Activated carbon is a highly effective adsorbent material derived from coal or biomass through thermochemical or hydrothermal processes, followed by physical or chemical activation to enhance its adsorption capabilities. This method is widely used in various industries for purification, filtration, and removal of contaminants from air, water, and gases. The activation process increases the surface area and porosity of the carbon, making it highly effective in trapping impurities. Below, we explore the key aspects of the activated carbon method, including its production, properties, and applications.
Key Points Explained:
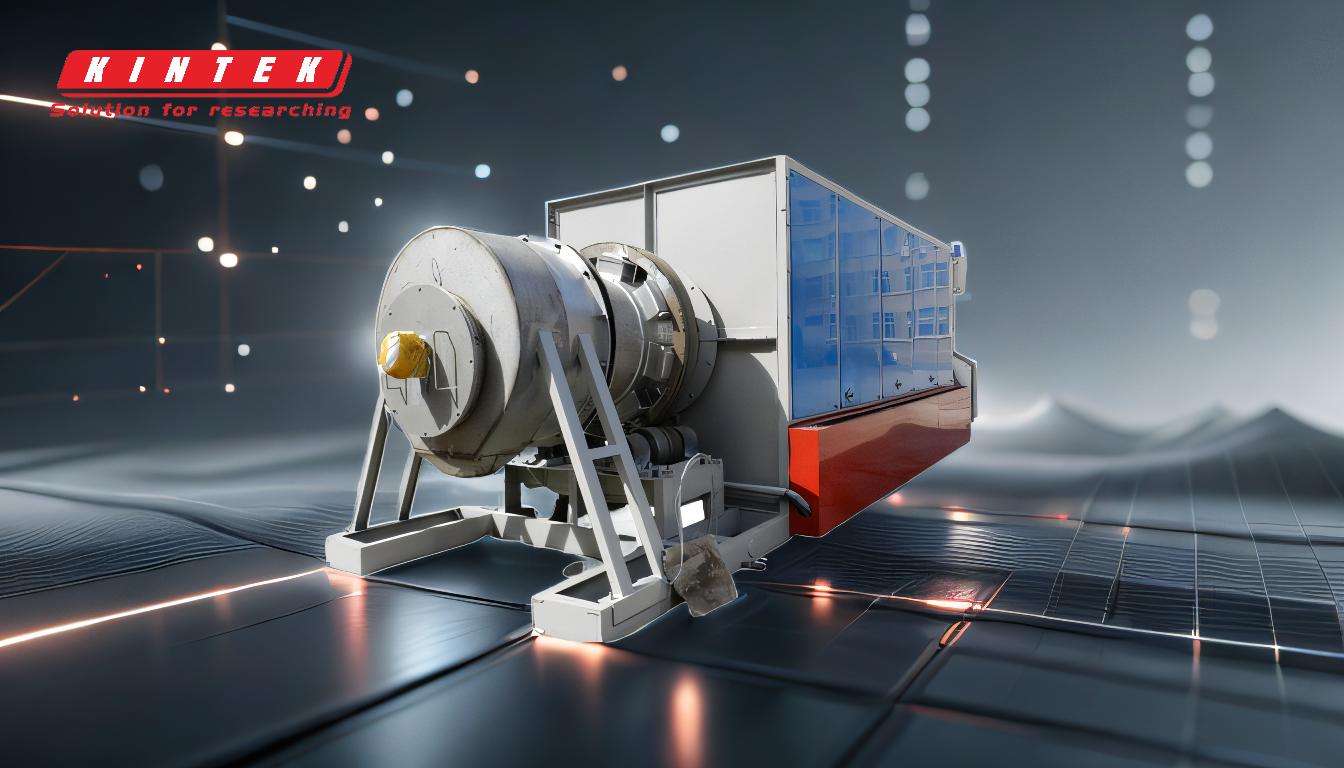
-
Definition and Origin of Activated Carbon
- Activated carbon is a porous form of carbon produced from carbon-rich materials like coal, wood, coconut shells, or other biomass.
- It undergoes a two-step process: carbonization (thermochemical decomposition) and activation (physical or chemical treatment).
-
Production Process
- Carbonization: The raw material is heated in the absence of oxygen to remove volatile components, leaving behind a carbon-rich char.
-
Activation: The char is treated with steam, carbon dioxide, or chemicals (e.g., phosphoric acid or potassium hydroxide) to create a highly porous structure.
- Physical activation uses high temperatures and gases.
- Chemical activation involves impregnating the material with chemicals before heating.
-
Properties of Activated Carbon
- High Surface Area: Activated carbon has an extensive network of pores, providing a large surface area (500–1500 m²/g) for adsorption.
- Porosity: It contains micro-, meso-, and macropores, allowing it to adsorb molecules of varying sizes.
- Adsorption Capacity: Its ability to trap contaminants depends on factors like pore size, surface chemistry, and the nature of the adsorbate.
-
Applications of Activated Carbon
- Water Treatment: Removes organic compounds, chlorine, and heavy metals from drinking water and wastewater.
- Air Purification: Captures volatile organic compounds (VOCs), odors, and pollutants in industrial and residential settings.
- Medical Uses: Used in poison treatment and drug overdose cases to adsorb toxins in the gastrointestinal tract.
- Industrial Processes: Purifies gases, recovers solvents, and removes impurities in chemical manufacturing.
-
Advantages of the Activated Carbon Method
- High adsorption efficiency for a wide range of contaminants.
- Versatility in applications across industries.
- Regenerability: Activated carbon can often be reactivated and reused, reducing waste.
-
Limitations
- Not effective for all types of contaminants (e.g., some inorganic compounds).
- Requires proper disposal or regeneration after use to avoid environmental issues.
- Cost can be high depending on the quality and application.
In summary, the activated carbon method is a versatile and efficient approach for adsorption-based purification and filtration. Its unique properties, such as high surface area and porosity, make it indispensable in environmental, industrial, and medical applications. However, its effectiveness depends on proper selection, usage, and maintenance.
Summary Table:
Aspect | Details |
---|---|
Definition | Porous carbon derived from coal or biomass, used for adsorption. |
Production Process | - Carbonization: Heating raw material without oxygen. |
- Activation: Physical (steam/gas) or chemical (acid/base) treatment. | |
Properties | - High surface area (500–1500 m²/g). |
- Micro-, meso-, and macropores for versatile adsorption. | |
Applications | - Water treatment, air purification, medical uses, industrial processes. |
Advantages | - High adsorption efficiency, versatility, and regenerability. |
Limitations | - Ineffective for some contaminants, requires proper disposal, high cost. |
Unlock the potential of activated carbon for your needs—contact our experts today!