The most common heat treatment process used to increase the hardness of a metal is quenching. Quenching involves heating the metal to a high temperature and then rapidly cooling it, typically in water, oil, or air. This rapid cooling locks the metal's microstructure into a harder state, significantly increasing its hardness. Quenching is widely used in industries where hardness and wear resistance are critical, such as in the manufacturing of tools, gears, and automotive components. While other processes like case hardening and tempering also enhance hardness, quenching is the most direct and widely applied method for achieving high hardness levels in metals.
Key Points Explained:
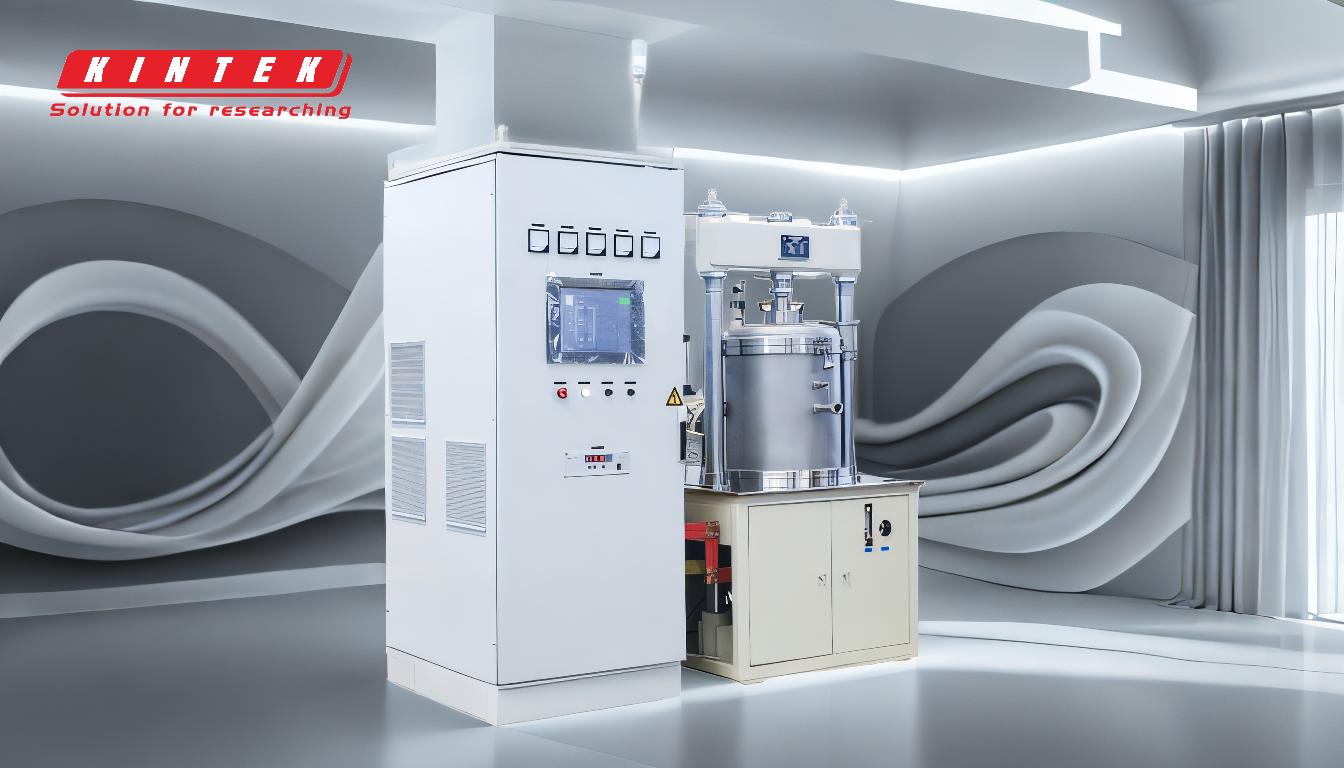
-
Definition of Quenching:
- Quenching is a heat treatment process where a metal is heated to a specific temperature (often above its critical transformation temperature) and then rapidly cooled by immersing it in a quenching medium such as water, oil, or air.
- The rapid cooling prevents the formation of softer microstructures, instead locking the metal into a harder state, such as martensite in steel.
-
Purpose of Quenching:
- The primary goal of quenching is to increase the hardness of the metal. This is achieved by altering the metal's microstructure, making it more resistant to deformation and wear.
- Quenching is particularly effective for steels, where it transforms the austenite phase into martensite, a hard and brittle structure.
-
Comparison with Other Heat Treatment Processes:
- Annealing: This process softens the metal, making it more ductile and easier to work with. It is the opposite of quenching in terms of hardness.
- Case Hardening: This increases surface hardness while maintaining a softer core, but it is not as effective as quenching for overall hardness.
- Tempering: Often performed after quenching, tempering reduces brittleness by slightly lowering hardness, but it is not the primary process for increasing hardness.
- Carburizing: This process adds carbon to the surface of the metal, increasing surface hardness, but it is not as universally applied as quenching.
-
Applications of Quenching:
- Quenching is widely used in the manufacturing of tools, such as hammers, chisels, and drill bits, where high hardness is essential for durability.
- It is also used in the automotive industry for components like gears, shafts, and springs, which require high wear resistance.
- In the aerospace industry, quenching is applied to critical components that must withstand extreme stress and wear.
-
Quenching Media and Their Effects:
- Water: Provides the fastest cooling rate, resulting in the highest hardness but also the highest risk of cracking or distortion.
- Oil: Offers a slower cooling rate, reducing the risk of cracking while still achieving significant hardness.
- Air: The slowest cooling medium, used for metals that are less prone to cracking but still require some level of hardness.
-
Challenges and Considerations:
- Quenching can introduce internal stresses and brittleness, which may require subsequent tempering to balance hardness with toughness.
- The choice of quenching medium and cooling rate must be carefully controlled to avoid defects like warping or cracking.
- Different metals and alloys require specific quenching techniques to achieve optimal results.
-
Why Quenching is the Most Common Process for Increasing Hardness:
- Quenching is the most direct and effective method for achieving high hardness levels in metals, especially steels.
- It is a well-understood and widely applicable process that can be tailored to meet the specific hardness requirements of various industries.
- While other processes like case hardening and tempering are important, they are often used in conjunction with quenching rather than as standalone methods for increasing hardness.
In summary, quenching stands out as the most common heat treatment process for increasing metal hardness due to its effectiveness, versatility, and widespread industrial applications.
Summary Table:
Aspect | Details |
---|---|
Definition | Rapid cooling of heated metal to lock it into a harder microstructure. |
Purpose | Increases hardness and wear resistance in metals, especially steels. |
Quenching Media | Water (fastest), oil (balanced), air (slowest). |
Applications | Tools, automotive components, aerospace parts. |
Challenges | Risk of cracking or distortion; requires careful control of cooling rates. |
Comparison | More effective than annealing, case hardening, and tempering for hardness. |
Need expert advice on heat treatment processes? Contact us today to optimize your metal hardening solutions!