Hot isostatic pressing (HIP) is a manufacturing process that applies high temperature and uniform pressure to materials to improve their mechanical properties, eliminate defects, and consolidate powders. This process is widely used in industries such as aerospace, automotive, and medical for applications like densification of ceramics, bonding of dissimilar metals, and healing of casting defects. A notable example of HIP is its use in aerospace to eliminate voids in castings, ensuring high-performance components with enhanced durability and reliability.
Key Points Explained:
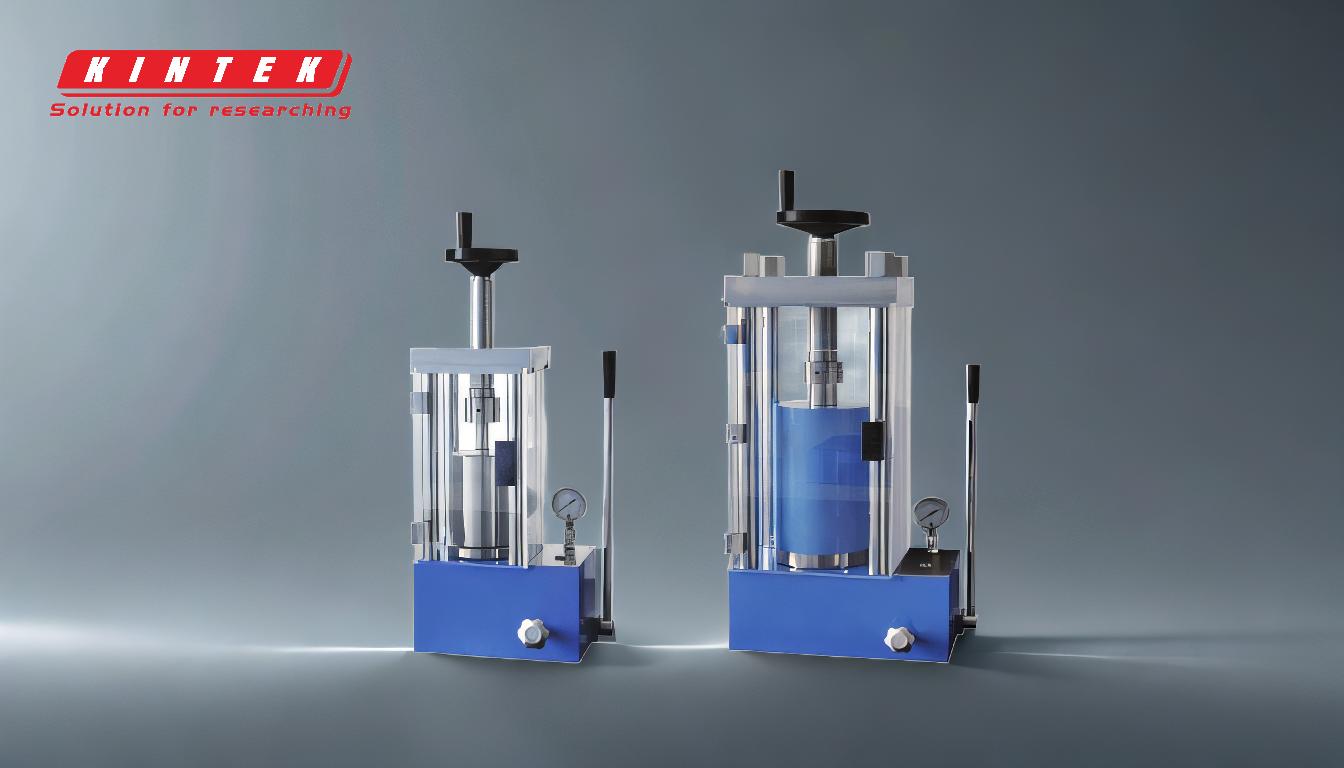
-
Definition and Purpose of Hot Isostatic Pressing (HIP):
- HIP involves subjecting materials to high temperatures (up to 2000°C) and uniform pressure (up to 200 MPa) in a controlled environment. The primary goal is to improve material properties, such as density, strength, and fatigue resistance, by eliminating voids, consolidating powders, and bonding dissimilar materials.
-
Applications of HIP:
- Aerospace Industry: HIP is used to eliminate voids and defects in critical components like turbine blades and engine parts, ensuring they meet stringent performance and safety standards.
- Medical Industry: HIP is employed to produce high-density, biocompatible materials for implants and prosthetics, such as titanium alloy hip joints.
- Automotive Industry: The process is used to manufacture high-strength components like gears and engine parts, improving their durability and performance.
- Ceramics and Composites: HIP is ideal for producing high-performance ceramics and composites, such as zirconia and alumina, which require exceptional strength and precision.
-
Types of HIP Applications:
- Densification: HIP is used to increase the density of materials, reducing porosity and improving mechanical properties. This is particularly useful for ceramics and powder metallurgy products.
- Diffusion Bonding: HIP enables the bonding of similar or dissimilar materials, creating complex components with superior structural integrity.
- Powder Metallurgy: HIP consolidates metal powders into near-net-shape components, reducing the need for extensive machining.
-
Process Techniques:
- Wet-Bag Technique: The material is placed in a flexible mold (e.g., polyurethane), submerged in a pressure vessel filled with a pressurizing fluid, and subjected to uniform pressure.
- Dry-Bag Technique: The flexible mold is fixed in the pressure vessel, and powder is loaded without removing the mold. This method is more efficient for high-volume production.
-
Advantages of HIP:
- Improved Material Properties: HIP enhances strength, fatigue resistance, and durability by eliminating defects and increasing density.
- Versatility: HIP can be applied to a wide range of materials, including metals, ceramics, composites, and plastics.
- Cost Efficiency: By reducing the need for machining and minimizing material waste, HIP can lower production costs.
-
Example of HIP in Action:
- In the aerospace industry, HIP is used to process nickel-base superalloys and titanium powders into high-performance components like turbine blades. These parts are critical for jet engines, where even minor defects can lead to catastrophic failures. HIP ensures these components are free of voids and have exceptional mechanical properties, making them reliable under extreme conditions.
By leveraging the capabilities of hot isostatic pressing, industries can produce high-quality, defect-free components that meet the demanding requirements of modern applications. This process is a cornerstone of advanced manufacturing, enabling innovation and reliability in critical sectors.
Summary Table:
Aspect | Details |
---|---|
Definition | HIP applies high temperature (up to 2000°C) and uniform pressure (up to 200 MPa) to improve material properties. |
Key Applications | - Aerospace: Eliminates voids in turbine blades and engine parts. |
- Medical: Produces biocompatible implants like titanium hip joints. | |
- Automotive: Manufactures high-strength gears and engine parts. | |
Process Techniques | - Wet-Bag: Flexible mold submerged in pressurizing fluid. |
- Dry-Bag: Fixed mold for high-volume production. | |
Advantages | - Improves strength, fatigue resistance, and durability. |
- Versatile for metals, ceramics, composites, and plastics. | |
- Cost-efficient by reducing machining and material waste. |
Interested in how hot isostatic pressing can elevate your manufacturing process? Contact us today to learn more!