Diode sputtering is a physical vapor deposition (PVD) technique used to create thin films on substrates by bombarding a target material with high-energy ions in a low vacuum environment. The process involves generating a plasma discharge through an electric potential difference between the target (cathode) and the substrate. Free electrons in the plasma collide with neutral gas atoms, ionizing them and accelerating them toward the target. This causes atoms to be ejected from the target and deposited onto the substrate, forming a thin film. Diode sputtering is widely used in industries such as semiconductors, optics, and aerospace due to its ability to produce high-quality, dense, and adherent coatings.
Key Points Explained:
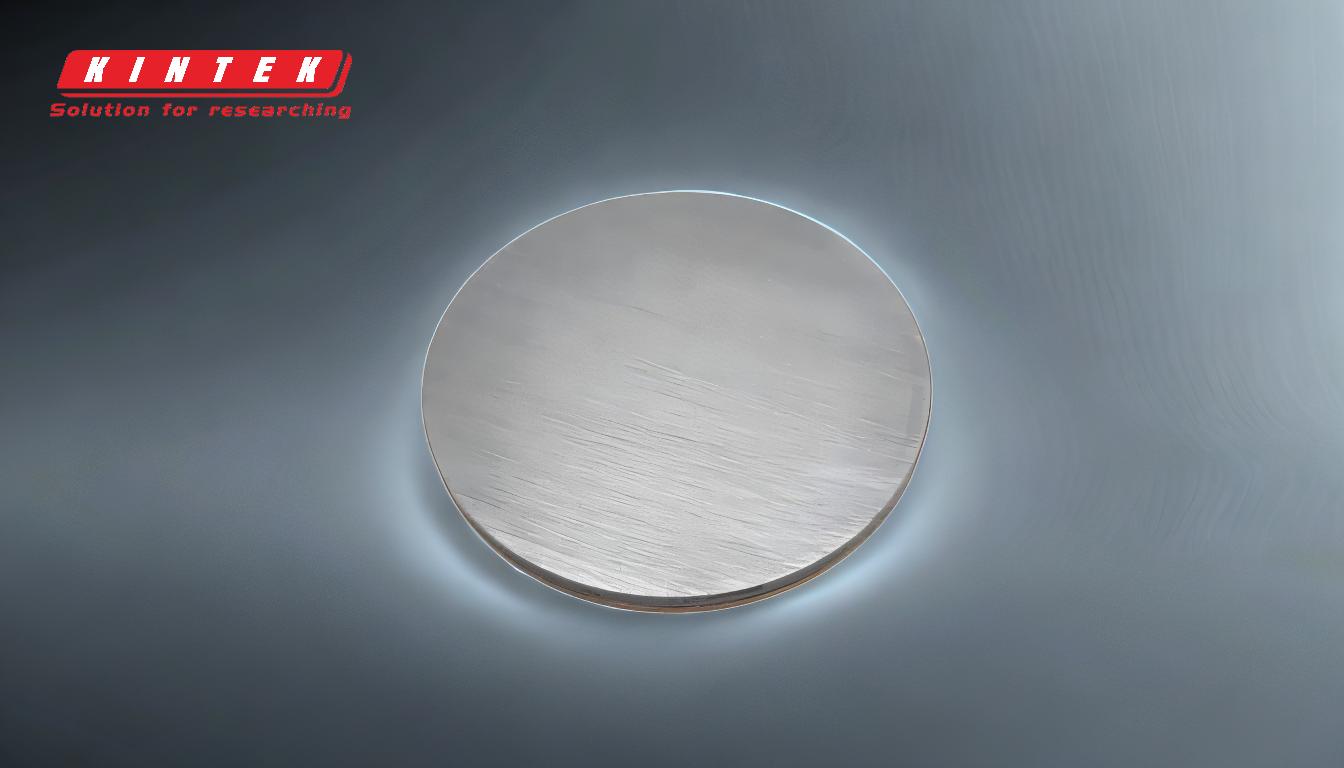
-
Basic Mechanism of Diode Sputtering:
- Diode sputtering relies on creating a plasma discharge in a low vacuum chamber by applying an electric potential difference between the target (cathode) and the substrate.
