Gas pressure sintering is a specialized sintering process that involves the application of high-pressure gas during the sintering of materials, typically ceramics or metals, to enhance densification and improve material properties. This technique is particularly useful for materials that are difficult to sinter using conventional methods due to their high melting points or other challenging characteristics. The process involves heating the material in a controlled environment while applying gas pressure, which helps in reducing porosity and achieving a more uniform and dense microstructure.
Key Points Explained:
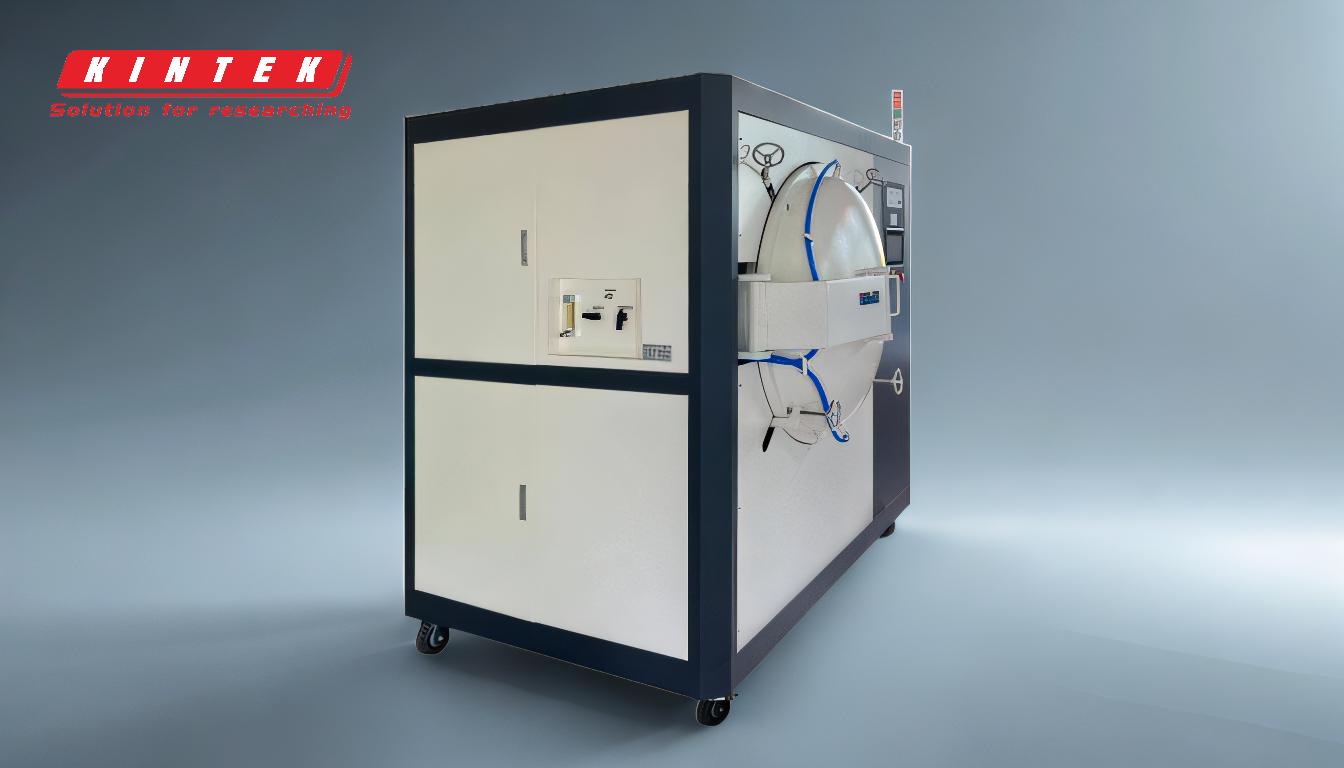
-
Definition and Purpose of Gas Pressure Sintering:
- Gas pressure sintering is a process where materials are sintered under high-pressure gas conditions to improve densification and material properties.
- It is particularly beneficial for materials with high melting points or those that are difficult to sinter using traditional methods.
-
Process Mechanism:
- The material is heated in a controlled environment, typically within a furnace designed to withstand high pressures.
- High-pressure gas, often inert gases like argon or nitrogen, is introduced to the sintering chamber.
- The gas pressure aids in the diffusion of atoms across particle boundaries, promoting densification and reducing porosity.
-
Advantages of Gas Pressure Sintering:
- Enhanced Densification: The application of gas pressure helps in achieving higher density and better mechanical properties.
- Improved Microstructure: The process results in a more uniform and fine-grained microstructure, which enhances the material's performance.
- Versatility: Suitable for a wide range of materials, including ceramics and high-melting-point metals.
-
Applications:
- Ceramics: Used in the production of advanced ceramics for applications in electronics, aerospace, and biomedical fields.
- Metals: Applied in the sintering of high-performance alloys and refractory metals like tungsten and molybdenum.
-
Comparison with Conventional Sintering:
- Pressure Application: Unlike conventional sintering, gas pressure sintering involves the application of external pressure, which significantly enhances the sintering process.
- Environment Control: The use of controlled gas environments prevents oxidation and other undesirable reactions, leading to better material quality.
-
Challenges and Considerations:
- Equipment Requirements: Specialized furnaces capable of withstanding high pressures and temperatures are required.
- Process Control: Precise control of temperature, pressure, and gas composition is essential to achieve the desired material properties.
- Cost: The process can be more expensive due to the need for advanced equipment and controlled environments.
In summary, gas pressure sintering is a sophisticated technique that leverages high-pressure gas to enhance the sintering process, resulting in materials with superior density, microstructure, and overall performance. This method is particularly valuable for advanced materials used in high-tech industries.
Summary Table:
Aspect | Details |
---|---|
Definition | Sintering process using high-pressure gas to enhance material properties. |
Key Benefits | - Enhanced densification - Improved microstructure - Material versatility |
Applications | - Advanced ceramics (electronics, aerospace) - High-performance metals |
Challenges | - Specialized equipment - Precise process control - Higher costs |
Interested in optimizing your material performance with gas pressure sintering? Contact our experts today to learn more!