Furnace lining refers to the protective layer of refractory materials installed inside a furnace to withstand high temperatures, protect the furnace structure, and improve thermal efficiency. It is typically made from materials like alumina, silicon carbide, or ceramic fibers, which are chosen for their ability to resist heat damage, insulate the furnace, and maintain uniform process conditions. The lining design often includes multi-layer insulation to minimize heat loss and energy consumption. Furnace linings are critical in various types of furnaces, such as muffle and rotary furnaces, where they ensure durability, thermal insulation, and protection against corrosion.
Key Points Explained:
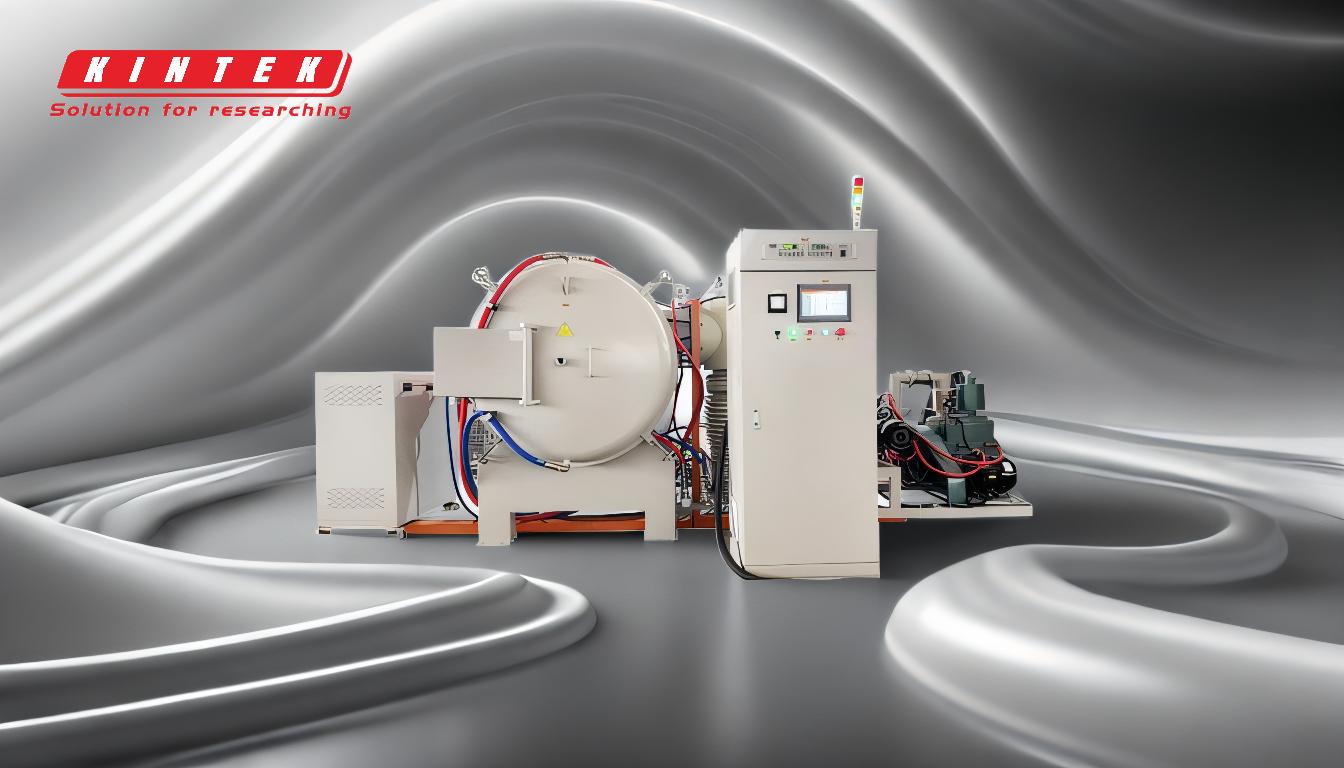
-
Definition and Purpose of Furnace Lining:
- Furnace lining is the inner layer of refractory materials that protects the furnace structure from high temperatures and thermal damage.
- It ensures uniform heating, reduces heat loss, and improves energy efficiency.
- The lining also acts as a barrier against corrosion and wear, extending the furnace's lifespan.
-
Common Materials Used in Furnace Linings:
- Alumina (AlO): A high-strength material that provides excellent thermal resistance and durability.
- Silicon Carbide (SiC): Known for its advanced heat resistance and ability to maintain uniform process conditions.
- Ceramic Fibers: Lightweight materials like alumina ceramic fibers offer superior insulation and rapid heat/cold resistance.
- Refractory Bricks, Cement, and Castables: Used in rotary furnaces to insulate the steel body and withstand temperatures up to 1000°C.
-
Design and Construction of Furnace Linings:
- Multi-layer insulation designs are common, combining materials like lightweight ceramic fibers and insulation boards.
- Vacuum-formed high-purity alumina fibers are used for their high service temperature and thermal insulation properties.
- Refractory linings in rotary furnaces often include a combination of bricks, cement, and castables for maximum efficiency and reduced skin temperature.
-
Benefits of Advanced Furnace Linings:
- Thermal Efficiency: Materials like alumina and ceramic fibers minimize heat loss, ensuring energy-efficient operation.
- Durability: High-purity materials resist cracking, slagging, and corrosion, even under extreme temperatures.
- Rapid Heating and Cooling: Lightweight linings with small heat storage capacity allow for faster temperature changes.
- Safety: Non-asbestos materials ensure safe operation and compliance with environmental standards.
-
Applications in Different Furnace Types:
- Muffle Furnaces: Typically lined with alumina or silicon carbide to protect the chamber from high temperatures.
- Rotary Furnaces: Use refractory bricks, cement, or castables to insulate the steel barrel and withstand temperatures up to 1000°C.
- High-Temperature Furnaces: Employ monolithic refractory metals or graphite retorts in the hot zone for superior performance.
-
Key Considerations for Purchasers:
- Material Selection: Choose materials based on the required temperature range, thermal efficiency, and durability.
- Design Features: Look for multi-layer insulation and lightweight materials for improved performance.
- Safety and Compliance: Ensure the lining materials are free from hazardous components like asbestos.
- Maintenance and Lifespan: Opt for linings with high resistance to cracking and corrosion to reduce maintenance costs and extend furnace life.
By understanding these key points, equipment and consumable purchasers can make informed decisions when selecting furnace linings that meet their specific operational needs.
Summary Table:
Aspect | Details |
---|---|
Purpose | Protects furnace structure, ensures uniform heating, and improves efficiency |
Common Materials | Alumina, Silicon Carbide, Ceramic Fibers, Refractory Bricks/Cement/Castables |
Design Features | Multi-layer insulation, lightweight materials, high-purity alumina fibers |
Benefits | Thermal efficiency, durability, rapid heating/cooling, safety compliance |
Applications | Muffle furnaces, rotary furnaces, high-temperature furnaces |
Key Considerations | Material selection, design features, safety, maintenance, and lifespan |
Ready to enhance your furnace's performance? Contact us today for expert guidance on the best furnace lining solutions!