Heat treatment is a process used to alter the physical and sometimes chemical properties of a material, typically metals, through controlled heating and cooling. It offers numerous advantages, such as improving hardness, strength, and wear resistance, while also enhancing machinability and ductility. However, it also has disadvantages, including potential distortion, increased costs, and limitations in material selection. Understanding the pros and cons of heat treatment is essential for optimizing material performance in various applications.
Key Points Explained:
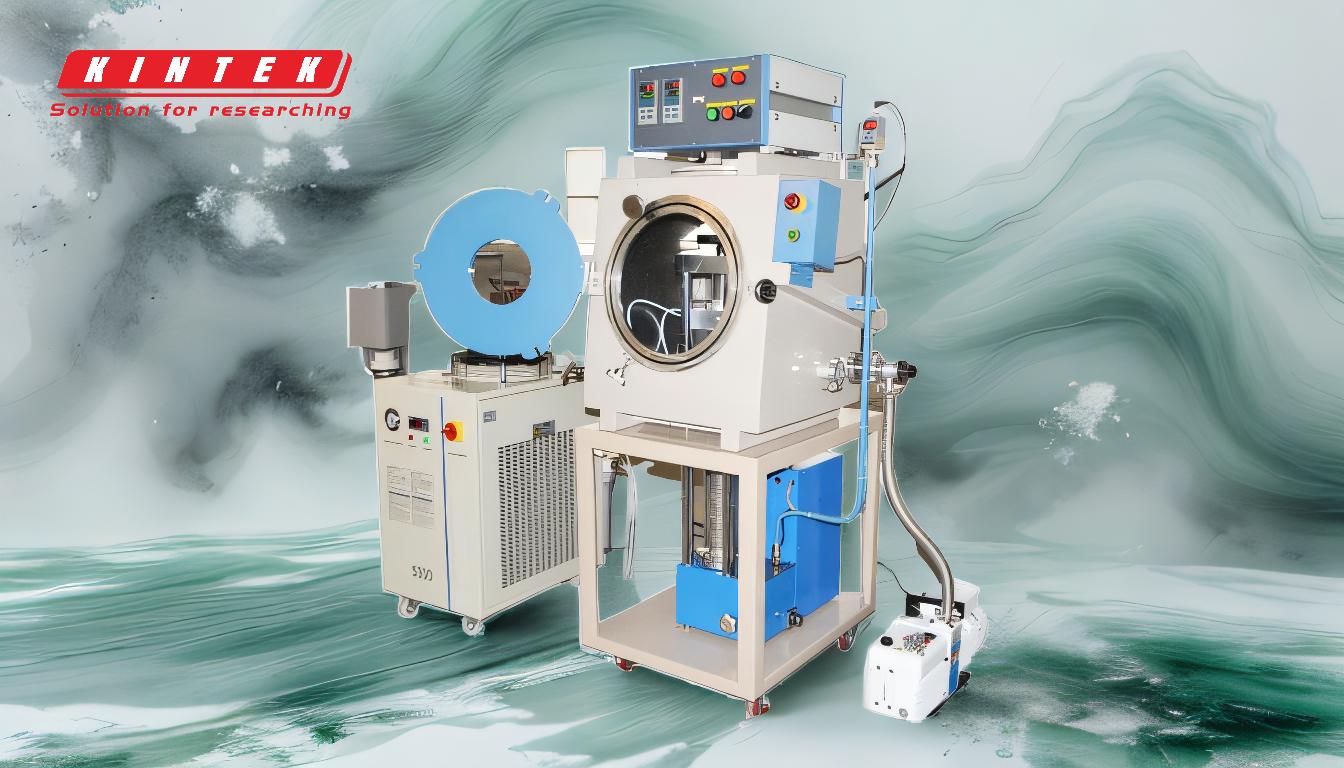
-
Advantages of Heat Treatment:
-
Improved Mechanical Properties:
- Heat treatment can significantly enhance the hardness, strength, and toughness of materials. For example, processes like quenching and tempering increase the hardness of steel, making it suitable for tools and machinery.
-
Enhanced Wear Resistance:
- By altering the microstructure, heat treatment can improve a material's resistance to wear and tear, extending its lifespan in demanding applications.
-
Increased Machinability:
- Certain heat treatment processes, such as annealing, soften materials, making them easier to machine and shape without excessive tool wear.
-
Improved Ductility and Toughness:
- Processes like normalizing and annealing can refine grain structures, improving ductility and toughness, which are critical for materials subjected to impact or stress.
-
Tailored Material Properties:
- Heat treatment allows customization of material properties to meet specific application requirements, such as corrosion resistance or electrical conductivity.
-
Improved Mechanical Properties:
-
Disadvantages of Heat Treatment:
-
Risk of Distortion and Warping:
- Rapid heating or cooling during processes like quenching can cause uneven stresses, leading to distortion or warping of the material.
-
Increased Costs:
- Heat treatment requires specialized equipment, energy, and skilled labor, which can increase production costs.
-
Material Limitations:
- Not all materials respond well to heat treatment. For instance, some alloys may become brittle or lose their desired properties after treatment.
-
Surface Oxidation and Decarburization:
- Exposure to high temperatures can cause surface oxidation or decarburization, reducing the material's surface quality and performance.
-
Complexity and Time-Consuming:
- Heat treatment processes often require precise control of temperature, time, and cooling rates, making them complex and time-consuming.
-
Risk of Distortion and Warping:
-
Applications and Considerations:
-
Industrial Applications:
- Heat treatment is widely used in industries such as automotive, aerospace, and manufacturing to produce components with enhanced performance and durability.
-
Material Selection:
- The choice of material and heat treatment process must align with the intended application to achieve the desired properties without compromising performance.
-
Process Optimization:
- Proper optimization of heat treatment parameters, such as temperature and cooling rate, is crucial to minimize disadvantages and maximize benefits.
-
Industrial Applications:
By carefully weighing the advantages and disadvantages, heat treatment can be effectively utilized to achieve superior material performance while mitigating potential drawbacks.
Summary Table:
Aspect | Advantages | Disadvantages |
---|---|---|
Mechanical Properties | Enhances hardness, strength, and toughness | Risk of distortion and warping |
Wear Resistance | Improves resistance to wear and tear | Increased costs due to specialized equipment and labor |
Machinability | Softens materials, making them easier to machine | Material limitations (some alloys may become brittle) |
Ductility & Toughness | Refines grain structures, improving ductility and toughness | Surface oxidation and decarburization |
Customization | Tailors material properties for specific applications | Complexity and time-consuming processes |
Ready to optimize your material performance? Contact us today to learn more about heat treatment solutions!