An industrial heating element is a component designed to convert electrical energy into heat through the process of resistive heating. These elements are constructed from materials that can withstand high temperatures and are used in a wide range of industrial applications, including furnaces, dryers, and specialized heating systems. The materials used in heating elements vary depending on the application and temperature requirements, with common choices including metallic alloys like nickel-chromium, molybdenum, and tungsten, as well as non-metallic materials such as graphite and silicon carbide. Industrial heating elements are available in various forms, including wire, ribbon, tubular, and strip configurations, and are tailored to meet specific operational needs, such as high-temperature vacuum furnaces or snow-melting systems.
Key Points Explained:
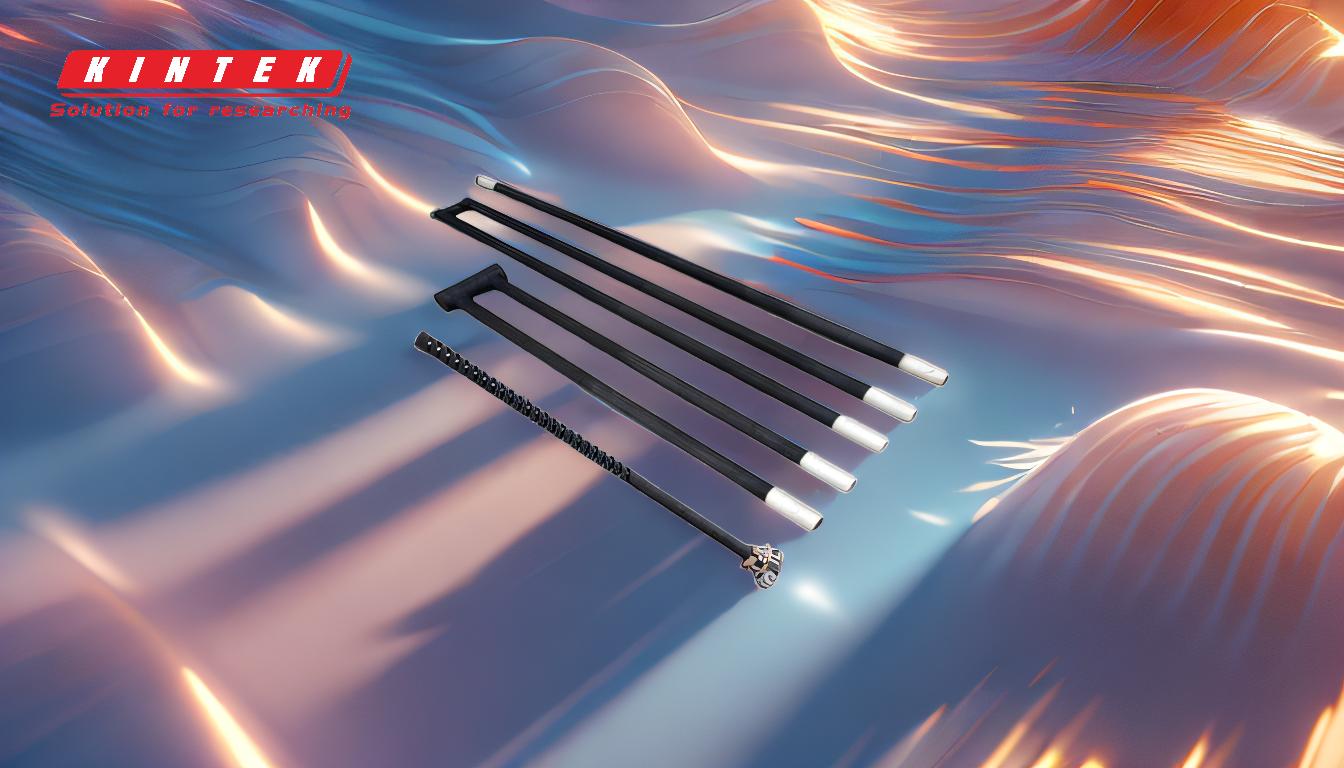
-
Definition and Function of Industrial Heating Elements
- Industrial heating elements are devices that convert electrical energy into heat through resistive heating.
