An induction furnace is a type of electrical furnace used for heating metals through induction heating. It operates by generating a rapidly alternating magnetic field using a copper coil, which induces eddy currents in the metal, causing it to heat up due to Joule heating. In ferromagnetic materials like iron, additional heating occurs due to magnetic hysteresis. The furnace typically consists of a nonconductive crucible that holds the metal charge, surrounded by the induction coil. This method of heating is efficient and widely used in various industrial applications.
Key Points Explained:
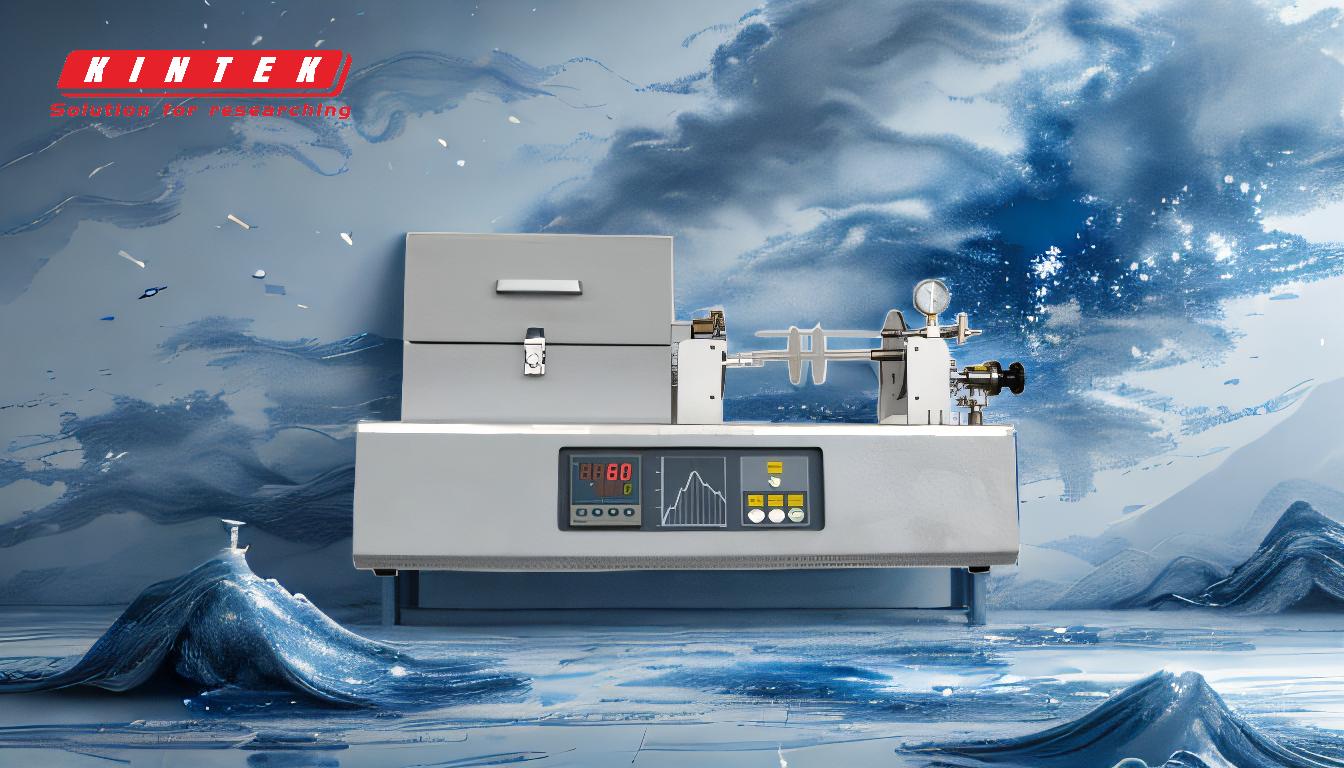
-
Basic Principle of Induction Heating:
- Induction heating works by generating a rapidly alternating magnetic field using a copper coil.
- This magnetic field induces eddy currents within the metal, which generate heat through Joule heating.
- In ferromagnetic materials, additional heat is produced due to magnetic hysteresis.
-
Components of an Induction Furnace:
- Nonconductive Crucible: Holds the metal charge and is typically made from materials that do not conduct electricity.
- Copper Coil: Surrounds the crucible and carries the alternating current that generates the magnetic field.
- Power Supply: Provides the alternating current necessary for induction heating.
-
Types of Induction Furnaces:
- Channel Type Induction Furnace: This type of furnace has a channel-like structure where the metal is heated. It is particularly useful for continuous melting processes.
- Coreless Induction Furnace: Does not have a core and is used for batch melting processes.
-
Advantages of Induction Furnaces:
- Efficiency: Induction furnaces are highly efficient as they directly heat the metal without intermediate steps.
- Precision: They allow for precise control over temperature and heating rates.
- Cleanliness: Since there is no combustion, the process is clean and produces fewer emissions.
-
Applications:
- Metal Melting: Widely used in foundries for melting metals like iron, steel, and non-ferrous metals.
- Heat Treatment: Used for processes like annealing, hardening, and tempering.
- Semiconductor Manufacturing: Utilized in the production of semiconductors and other high-purity materials.
-
IGBT Induction Furnace:
- Modern induction furnaces often use Insulated Gate Bipolar Transistors (IGBTs) for better control and efficiency. IGBTs allow for precise control of the power supply, leading to improved performance and energy savings. For more details on IGBT induction furnaces, you can visit igbt induction furnace.
In summary, induction furnaces, including the channel type, are essential tools in modern metallurgy and material processing, offering high efficiency, precision, and cleanliness. The use of advanced technologies like IGBTs further enhances their performance, making them indispensable in various industrial applications.
Summary Table:
Aspect | Details |
---|---|
Basic Principle | Uses induction heating with a copper coil to generate eddy currents in metal. |
Key Components | Nonconductive crucible, copper coil, and power supply. |
Advantages | High efficiency, precise temperature control, and clean operation. |
Applications | Metal melting, heat treatment, and semiconductor manufacturing. |
IGBT Technology | Enhances control and energy efficiency in modern induction furnaces. |
Discover how a channel type induction furnace can optimize your industrial processes—contact us today!