The Chemical Vapor Deposition (CVD) method is a widely used technique for synthesizing carbon nanotubes (CNTs). It involves the decomposition of gaseous precursors on a substrate, often catalyzed by metal nanoparticles, to form CNTs. The process is highly controllable, cost-effective, and scalable, making it the mainstream method for CNT synthesis. Key steps include the transport of gaseous species to the substrate, adsorption, surface-catalyzed reactions, nucleation, and growth of CNTs, followed by desorption of by-products. The method is also associated with environmental considerations, as material and energy consumption, as well as greenhouse gas emissions, must be minimized to reduce ecotoxicity impacts.
Key Points Explained:
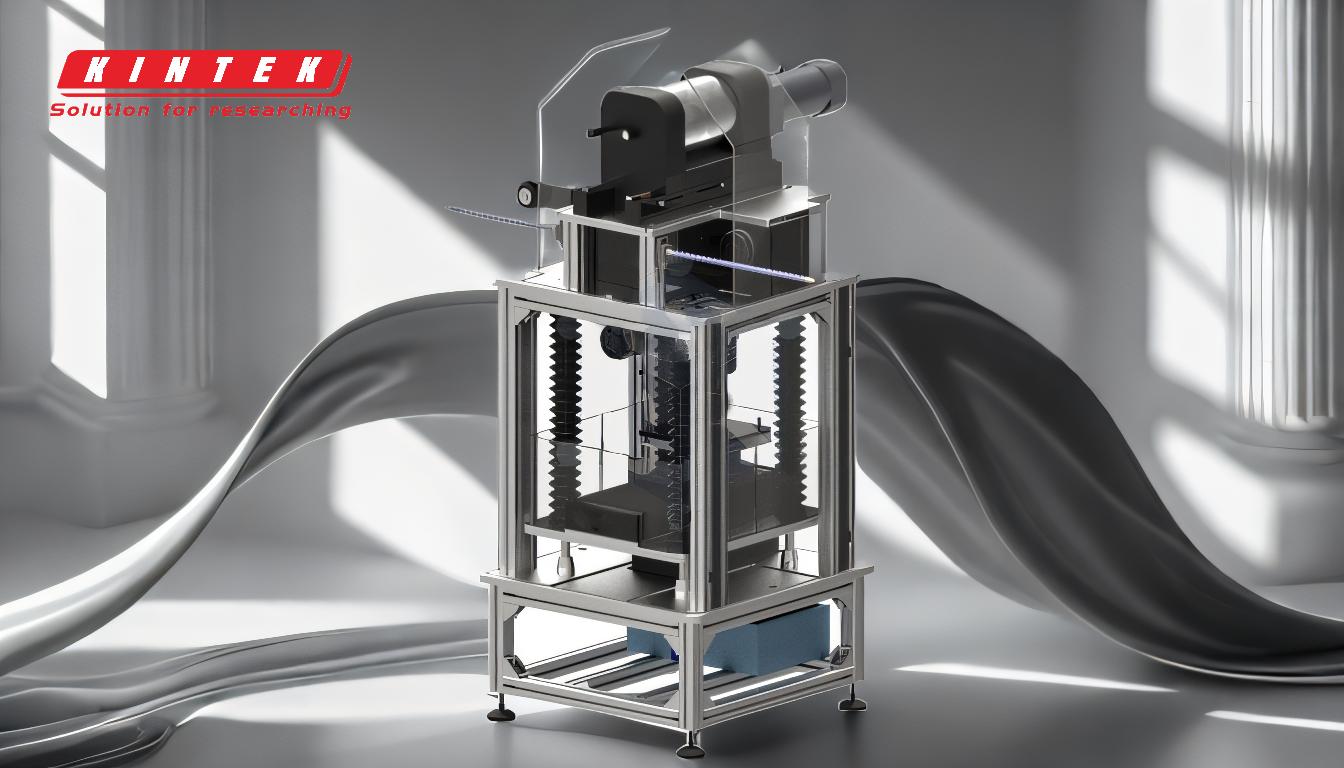
-
Overview of CVD for CNT Synthesis:
- Chemical Vapor Deposition (CVD) is a process where gaseous precursors are decomposed on a substrate to form carbon nanotubes (CNTs).
- The method is highly controllable, allowing for precise manipulation of CNT structure and properties.
- It is cost-effective and scalable, making it suitable for industrial applications.
-
Steps Involved in CVD Process:
- Transport of Gaseous Species: The gaseous precursors are transported to the substrate surface.
- Adsorption: The gaseous species adsorb onto the substrate surface.
- Surface-Catalyzed Reactions: Heterogeneous reactions occur on the substrate surface, often catalyzed by metal nanoparticles.
- Nucleation and Growth: CNTs nucleate and grow on the substrate surface.
- Desorption and Transport of By-products: Gaseous by-products are desorbed and transported away from the substrate.
-
Catalytic Chemical Vapor Deposition (CCVD):
- CCVD is a variant of CVD that uses metal catalysts (e.g., iron, nickel, or cobalt) to facilitate the growth of CNTs.
- The catalysts help in controlling the diameter, length, and chirality of the CNTs.
- CCVD is the mainstream method due to its structural controllability and cost-effectiveness.
-
Environmental Considerations:
- The synthesis process is a major contributor to the potential ecotoxicity of CNTs.
- Material consumption, energy use, and greenhouse gas emissions must be minimized to reduce the environmental impact.
- Life cycle assessment (LCA) is often used to evaluate and optimize the environmental performance of CNT synthesis.
-
Thermal Treatments and Gas-Phase Rearrangement:
- Thermal treatments are essential in the CVD process to achieve the necessary gas-phase rearrangement and catalyst deposition.
- These treatments ensure the proper decomposition of precursors and the formation of high-quality CNTs.
-
Applications and Advantages:
- CVD-synthesized CNTs are used in various applications, including electronics, composites, and energy storage.
- The method allows for the production of CNTs with specific properties tailored to the intended application.
-
Future Directions:
- Research is ongoing to further optimize the CVD process, particularly in terms of reducing environmental impact and improving the quality and yield of CNTs.
- Advances in catalyst design and process control are expected to enhance the scalability and cost-effectiveness of CNT synthesis.
By understanding these key points, one can appreciate the complexity and importance of the CVD method in the synthesis of carbon nanotubes, as well as the need for continuous improvement to address environmental and economic challenges.
Summary Table:
Key Aspect | Details |
---|---|
Process Overview | Decomposition of gaseous precursors on a substrate to form CNTs. |
Key Steps | Transport, adsorption, surface-catalyzed reactions, nucleation, growth, desorption. |
Catalytic CVD (CCVD) | Uses metal catalysts (e.g., iron, nickel) for controlled CNT growth. |
Environmental Impact | Material/energy consumption and emissions must be minimized. |
Applications | Electronics, composites, energy storage, and more. |
Future Directions | Optimizing environmental impact, improving quality, and scalability. |
Discover how CVD can revolutionize your CNT synthesis—contact our experts today for tailored solutions!