Field Assisted Sintering (FAS), also known as Field Assisted Sintering Technology (FAST) or Spark Plasma Sintering (SPS), is an advanced sintering technique that utilizes a direct current (DC) electric current to heat the mold and/or sample through Joule heating. This method enables rapid heating rates, reduced processing cycle times, and lower sintering temperatures and pressures compared to traditional sintering processes. By directly applying electrical power to the mold and powder, FAS enhances sintering activity, making it particularly effective for fine metal powders and complex materials.
Key Points Explained:
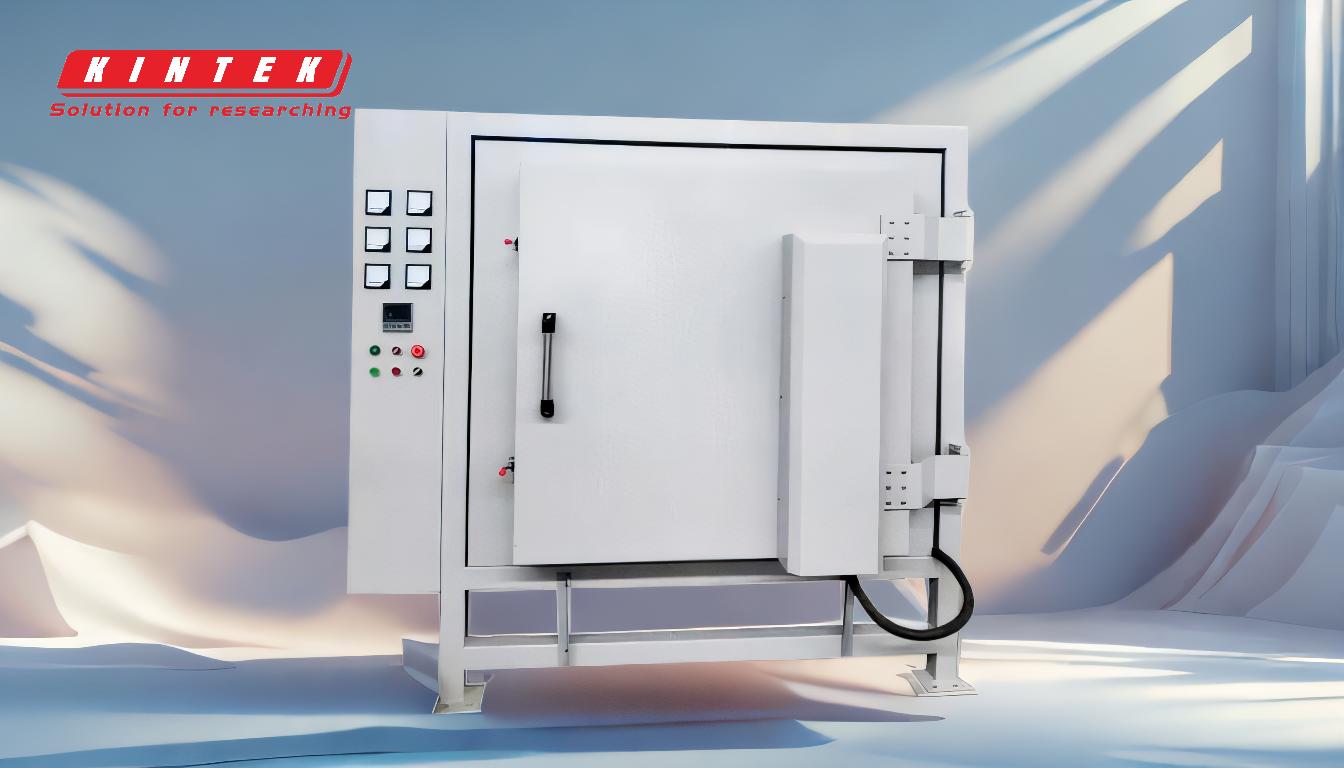
-
Definition and Mechanism of Field Assisted Sintering (FAS):
- FAS is a sintering process that employs a DC electric current to generate heat directly within the mold and/or sample through Joule heating.
- The electrical resistivity of the mold and the powder causes localized heating, which accelerates the sintering process.
- This method is also referred to as Spark Plasma Sintering (SPS) or direct hot pressing.
-
Key Advantages of FAS:
- High Heating Rates: The direct application of electrical current allows for extremely rapid heating, often reaching temperatures in seconds or minutes.
- Short Processing Cycle Times: The efficiency of FAS reduces the overall time required for sintering, making it suitable for high-throughput applications.
- Lower Sintering Temperatures and Pressures: FAS enables sintering at lower temperatures and pressures compared to conventional methods, which can reduce energy consumption and material degradation.
-
Applications and Materials:
- FAS is particularly effective for sintering fine metal powders, ceramics, and composite materials.
- It is widely used in the production of advanced materials, such as nanostructured materials, functionally graded materials, and complex geometries that are difficult to achieve with traditional sintering methods.
-
Comparison with Conventional Sintering:
- Heating Mechanism: In conventional sintering, heat is typically applied externally, leading to slower heating rates and longer cycle times.
- Energy Efficiency: FAS is more energy-efficient due to its direct heating mechanism and reduced processing times.
- Material Properties: FAS can produce materials with enhanced mechanical properties, such as higher density and improved grain structure, due to the rapid sintering process.
-
Technical Considerations:
- Mold Design: The mold used in FAS must be electrically conductive to allow the flow of current and generate heat. Common materials include graphite and other conductive ceramics.
- Control of Parameters: Precise control of current, temperature, and pressure is essential to achieve optimal sintering results and avoid defects such as overheating or incomplete densification.
-
Future Developments:
- Ongoing research is focused on further optimizing FAS for new materials and applications, including additive manufacturing and the sintering of nanomaterials.
- Advances in mold materials and process control systems are expected to enhance the capabilities and efficiency of FAS in the future.
In summary, Field Assisted Sintering is a highly efficient and versatile sintering technique that offers significant advantages over traditional methods, particularly for advanced materials and complex geometries. Its ability to achieve rapid heating, short cycle times, and lower sintering temperatures makes it a valuable tool in modern materials science and manufacturing.
Summary Table:
Aspect | Field Assisted Sintering (FAS) |
---|---|
Mechanism | Uses DC electric current for Joule heating, directly heating the mold and sample. |
Key Advantages | High heating rates, short cycle times, lower sintering temperatures and pressures. |
Applications | Fine metal powders, ceramics, composites, nanostructured materials, and complex geometries. |
Comparison to Conventional | Faster, more energy-efficient, and produces materials with enhanced mechanical properties. |
Technical Considerations | Requires conductive molds (e.g., graphite) and precise control of current, temperature, and pressure. |
Future Developments | Optimization for additive manufacturing, nanomaterials, and improved process control systems. |
Ready to enhance your material processing with FAS technology? Contact our experts today to learn more!