- Free electrons in the plasma are accelerated toward the cathode, colliding with neutral gas atoms (typically argon).
- These collisions ionize the gas atoms, turning them into positively charged ions.
- The positive ions are then accelerated toward the cathode, where they strike the target material, causing atoms to be ejected (sputtered) from its surface.
- The ejected material travels through the chamber and deposits onto the substrate, forming a thin film.
-
Glow Discharge and Plasma Formation:
- The plasma discharge is a critical component of diode sputtering. It is created by the ionization of gas atoms and the acceleration of electrons and ions.
- When positive ions return to their ground state, they absorb free electrons and release photons, producing a visible glow discharge.
- This glow discharge is an indicator of the plasma's presence and activity, ensuring the continuous ionization and sputtering process.
-
Applications of Diode Sputtering:
- Semiconductor Industry: Used for depositing thin films in semiconductor circuits and thin-film transistors.
- Optics: Applied in anti-reflective coatings for eyeglasses and low-emissivity coatings for architectural glass.
- Aerospace and Defense: Utilized for creating gadolinium films for neutron radiography and corrosion-resistant coatings.
- Medical Devices: Produces dielectric stacks to electrically isolate surgical tools and other medical equipment.
-
Advantages of Diode Sputtering:
- High-Quality Films: Produces dense, uniform, and adherent thin films with excellent material properties.
- Scalability: Suitable for large-scale production, such as in flat-panel displays and semiconductor wafer metallization.
- Versatility: Can deposit a wide range of materials, including metals, alloys, and dielectrics, in a single run.
- Line-of-Sight Deposition: Ideal for applications requiring precise, directional deposition, such as lift-off techniques.
-
Process Parameters and Control:
- Vacuum Level: Operates in a low vacuum environment to maintain plasma stability and minimize contamination.
- Gas Selection: Typically uses inert gases like argon to avoid chemical reactions with the target material.
- Power Supply: Requires precise control of the electric potential difference to regulate ion energy and deposition rate.
- Substrate Preparation: Ensures clean and smooth surfaces to enhance film adhesion and uniformity.
-
Comparison with Other Sputtering Techniques:
- Diode sputtering is one of the simplest and earliest forms of sputtering, making it cost-effective and easy to implement.
- Unlike more advanced techniques (e.g., magnetron sputtering), diode sputtering does not use magnetic fields to enhance plasma density, which can limit deposition rates and efficiency.
- However, it remains widely used for applications where simplicity, scalability, and cost-effectiveness are prioritized over high deposition rates.
-
Future Trends and Innovations:
- Ongoing research focuses on improving plasma efficiency and deposition rates through advanced power supplies and gas flow control.
- Integration with other PVD techniques, such as magnetron sputtering, to combine the benefits of both methods.
- Development of new target materials and gas mixtures to expand the range of applications and improve film properties.
In summary, diode sputtering is a foundational PVD technique with broad industrial applications. Its ability to produce high-quality thin films with strong adhesion and uniformity makes it indispensable in fields ranging from semiconductors to aerospace. While newer sputtering methods offer enhanced capabilities, diode sputtering remains a reliable and cost-effective solution for many production needs.
Summary Table:
Aspect | Details |
---|---|
Mechanism | Plasma discharge bombards target material, ejecting atoms for deposition. |
Applications | Semiconductors, optics, aerospace, medical devices. |
Advantages | High-quality, dense, adherent films; scalable; versatile. |
Process Parameters | Low vacuum, inert gases (e.g., argon), precise power control. |
Comparison | Simpler and cost-effective vs. advanced techniques like magnetron sputtering. |
Future Trends | Improved plasma efficiency, integration with other PVD techniques. |
Interested in leveraging diode sputtering for your projects? Contact us today to learn more!