Thermoforming is a cost-effective alternative to injection molding, particularly for lower-volume production runs. The primary reason for its affordability lies in the significantly lower tooling costs. Thermoforming molds are typically made from less expensive materials like alumina ceramic, which are easier and cheaper to manufacture compared to the hardened steel molds required for injection molding. Additionally, the simpler design and production process of thermoforming molds reduce both initial investment and lead times, making it a more economical choice for certain applications.
Key Points Explained:
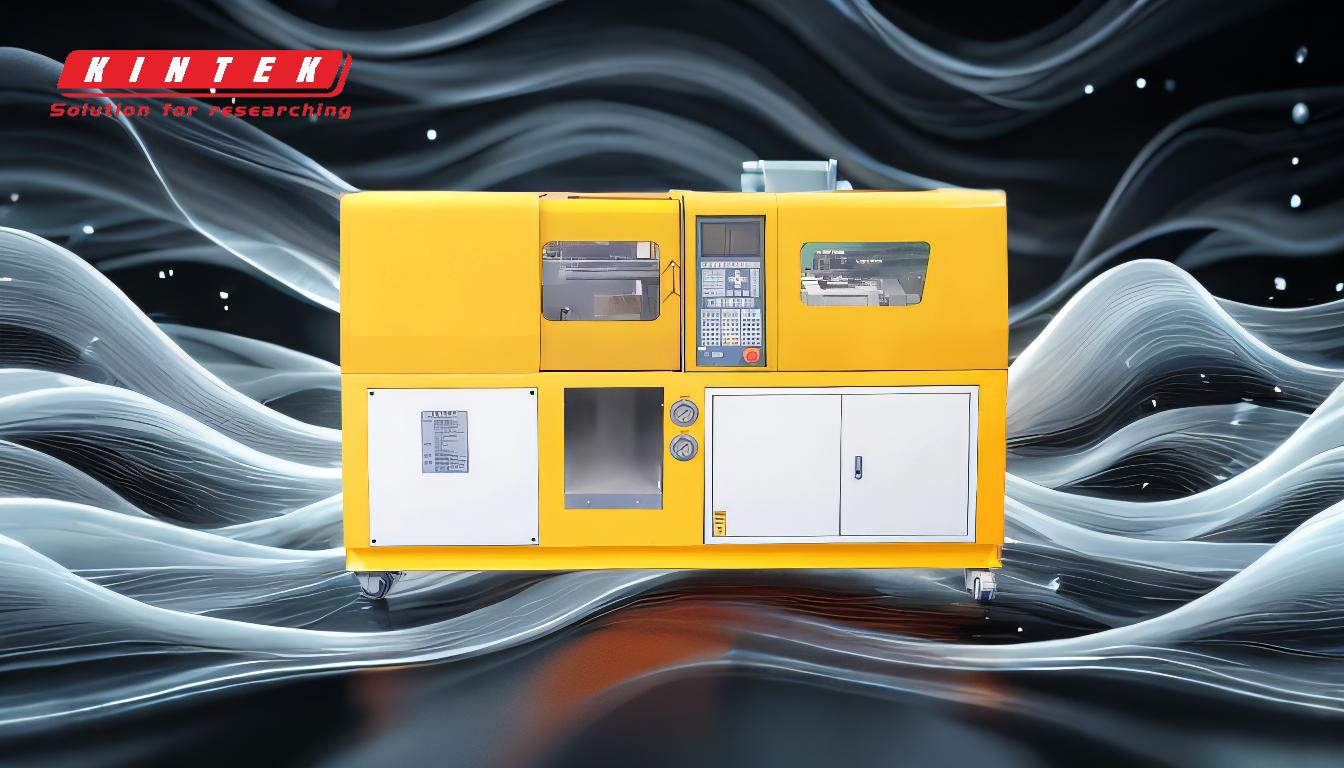
-
Lower Tooling Costs:
- Material Cost: Thermoforming molds are often made from aluminum, which is less expensive than the hardened steel used in injection molding. Aluminum is easier to machine and requires less time and labor to produce, further reducing costs.
- Design Complexity: Thermoforming molds are generally simpler in design compared to injection molding molds. This simplicity translates to lower design and manufacturing costs.
-
Reduced Initial Investment:
- Mold Production Time: The time required to produce a thermoforming mold is significantly shorter than that for an injection molding mold. This quicker turnaround can lead to cost savings, especially for projects with tight deadlines.
- Setup Costs: The initial setup for thermoforming is less complex and less expensive. This includes the cost of machinery, which is generally lower for thermoforming equipment compared to injection molding machines.
-
Economical for Lower-Volume Production:
- Volume Flexibility: Thermoforming is particularly cost-effective for lower-volume production runs. The lower initial investment in tooling makes it a viable option for companies that do not require high-volume production.
- Prototyping: For prototyping or short-run production, thermoforming offers a more economical solution. The ability to quickly and inexpensively produce molds allows for faster iteration and testing of designs.
-
Material Efficiency:
- Waste Reduction: Thermoforming can be more material-efficient, especially for larger parts. The process often produces less scrap material compared to injection molding, leading to cost savings on raw materials.
- Thinner Walls: Thermoformed parts can often be made with thinner walls, which reduces material usage without compromising on strength or functionality.
-
Operational Costs:
- Energy Consumption: Thermoforming generally requires less energy compared to injection molding. The lower energy consumption contributes to overall cost savings, especially in large-scale operations.
- Maintenance: The maintenance costs for thermoforming equipment are typically lower. The simpler machinery and less wear and tear on molds result in reduced maintenance expenses over time.
In summary, thermoforming offers a more economical alternative to injection molding, particularly for lower-volume production, prototyping, and applications where material efficiency and reduced initial investment are critical. The lower tooling costs, simpler design, and faster production times make thermoforming a cost-effective choice for many manufacturers.
Summary Table:
Aspect | Thermoforming | Injection Molding |
---|---|---|
Tooling Costs | Lower (aluminum molds) | Higher (hardened steel molds) |
Initial Investment | Reduced (simpler setup, cheaper machinery) | Higher (complex setup, expensive machinery) |
Production Time | Faster (shorter mold production time) | Slower (longer mold production time) |
Volume Suitability | Ideal for lower-volume production and prototyping | Better for high-volume production |
Material Efficiency | Higher (less waste, thinner walls) | Lower (more waste, thicker walls) |
Operational Costs | Lower (less energy consumption, reduced maintenance) | Higher (more energy consumption, higher maintenance) |
Interested in cost-effective thermoforming solutions? Contact us today to learn more!