Basic lining materials are refractory materials used in high-temperature industrial applications, such as furnaces, kilns, and reactors, to provide thermal insulation, resist corrosion, and withstand thermal shock. These materials are typically composed of alkaline compounds like magnesia (MgO) or dolomite (CaO·MgO), which offer excellent resistance to basic slags and high-temperature environments. They are designed to ensure durability, ease of installation, and maintenance while minimizing heat loss and protecting the structural integrity of the equipment.
Key Points Explained:
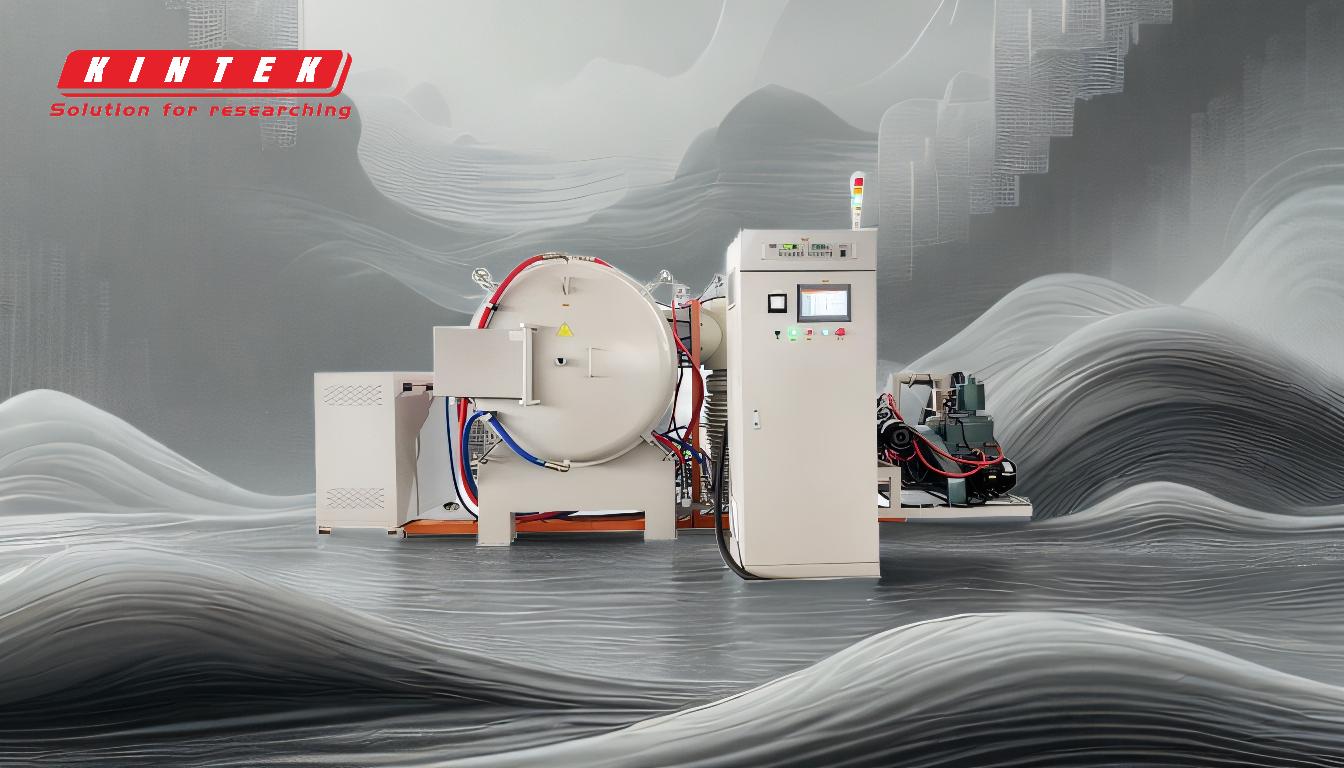
-
Definition and Composition of Basic Lining Materials
- Basic lining materials are refractory materials composed primarily of alkaline compounds such as magnesia (MgO) or dolomite (CaO·MgO).
- These materials are chosen for their ability to withstand high temperatures and resist chemical reactions with basic slags, making them ideal for environments like steelmaking furnaces.
-
Key Properties of Basic Lining Materials
- Low Thermal Conductivity: Ensures effective thermal insulation, reducing heat loss and improving energy efficiency.
- Resistance to Corrosion: Protects the lining from chemical attack by basic slags and other corrosive substances.
- Thermal Shock Resistance: Allows the material to withstand rapid temperature changes without cracking or failing.
- Ease of Installation and Maintenance: Simplifies the process of applying and repairing the lining, reducing downtime and operational costs.
-
Applications of Basic Lining Materials
- Commonly used in high-temperature industrial processes, such as steelmaking, cement production, and glass manufacturing.
- Suitable for furnaces, kilns, and reactors where exposure to basic slags and extreme temperatures is prevalent.
-
Advantages of Basic Lining Materials
- Durability: Long-lasting performance in harsh environments.
- Energy Efficiency: Reduces heat loss, leading to lower energy consumption.
- Cost-Effectiveness: Minimizes the need for frequent repairs and replacements.
-
Considerations for Selection
- The specific application and operating conditions (e.g., temperature, chemical exposure) should guide the choice of basic lining material.
- Factors like installation complexity, maintenance requirements, and cost should also be evaluated.
In summary, basic lining materials are essential for high-temperature industrial applications, offering a combination of durability, resistance to corrosion and thermal shock, and ease of use. Their selection and application should be tailored to the specific needs of the process to ensure optimal performance and cost-effectiveness.
Summary Table:
Key Aspect | Details |
---|---|
Composition | Alkaline compounds like magnesia (MgO) or dolomite (CaO·MgO). |
Key Properties | Low thermal conductivity, corrosion resistance, thermal shock resistance. |
Applications | Steelmaking, cement production, glass manufacturing. |
Advantages | Durability, energy efficiency, cost-effectiveness. |
Selection Considerations | Temperature, chemical exposure, installation complexity, maintenance needs. |
Need the right basic lining material for your high-temperature application? Contact our experts today for tailored solutions!