Diffusion in sintering is a critical process that involves the movement of atoms within a solid material, driven by the reduction in surface area and local curvature of the powder particles. This atomic movement is facilitated by heat and, in some cases, pressure, leading to the consolidation of powder particles without melting them. The process is essential for creating materials with enhanced properties such as hardness, toughness, and precision, and is widely used in manufacturing to produce complex shapes and geometries.
Key Points Explained:
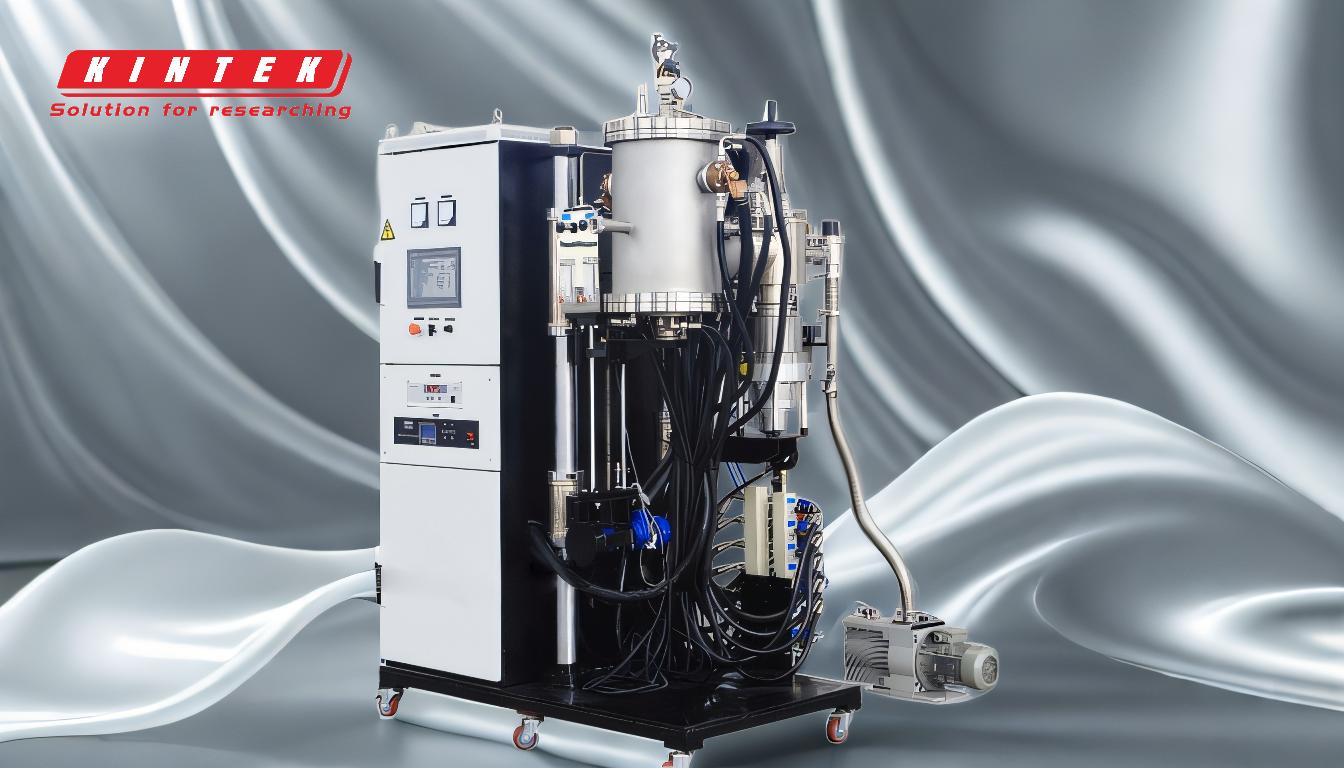
-
Definition of Diffusion in Sintering:
- Diffusion in sintering refers to the movement of atoms within a solid material, which is driven by the reduction in surface area. This process helps in consolidating powder particles, leading to the formation of a denser and more cohesive material.
-
Driving Forces for Diffusion:
- Reduction in Surface Area: The primary driving force for diffusion during sintering is the reduction in surface area. As atoms move, they tend to reduce the local curvature of the free surface, leading to the consolidation of powder particles.
- Heat and Pressure: Heat causes atoms to vibrate and move more freely, facilitating diffusion. Pressure, especially in techniques like hot pressing, can provide an additional driving force for the fusion of particles.
-
Atomic Movement and Diffusion:
- Atomic Vibration: When a solid material is heated, the atoms within it begin to vibrate more intensely. This increased vibration allows atoms to move through the material, a process known as atomic diffusion.
- Concentration Gradient: The rate of diffusion is influenced by the concentration gradient of atoms within the material. A steeper concentration gradient generally leads to a faster rate of diffusion.
-
Role of Heat Treatment:
- Homogeneous Distribution: During heat treatment, diffusion causes the atoms of the dissolved element to spread out, aiming to form a homogeneous distribution within the base metal's crystals.
- Phase Formation: If the alloy is cooled to an insoluble state, the atoms of the dissolved constituents may migrate out of the solution, leading to nucleation and the formation of a microstructure with two or more distinct phases.
-
Benefits of Sintering:
- Enhanced Material Properties: Sintering is crucial for producing components with superior hardness, toughness, and precision. It allows for the combination of different material properties, such as toughness and abrasion resistance.
- Complex Geometries: The process enables the creation of intricate shapes and geometries that are challenging to achieve with conventional manufacturing methods.
- Cost-Effective Manufacturing: Sintering allows for lower-cost tooling and rapid mass production while maintaining precision and repeatability.
-
Practical Example of Diffusion:
- Helium Balloons: A practical example of diffusion is the deflation of helium balloons. Helium atoms diffuse through the balloon wall and escape, illustrating the movement of atoms through a material.
-
Importance of Pressure in Sintering:
- Hot Pressing: Applying pressure during heat treatment, particularly in hot pressing, can significantly enhance the sintering process, especially for materials that are otherwise difficult to sinter.
By understanding these key points, one can appreciate the complexity and importance of diffusion in the sintering process, which is fundamental to modern manufacturing and material science.
Summary Table:
Key Aspect | Description |
---|---|
Definition | Movement of atoms within a solid material driven by surface area reduction. |
Driving Forces | Reduction in surface area, heat, and pressure. |
Atomic Movement | Atomic vibration and concentration gradient facilitate diffusion. |
Role of Heat Treatment | Promotes homogeneous distribution and phase formation. |
Benefits of Sintering | Enhanced hardness, toughness, precision, and cost-effective manufacturing. |
Practical Example | Helium balloons deflating due to atomic diffusion. |
Importance of Pressure | Hot pressing enhances sintering for difficult materials. |
Discover how sintering can transform your manufacturing process—contact our experts today!