A channel induction furnace is a type of induction furnace used primarily for melting and holding metals, particularly in foundries and metalworking industries. It operates on the principle of electromagnetic induction, where an alternating current passes through a coil, generating a magnetic field that induces eddy currents in the metal, causing it to heat up and melt. The furnace features a unique design with a refractory-lined channel that contains the molten metal, allowing for continuous operation and efficient energy use. Channel induction furnaces are known for their high efficiency, precise temperature control, and ability to maintain a consistent melt pool, making them ideal for applications requiring long-term metal holding or continuous casting processes.
Key Points Explained:
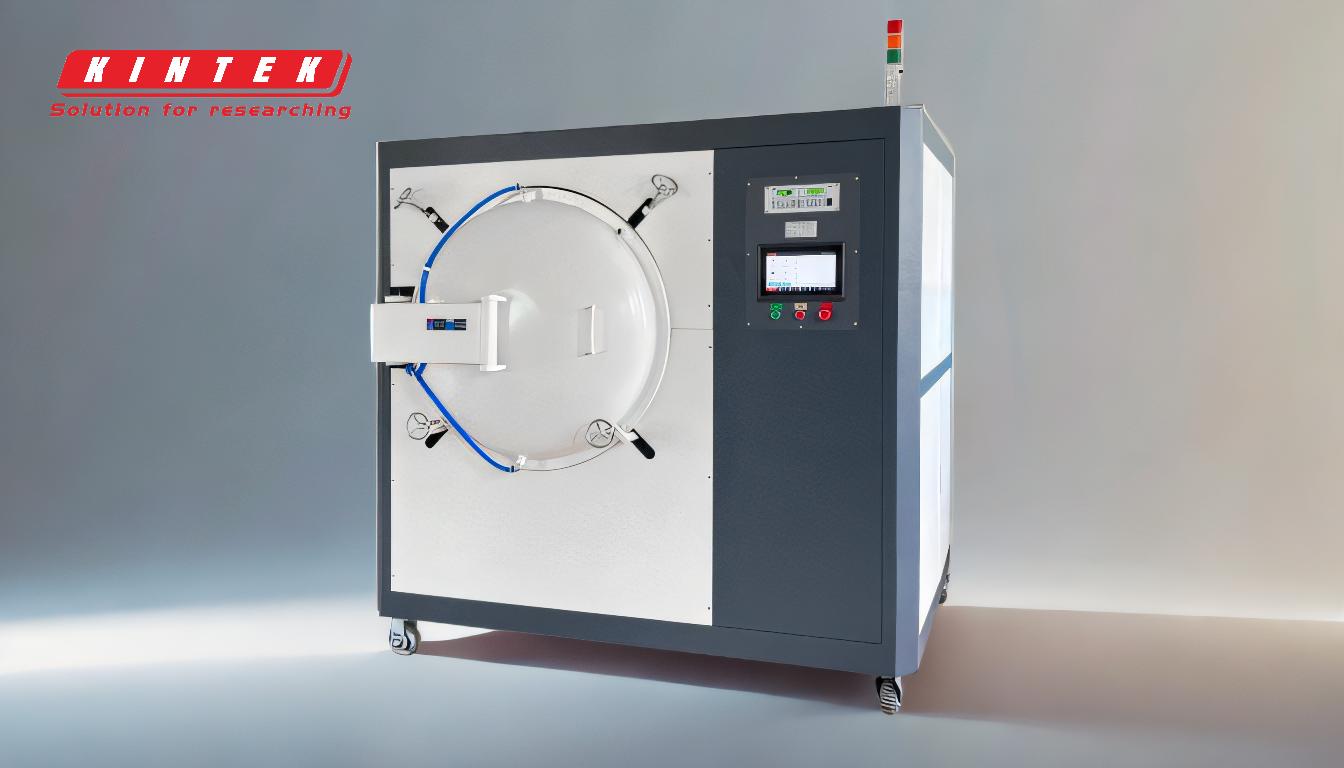
-
Basic Working Principle:
- A channel induction furnace operates on electromagnetic induction. An alternating current flows through a coil, creating a magnetic field that induces eddy currents in the metal. These currents generate heat, melting the metal.
- The design includes a refractory-lined channel that holds the molten metal, ensuring continuous operation and efficient heat transfer.
-
Core Components:
- Induction Coil: The primary component that generates the magnetic field. It is typically made of copper and is water-cooled to prevent overheating.
- Refractory Lining: Protects the furnace structure from high temperatures and chemical reactions with molten metal.
- Channel: A loop-shaped passage that contains the molten metal, allowing for continuous circulation and heating.
-
Advantages of Channel Induction Furnaces:
- High Efficiency: The design minimizes heat loss, making it energy-efficient compared to other furnace types.
- Precise Temperature Control: Enables consistent and accurate control of the metal's temperature, which is crucial for quality in casting and metalworking.
- Continuous Operation: The channel design allows for uninterrupted melting and holding of metal, ideal for foundries with high production demands.
- Low Maintenance: The robust design and fewer moving parts reduce maintenance requirements and downtime.
-
Applications:
- Foundries: Used for melting and holding metals like iron, steel, aluminum, and copper alloys.
- Continuous Casting: Ideal for processes requiring a steady supply of molten metal.
- Metal Recycling: Efficiently melts scrap metal for reuse in manufacturing.
-
Comparison with Other Furnaces:
- Unlike igbt induction furnace, which uses insulated gate bipolar transistors for power control, channel induction furnaces rely on traditional induction principles. They are better suited for long-term metal holding and continuous processes, whereas IGBT furnaces are more versatile for rapid heating and smaller-scale operations.
-
Considerations for Purchasers:
- Energy Efficiency: Evaluate the furnace's energy consumption and heat retention capabilities.
- Capacity: Ensure the furnace meets the required melt volume and production rate.
- Refractory Life: Check the durability of the refractory lining, as frequent replacements can increase operational costs.
- Maintenance Requirements: Consider the ease of maintenance and availability of spare parts.
By understanding these key points, purchasers can make informed decisions when selecting a channel induction furnace for their specific needs.
Summary Table:
Aspect | Details |
---|---|
Working Principle | Electromagnetic induction heats metal via eddy currents in a refractory-lined channel. |
Core Components | Induction coil, refractory lining, and a loop-shaped channel for molten metal. |
Advantages | High efficiency, precise temperature control, continuous operation, low maintenance. |
Applications | Foundries, continuous casting, metal recycling. |
Key Considerations | Energy efficiency, capacity, refractory life, and maintenance requirements. |
Ready to enhance your metalworking process? Contact us today to find the perfect channel induction furnace!