the drive gear or rollers, and the internal heat source. These components work together to ensure efficient and reliable operation.
For more detailed information about rotary furnaces, you can explore the topic further here: rotating furnace.
Summary Table:
Aspect | Details |
---|---|
Structure | Long steel cylinder with refractory lining, inclined at 3% to 6% angle. |
Rotation Mechanism | Driven by an electric motor, adjustable speed, ensures uniform heating. |
Applications | Ceramics, metallurgy, electronics, glass, chemical industry, and research. |
Advantages | Even heat distribution, continuous processing, high-temperature operation. |
Components | Furnace body, refractory lining, drive gear/rollers, internal heat source. |
Learn more about how rotary furnaces can optimize your processes—contact our experts today!