Chemical vapor deposition (CVD) of diamond is a sophisticated process used to create synthetic diamonds by depositing carbon atoms onto a substrate in a controlled environment. This method involves the use of gas precursors, typically methane and hydrogen, which are activated using energy sources like microwaves or hot filaments. The activated gases form carbon radicals that deposit onto a substrate, layer by layer, to form a diamond structure. This technique is widely used for creating high-quality diamond coatings and single crystals, which are essential in various industrial applications, including cutting tools and optical components like CVD diamond domes.
Key Points Explained:
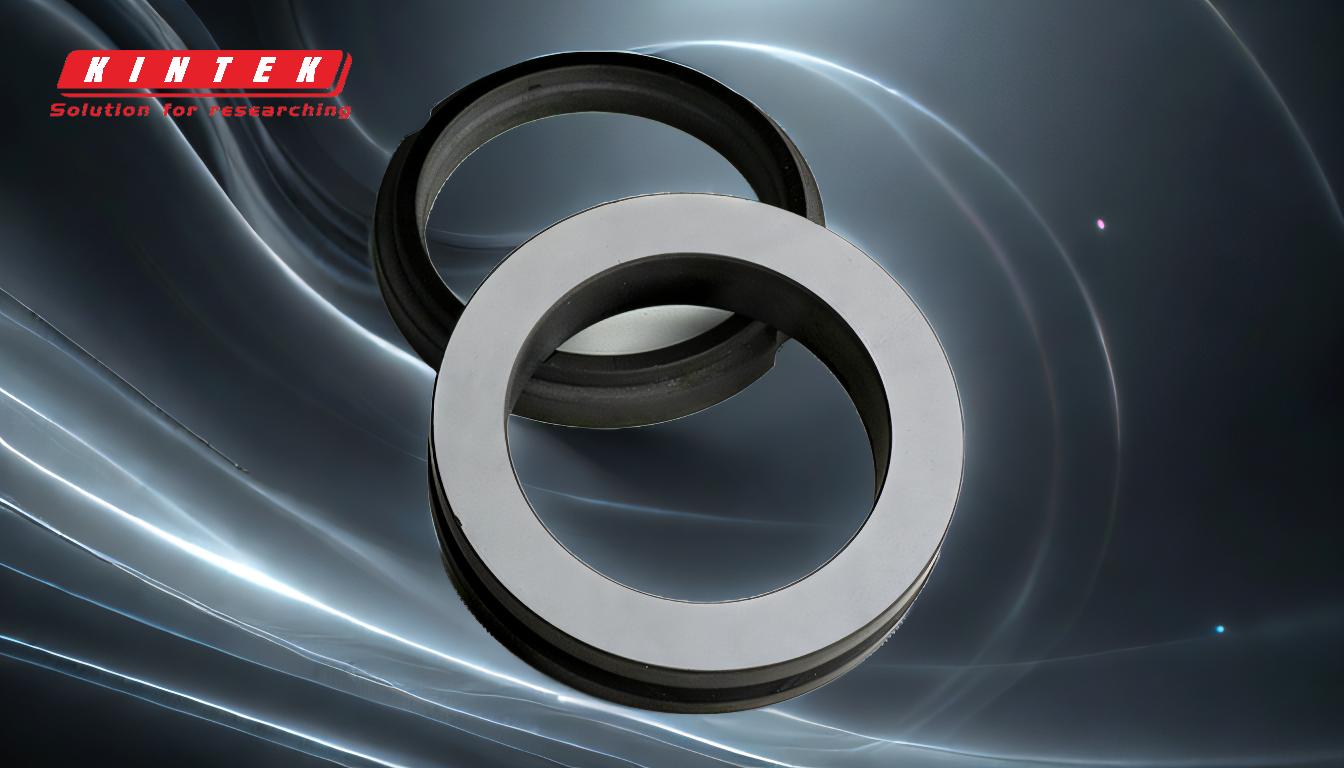
-
Process Overview:
- CVD involves feeding a mixture of gases, such as methane and hydrogen, into a chamber under low pressure.
- These gases are activated using energy sources like microwaves, hot filaments, or lasers, breaking them into chemically active radicals.
- The activated carbon radicals then deposit onto a substrate, forming a diamond layer.
-
Steps in the CVD Process:
- Transport of Gaseous Species: The reacting gases are transported to the surface of the substrate.
- Adsorption: The gaseous species adsorb onto the substrate surface.
- Surface Reactions: Heterogeneous surface-catalyzed reactions occur, leading to the formation of carbon radicals.
- Surface Diffusion: The carbon radicals diffuse across the surface to growth sites.
- Nucleation and Growth: Nucleation occurs, followed by the growth of the diamond film.
- Desorption: Gaseous reaction products desorb from the surface and are transported away.
-
Types of CVD Methods:
- Chemical Transport Method: Involves the transport of a volatile compound of the substance to be deposited.
- Pyrolysis Method: Involves the thermal decomposition of the vapor into atoms and molecules.
- Synthesis Reaction Method: Involves chemical reactions of the vapor with other substances to form the desired coating.
-
Applications of CVD Diamond:
- Coatings: CVD is used to coat cutting tools with diamond films, enhancing their durability and performance.
- Single Crystals: The process can produce single crystals several millimeters in size, which are used in high-precision applications.
- Optical Components: CVD diamond is used to fabricate optical components like CVD diamond domes, which are essential in various optical systems.
-
Advantages of CVD Diamond:
- High Quality: CVD diamonds are of high quality, with properties similar to natural diamonds.
- Versatility: The process can be used to create a wide range of diamond products, from coatings to single crystals.
- Precision: The layer-by-layer growth allows for precise control over the thickness and properties of the diamond film.
-
Challenges and Considerations:
- Complexity: The CVD process is complex and requires precise control over various parameters, such as gas composition, pressure, and temperature.
- Cost: The equipment and energy required for CVD can be expensive, making the process cost-intensive.
- Substrate Preparation: The substrate must be carefully prepared to ensure proper adhesion and growth of the diamond film.
In summary, chemical vapor deposition of diamond is a highly controlled and versatile process used to create synthetic diamonds with applications ranging from industrial coatings to optical components. The process involves several intricate steps and requires precise control over various parameters to achieve high-quality diamond films. Despite its complexity and cost, CVD diamond offers significant advantages in terms of quality and precision, making it a valuable technique in various fields.
Summary Table:
Aspect | Details |
---|---|
Process Overview | Uses methane and hydrogen gases activated by microwaves or filaments. |
Steps | Transport, adsorption, surface reactions, diffusion, nucleation, desorption. |
CVD Methods | Chemical transport, pyrolysis, synthesis reaction. |
Applications | Coatings, single crystals, optical components like CVD diamond domes. |
Advantages | High quality, versatility, precision. |
Challenges | Complexity, cost, substrate preparation. |
Discover how CVD diamond can enhance your applications—contact our experts today!