- They are used in a variety of industrial applications, such as furnaces, dryers, and specialized heating systems like roof or pathway heating.
- The primary function is to provide controlled and efficient heat generation for industrial processes.
-
Materials Used in Heating Elements
-
Metallic Materials:
- Common metallic materials include nickel-chromium alloys, stainless steel, molybdenum, tungsten, and tantalum.
- These materials are chosen for their high melting points, resistance to oxidation, and durability under high temperatures.
-
Non-Metallic Materials:
- Non-metallic options include graphite, silicon carbide, and molybdenum dioxide.
- These materials are often used in high-temperature applications due to their thermal stability and resistance to chemical reactions.
-
Metallic Materials:
-
Types of Heating Elements
-
Resistance Wire or Ribbon:
- Made from metallic alloys, these elements can be straight or coiled and are used in devices like toasters, hair dryers, and industrial furnaces.
-
Tubular Electric Heaters:
- These are cylindrical heating elements often used in industrial processes requiring uniform heat distribution.
-
Graphite or Molybdenum Strips:
- Lightweight and curved, these elements are ideal for high-temperature vacuum furnaces and other specialized applications.
-
Resistance Wire or Ribbon:
-
Applications of Industrial Heating Elements
-
Industrial Furnaces:
- Heating elements are critical in furnaces for processes like melting, annealing, and heat treatment. Materials like tungsten and silicon carbide are often used for their ability to withstand extreme temperatures.
-
Snow and Ice Melting Systems:
- Heating elements are embedded in pathways, roofs, or driveways to melt snow and ice, ensuring safety and accessibility.
-
Dryers and Heaters:
- Used in industrial dryers for materials like textiles, food, or chemicals, as well as in space heaters for large facilities.
-
Industrial Furnaces:
-
Design and Configuration
- Heating elements are designed in various shapes and configurations to suit specific applications:
- Cylindrical or Semi-Circular: Common in industrial furnaces for even heat distribution.
- Flat Panels: Used in applications like floor heating or large surface heating systems.
- Coiled or Straight Wire: Ideal for compact devices like toasters or hair dryers.
- Heating elements are designed in various shapes and configurations to suit specific applications:
-
High-Temperature Applications
- For extreme temperatures (above 1200°C), heating elements are made from exotic materials such as:
- Platinum, tungsten disilicide, and molybdenum disilicide.
- These materials are chosen for their ability to maintain structural integrity and performance under harsh conditions.
- For extreme temperatures (above 1200°C), heating elements are made from exotic materials such as:
-
Customization and Selection Criteria
- When selecting a heating element, factors to consider include:
- Operating temperature range.
- Material compatibility with the environment (e.g., resistance to corrosion or oxidation).
- Physical configuration and size to fit the application.
- Electrical resistance and power requirements.
- When selecting a heating element, factors to consider include:
-
Advantages of Industrial Heating Elements
- Efficiency: Converts electrical energy into heat with minimal losses.
- Durability: Made from materials that can withstand high temperatures and harsh environments.
- Versatility: Available in various forms and materials to suit diverse industrial needs.
- Precision: Provides controlled and consistent heating for critical processes.
By understanding the materials, types, and applications of industrial heating elements, purchasers can make informed decisions to select the most suitable components for their specific requirements.
Summary Table:
Aspect | Details |
---|---|
Function | Converts electrical energy into heat through resistive heating. |
Materials | Metallic (e.g., nickel-chromium, tungsten) and non-metallic (e.g., graphite, silicon carbide). |
Types | Resistance wire, tubular heaters, graphite/molybdenum strips. |
Applications | Industrial furnaces, snow-melting systems, dryers, and heaters. |
Design | Cylindrical, flat panels, coiled/straight wire for specific needs. |
High-Temperature Use | Exotic materials like platinum and tungsten disilicide for >1200°C. |
Advantages | Efficiency, durability, versatility, and precision in heat control. |
Need the right heating element for your industrial application? Contact us today for expert guidance!