Direct current pulse magnetron sputtering (DC pulse sputtering) is an advanced variation of magnetron sputtering, a physical vapor deposition (PVD) technique used to create thin films on substrates. Unlike traditional DC magnetron sputtering, which uses a continuous direct current, DC pulse sputtering applies a pulsed DC power supply to the target material. This method combines the benefits of high deposition rates and precise control over film properties, making it particularly effective for depositing high-quality thin films, especially for materials that are challenging to sputter, such as dielectrics or insulators. The pulsed power helps reduce arcing and overheating, which are common issues in traditional DC sputtering, thereby improving film quality and process stability.
Key Points Explained:
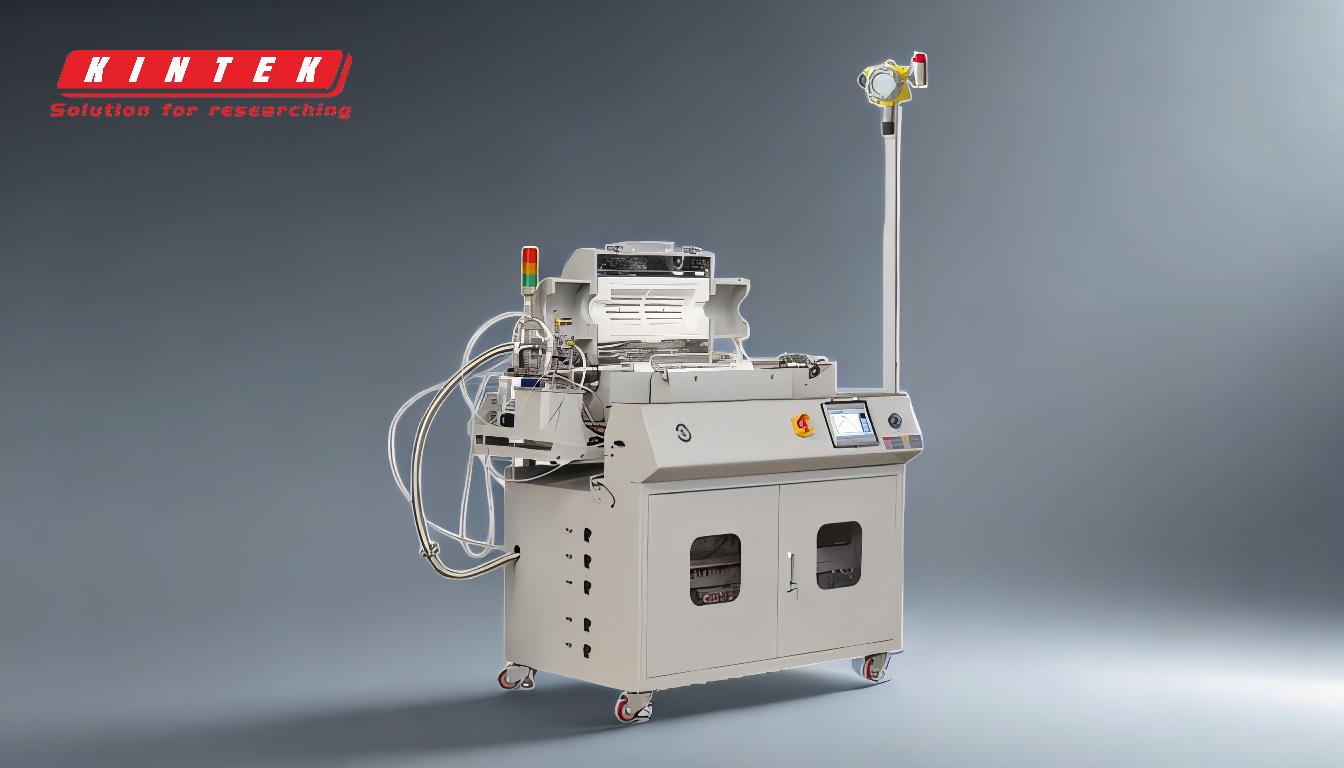
-
Basic Principle of Magnetron Sputtering:
- Magnetron sputtering is a plasma-based PVD method where a target material is bombarded with ions in a vacuum chamber, causing atoms to be ejected and deposited onto a substrate.
- The process involves the use of a magnetic field to confine electrons near the target, increasing the ionization of the sputtering gas (usually argon) and enhancing the efficiency of the sputtering process.
- This technique is known for its high deposition rates, excellent film quality, and ability to operate at low pressures (around 0.1 Pa).
-
Introduction to DC Pulse Magnetron Sputtering:
- DC pulse sputtering is a modification of traditional DC magnetron sputtering, where a pulsed DC power supply is used instead of a continuous DC supply.
- The pulsed power alternates between high and low voltage states, which helps manage heat buildup and reduces arcing, a common issue when sputtering insulating or dielectric materials.
- This method is particularly useful for depositing thin films of materials that are prone to charging or arcing, such as oxides, nitrides, and other insulators.
-
Advantages of DC Pulse Sputtering:
- Reduced Arcing: The pulsed nature of the power supply minimizes arcing, which can damage the target and degrade film quality.
- Improved Film Quality: By controlling the power pulses, DC pulse sputtering produces denser and more uniform films with fewer defects.
- Versatility: This method can be used to deposit a wide range of materials, including conductive, insulating, and dielectric films, making it suitable for applications in microelectronics, optics, and semiconductors.
-
Process Mechanism:
- In DC pulse sputtering, the target is connected to a pulsed DC power supply, which alternates between positive and negative voltage states.
- During the negative pulse, ions from the plasma are accelerated toward the target, causing sputtering of target atoms.
- During the positive pulse, the target is briefly discharged, preventing charge buildup and reducing the risk of arcing.
- The sputtered atoms travel through the vacuum chamber and deposit onto the substrate, forming a thin film.
-
Applications of DC Pulse Magnetron Sputtering:
- Microelectronics: Used for depositing dielectric and nitride films in semiconductor manufacturing.
- Optical Coatings: Ideal for creating thin films with specific optical properties, such as anti-reflective or reflective coatings.
- Decorative and Functional Coatings: Applied in industries requiring durable, high-quality coatings with precise thickness and uniformity.
-
Comparison with Other Sputtering Techniques:
- DC Magnetron Sputtering: Continuous DC power can lead to arcing and overheating, especially with insulating materials.
- RF Magnetron Sputtering: Suitable for non-conductive materials but typically has lower deposition rates compared to DC pulse sputtering.
- DC Pulse Sputtering: Combines the benefits of both DC and RF sputtering, offering high deposition rates, reduced arcing, and compatibility with a wide range of materials.
-
Future Developments:
- Ongoing research aims to optimize pulse parameters (frequency, duty cycle, and voltage) to further enhance film quality and deposition efficiency.
- Advances in power supply technology and process control are expected to expand the applications of DC pulse sputtering in emerging fields such as flexible electronics and energy storage.
By leveraging the unique advantages of DC pulse magnetron sputtering, manufacturers can achieve superior thin film deposition with greater precision and reliability, making it a valuable technique in modern materials science and engineering.
Summary Table:
Aspect | Details |
---|---|
Basic Principle | Plasma-based PVD method using a magnetic field to enhance sputtering efficiency. |
Key Advantage | Reduces arcing and overheating, improving film quality and process stability. |
Applications | Microelectronics, optical coatings, decorative and functional coatings. |
Comparison | Combines benefits of DC and RF sputtering, offering versatility and efficiency. |
Future Developments | Optimization of pulse parameters and expansion into flexible electronics. |
Unlock the potential of DC pulse magnetron sputtering for your projects—contact our experts today!