A direct core-type induction furnace is a type of induction furnace that operates on the principle of a transformer at mains frequency. It consists of an iron core surrounded by a primary coil through which alternating current flows. This induces a larger current in a secondary coil formed by a loop of molten metal, generating heat via the Joule Effect. The furnace is highly efficient, with power efficiency reaching up to 98%. It is primarily used for melting and alloying metals, offering uniform composition and temperature with minimal melt losses. The design includes components such as a power supply, cooling system, and control system, making it suitable for industrial applications.
Key Points Explained:
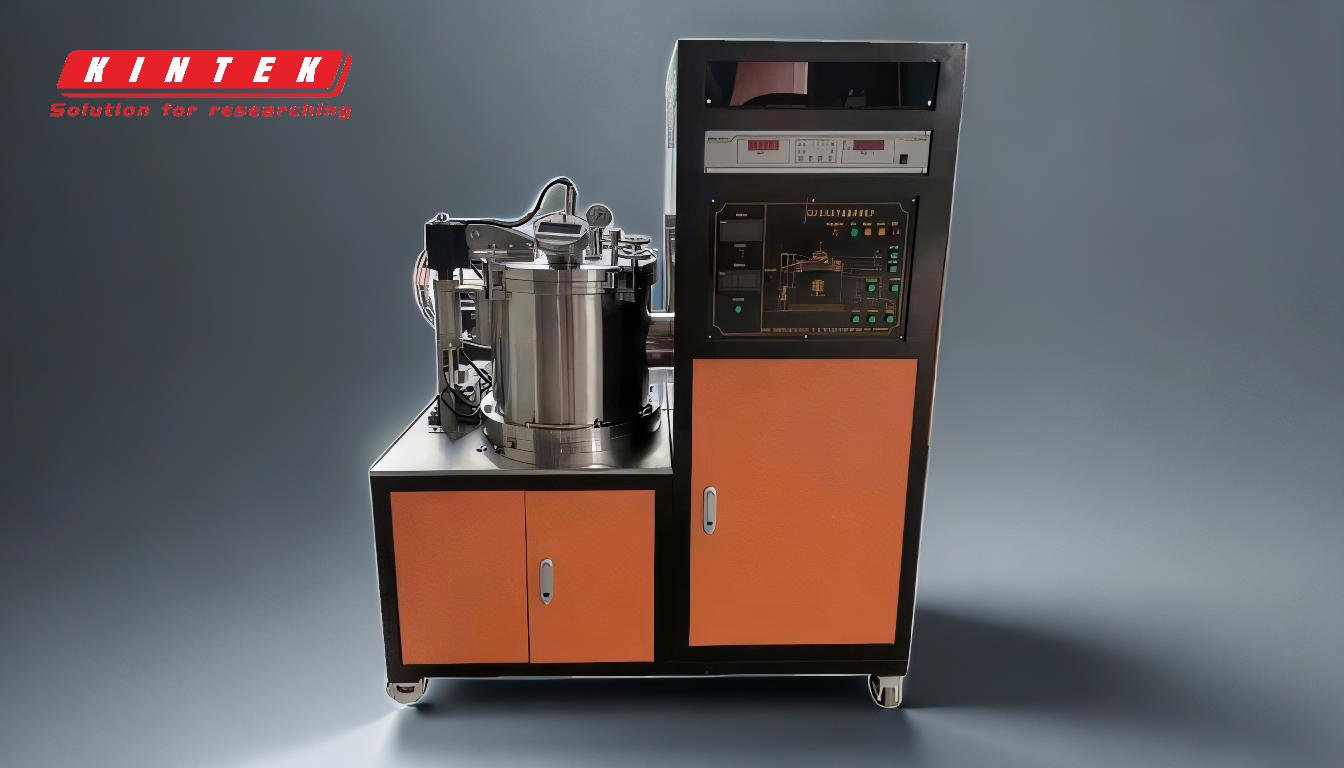
-
Operating Principle:
- The direct core-type induction furnace operates similarly to a transformer. An alternating current flows through a primary coil surrounding an iron core, inducing a larger current in a secondary coil formed by a loop of molten metal.
- This process generates heat through the Joule Effect, which is highly efficient, with power efficiency reaching up to 98%.
-
Components:
- Iron Core: The central component that enhances the magnetic field and improves efficiency.
- Primary Coil: Surrounds the iron core and carries the alternating current.
- Secondary Coil: Formed by a loop of molten metal, it carries the induced current.
- Power Supply Unit: Includes a transformer, inverter, and capacitor bank to supply and regulate the alternating current.
- Cooling System: Essential for maintaining the temperature of the power supply and furnace coil.
- Control System: Manages the operation and ensures uniform composition and temperature of the molten metal.
- Fume Extraction Equipment: Removes any fumes generated during the melting process.
-
Applications:
- Melting and Alloying: Ideal for melting and alloying a wide variety of metals with minimal melt losses.
- Uniform Composition and Temperature: Ensures that the molten metal has a uniform composition and temperature, which is crucial for high-quality casting and manufacturing processes.
-
Advantages:
- High Efficiency: With power efficiency up to 98%, it is one of the most efficient methods for melting metals.
- Minimal Melt Losses: The design and operation minimize the loss of material during the melting process.
- Uniform Heating: Provides uniform heating, which is essential for consistent quality in the final product.
-
Comparison with Coreless Induction Furnace:
- Coreless Induction Furnace: Uses a crucible surrounded by a water-cooled alternating current solenoid coil. It is simpler in design but less efficient compared to the core-type furnace.
- Core-Type Induction Furnace: Incorporates an iron core to enhance the magnetic field, making it more efficient and suitable for larger-scale operations.
-
Temperature Capabilities:
- Forging Heating Temperature: Can reach up to 1250°C.
- Melting Temperature: Can reach up to 1650°C, making it suitable for melting a wide range of metals.
-
Industrial Suitability:
- Versatility: Suitable for various industrial applications due to its ability to handle different metals and alloys.
- Scalability: Can be scaled to meet the demands of different production volumes, from small-scale operations to large industrial foundries.
In summary, the direct core-type induction furnace is a highly efficient and versatile tool for melting and alloying metals. Its design, which includes an iron core and primary and secondary coils, allows for uniform heating and minimal melt losses. With components like a power supply unit, cooling system, and control system, it is well-suited for industrial applications requiring high-quality metal processing.
Summary Table:
Feature | Details |
---|---|
Operating Principle | Transformer-like design with primary and secondary coils for efficient heating. |
Efficiency | Up to 98% power efficiency. |
Key Components | Iron core, primary coil, secondary coil, power supply, cooling system, control system. |
Applications | Melting and alloying metals with uniform composition and temperature. |
Temperature Range | Forging: Up to 1250°C; Melting: Up to 1650°C. |
Advantages | High efficiency, minimal melt losses, uniform heating. |
Industrial Suitability | Scalable and versatile for various metals and production volumes. |
Upgrade your metal processing with a direct core-type induction furnace—contact us today to learn more!