Chemical vapor deposition (CVD) is a versatile and widely used method for synthesizing nanomaterials, particularly graphene and carbon nanotubes (CNTs). It involves the decomposition of gaseous precursors on a substrate, often catalyzed by a metal surface, to form thin films or nanostructures. CVD operates at medium temperatures (500–1100°C) and allows precise control over material properties by adjusting parameters like temperature, gas composition, and substrate type. This method is distinct from high-temperature techniques like electric arc discharge and laser vaporization, offering scalability and high purity, making it the preferred choice for industrial-scale production of nanomaterials such as graphene.
Key Points Explained:
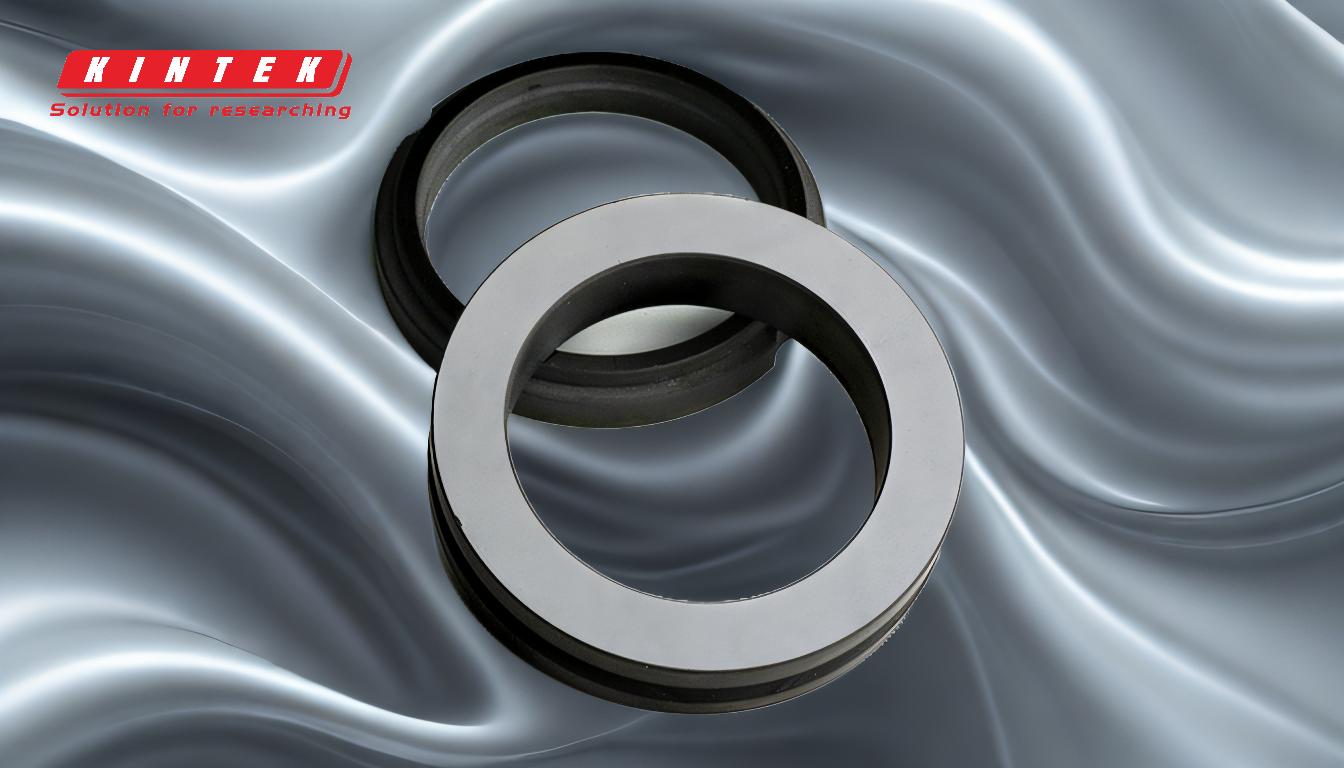
-
Definition and Process of CVD:
- CVD is a bottom-up synthesis method where gaseous precursors decompose on a substrate to form nanomaterials.
- The process involves introducing precursor gases into a reaction chamber under controlled conditions of temperature, pressure, and flow rate.
- A catalyst, typically a metal like copper (Cu), platinum (Pt), or iridium (Ir), activates the chemical reaction, enabling the formation of nanostructures like graphene or carbon nanotubes.
-
Key Components and Conditions:
- Precursor Gases: Carbon-bearing gases like methane are commonly used for graphene synthesis.
- Substrate: Metal foils (e.g., Cu) serve as both catalysts and surfaces for nucleation.
- Temperature: Medium temperatures (500–1100°C) are ideal for CVD, unlike high-temperature methods (>3000°C) used in arc discharge or laser vaporization.
- Pressure and Flow Rate: These parameters are carefully controlled to ensure uniform deposition and high-quality film formation.
-
Types of CVD:
- Thermal CVD: Relies on heat to activate the chemical reaction between precursor gases and the substrate.
- Plasma-Enhanced CVD (PECVD): Uses plasma to lower the reaction temperature, making it suitable for temperature-sensitive substrates.
-
Applications in Nanomaterial Synthesis:
- Graphene Production: CVD is the only method capable of producing large-area, monolayer graphene sheets on metal foils, which can then be transferred to other substrates.
- Carbon Nanotubes (CNTs): CVD is widely used for synthesizing single-walled and multi-walled CNTs with high purity and precision.
- Other Nanostructures: CVD can produce a variety of nanostructures with tailored properties by adjusting process parameters.
-
Advantages of CVD:
- Scalability: Suitable for industrial-scale production of nanomaterials.
- High Purity: Produces materials with minimal impurities.
- Precision Control: Allows fine-tuning of material properties by varying parameters like temperature, gas composition, and substrate type.
- Versatility: Capable of synthesizing a wide range of nanomaterials, including graphene, CNTs, and thin films.
-
Challenges and Considerations:
- Complexity: The process requires careful monitoring and control of multiple parameters.
- Cost: High-quality precursors and equipment can be expensive.
- Substrate Limitations: The choice of substrate and catalyst can influence the quality and properties of the synthesized material.
-
Comparison with Other Methods:
- Electric Arc Discharge and Laser Vaporization: These methods operate at extremely high temperatures (>3000°C) and are less suitable for large-scale production.
- Hydrothermal and Sol-Gel Methods: These are chemical synthesis techniques that are less precise and scalable compared to CVD.
-
Industrial Significance:
- CVD is the preferred method for producing graphene and CNTs on an industrial scale due to its ability to produce high-quality materials with consistent properties.
- It enables the synthesis of novel materials with applications in electronics, energy storage, and composite materials.
By leveraging the controlled environment of CVD, researchers and manufacturers can produce nanomaterials with tailored properties, making it a cornerstone of modern nanotechnology.
Summary Table:
Aspect | Details |
---|---|
Process | Decomposition of gaseous precursors on a substrate to form nanomaterials. |
Temperature Range | 500–1100°C, ideal for controlled synthesis. |
Key Components | Precursor gases, metal substrates, and catalysts like Cu, Pt, or Ir. |
Types of CVD | Thermal CVD, Plasma-Enhanced CVD (PECVD). |
Applications | Graphene, carbon nanotubes, and tailored nanostructures. |
Advantages | Scalability, high purity, precision control, and versatility. |
Challenges | Complexity, cost, and substrate limitations. |
Unlock the potential of nanomaterials with CVD—contact our experts today to learn more!